In machining, countersink and counterbore holes are essential for creating precise and functional assemblies, but they serve different purposes. A countersink hole is conical and designed to accommodate flat-head screws, ensuring the screw sits flush with or below the surface. A counterbore hole, on the other hand, is cylindrical and provides space for a bolt head or washer to sit flush or recessed.
Choosing the right one can impact the finished product’s overall performance, aesthetics, and structural integrity. This article explores the differences between countersink and counterbore holes and their specific characteristics, advantages, and best-use cases.
What is a Countersink Hole?
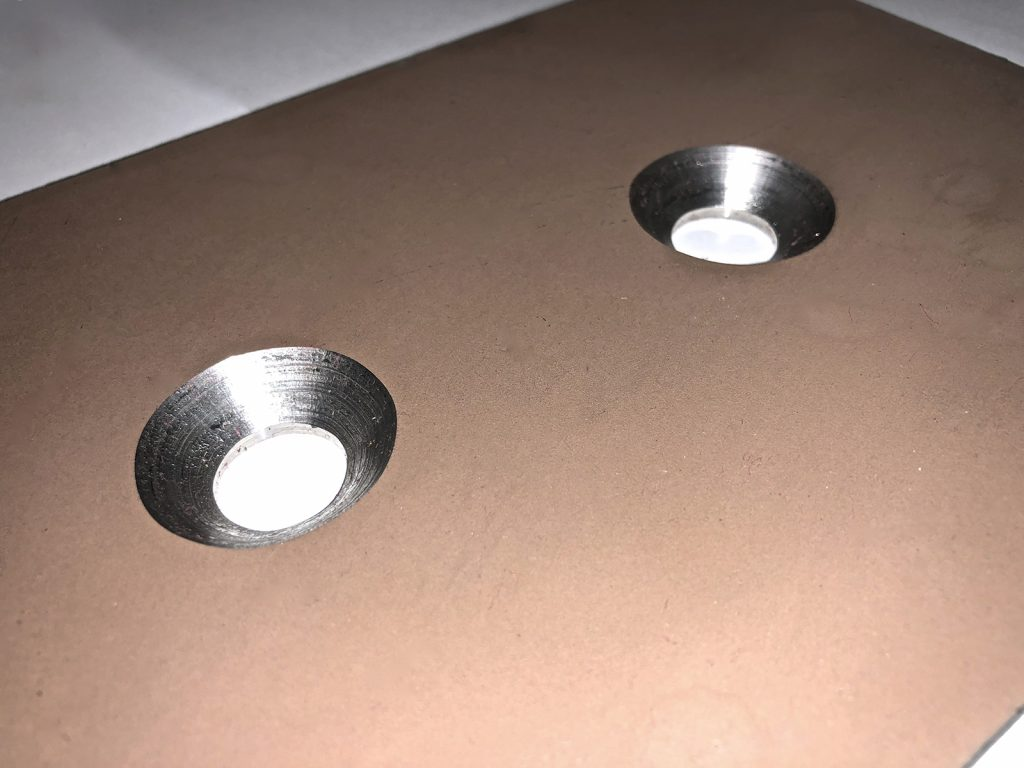
A countersink hole is designed with a conical-shaped entry that allows a flat-head screw or fastener to sit flush or slightly below the surface of the material. This type of hole is typically created using a countersink drill bit, which cuts a V-shaped profile at the opening of the drilled hole.
Features of Countersink Holes
- Conical Shape: Countersink holes feature a conical depression, typically at a 90-degree or 120-degree angle, depending on the screw head type. This specific shape facilitates the optimal seating of the fastener, ensuring that it aligns correctly with the material surface.
- Flush or Recessed Surface: The hole allows screws or fasteners to sit flush with the surface, providing a smooth, clean finish. This flush design is especially beneficial for components that require a neat appearance, as it prevents any protrusions that might interfere with other parts or mechanisms.
- Improved Aesthetics: The flush finish enhances the appearance of the assembled parts, making it suitable for applications where visual appeal is important. In consumer products, such as electronics or furniture, aesthetics can significantly impact marketability.
- Reduced Stress Concentration: The angled entry of the hole helps distribute forces evenly, reducing the chances of cracking or material deformation. This is crucial in applications where the material may be subject to varying loads or stress during use.
- Versatility: Countersink holes can be used in various materials, including wood, metal, and plastics. Their versatility makes them suitable for different industries and applications.
- Enhanced Grip: The conical shape of the countersink provides a better grip for the screw head, ensuring that it remains securely in place. This feature is especially important in applications where vibration or movement could loosen fasteners over time.
When to Use Countersink Holes
- When Appearance Matters: Use countersink holes when a flush or smooth surface finish is required, such as in consumer electronics, cabinetry, or decorative hardware. The visually appealing outcome is often a priority in such applications, making countersink holes an excellent choice.
- For Surface-Level Fastening: They are ideal for joining components where fasteners should not protrude above the surface, like in hinges or mounting brackets. This characteristic prevents snagging or interference with other mechanical parts.
- Preventing Material Damage: The conical profile of the countersink helps to reduce stress around the hole, making it suitable for brittle materials like plastic or glass. In delicate assemblies, this stress reduction is vital to maintaining structural integrity.
- Facilitating Easy Disassembly: Countersink holes allow for easy access to screws, facilitating quick assembly and disassembly. This is particularly advantageous in applications requiring regular maintenance or part replacement, such as electronic devices or machinery.
- Improving Resistance to Corrosion: In metal applications, countersink holes can help improve resistance to corrosion by allowing for better sealing of the fastener against environmental factors. When used with appropriate coatings or sealants, they can significantly enhance the durability of the assembly.
- Accommodating Washers: Countersink holes can also be used in conjunction with flat washers to further distribute the load from the screw head, enhancing the overall strength of the joint. This combination is particularly useful in heavy-duty applications where the integrity of the fastening is crucial.
- Integration with Other Fastening Methods: Countersink holes can be combined with other fastening techniques, such as adhesive bonding, to provide additional strength and stability in assemblies. This hybrid approach allows for more flexibility in design and application.
- Supporting Precision Assembly: In high-precision industries, such as aerospace or automotive, countersink holes ensure that fasteners fit perfectly, reducing the risk of misalignment and improving the reliability of the assembly. This precision is essential for components that must withstand rigorous operational conditions.
Countersink holes play a vital role in various applications across multiple industries, providing not only aesthetic advantages but also functional benefits. Understanding when and how to use them can significantly enhance the quality and performance of assembled products. Whether for consumer goods, industrial machinery, or specialized equipment, the importance of countersink holes cannot be overstated.
What is a Counterbore Hole?
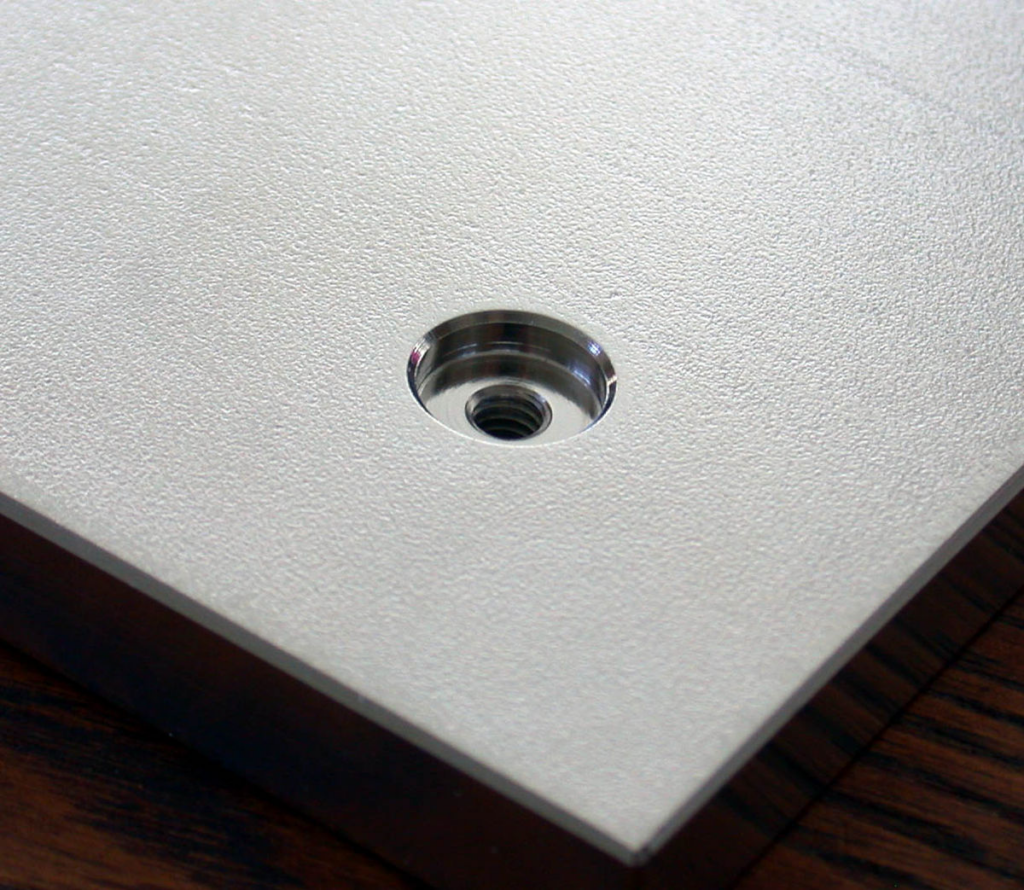
A counterbore hole is characterized by a cylindrical recess that allows a socket head or similar fastener to sit below the surface of the material. This type of hole is created using a counterbore tool, which drills a flat-bottomed cavity above the main hole. The design of a counterbore hole is integral for applications where aesthetics and structural integrity are crucial.
Features of Counterbore Holes
- Cylindrical Recess: The primary feature is a flat-bottomed cylindrical recess, designed to accommodate the head of a bolt or fastener. This design ensures that the fastener sits securely below the surface, providing a clean finish and preventing interference with adjacent components.
- Increased Stability: The flat-bottomed design provides a larger surface area for the fastener head to bear against, resulting in increased stability and strength. This added stability is essential in applications that experience dynamic loads or vibrations.
- Mechanical Strength: Counterbore holes offer better resistance to shear forces, making them ideal for structural applications. This enhanced strength is particularly valuable in heavy-duty settings, such as construction and manufacturing, where safety and reliability are paramount.
- Consistent Alignment: The recessed profile ensures consistent alignment of components, preventing misalignment or movement during assembly. This feature is critical in precision engineering, where even minor misalignments can lead to functional issues.
- Accommodates Larger Fasteners: Counterbore holes are designed to fit larger fasteners, such as socket head cap screws. This capability allows for the use of more robust fasteners, which can enhance the overall durability of the assembly.
When to Use Counterbore Holes
- Structural Applications: Counterbore holes are ideal for heavy-duty applications that require strong joints, such as machinery assembly or metal frameworks. Their design ensures that the connection can withstand significant forces without failure.
- When Using Socket Head Screws: They accommodate socket head cap screws or other large-headed fasteners that need to sit below the surface. This is particularly useful in applications where a smooth surface is desired, reducing the risk of snagging or interference.
- For Mechanical Support: Use counterbore holes when the joint requires extra support and load-bearing capacity. This makes them suitable for critical components in machinery, automotive parts, and aerospace applications.
- Facilitating Maintenance: The design of counterbore holes allows for easy access to fasteners for maintenance and repair. This is especially important in assemblies that require frequent disassembly for inspection or part replacement.
- Enhanced Aesthetic Appeal: In applications where the appearance of the final product is important, counterbore holes provide a clean and finished look. This aesthetic advantage is often required in consumer products and decorative items.
- Improved Resistance to Corrosion: When used in conjunction with the appropriate sealing techniques, counterbore holes can improve the resistance of fasteners to corrosion, as the fastener head is recessed and less exposed to environmental elements.
- Supporting High Torque Applications: Counterbore holes allow for the use of larger, more robust fasteners, which can handle higher torque levels without failure. This is essential in applications requiring significant clamping force or load-bearing capability.
Counterbore holes serve essential roles in various applications, providing not only structural advantages but also aesthetic benefits. Understanding their features and appropriate usage can enhance the performance and reliability of assembled products across numerous industries. Whether in heavy machinery, automotive components, or consumer goods, the significance of counterbore holes is substantial, ensuring the integrity and longevity of assemblies.
Countersink vs Counterbore Holes: Differences Comparison
While both countersink and counterbore holes are used for accommodating fasteners, they differ significantly in terms of design, function, and application. Understanding these differences will help in choosing the right hole type for your specific requirements.
Design Differences
Both countersink and counterbore holes serve distinct purposes in fastening applications and differ primarily in shape. Countersink holes feature a conical profile with a V-shaped entry, allowing flat-head screws to sit flush or slightly below the surface. This design enhances aesthetics, making it ideal for visible applications.
Additionally, countersink holes can be made with various angle options, commonly 90 or 120 degrees, to match the specific head shapes of the fasteners used. In contrast, counterbore holes are characterized by a cylindrical shape with a flat-bottomed cavity, specifically designed to accommodate socket head cap screws or hex bolts.
The flat bottom of counterbore holes maximizes surface contact, providing increased stability and strength in structural applications. This design consideration is essential in high-load scenarios, as it distributes forces more evenly across the fastener head.
Function
Functionally, countersink holes allow fasteners to fit flush with the material surface, offering a neat appearance that is particularly beneficial in woodworking and decorative applications. They reduce snagging and create a smooth finish, which is crucial in areas where safety and aesthetics are priorities.
Conversely, counterbore holes are engineered to allow the heads of larger fasteners to sit below the surface, enhancing mechanical strength and support. This design is essential in applications where structural integrity is critical, minimizing the risk of failure under stress. Furthermore, counterbore holes can often accommodate washer-like features that can further distribute the load, improving joint durability.
Usage Differences
In terms of application, countersink holes are ideal for situations where aesthetics and surface-level fastening are crucial, such as in cabinetry and consumer electronics. They provide a clean finish that enhances the overall look of the assembled product and can often be painted or finished without visible fasteners.
On the other hand, counterbore holes are best suited for heavy-duty applications requiring strong joints, like machinery assembly or metal frameworks. Their ability to accommodate larger fasteners ensures robust connections essential for handling significant loads and stresses, making them a popular choice in the construction and automotive industries.
Cost and Manufacturing Differences
From a cost perspective, countersink holes generally require less material removal, making them more economical to produce. This cost-effectiveness is advantageous for projects with budget constraints, especially when high quantities of fasteners are needed. In comparison, counterbore holes typically involve more machining steps, resulting in higher production costs due to the need for more advanced tooling and setup.
Additionally, the manufacturing complexity of these hole types varies; countersink holes are easier to produce due to their simpler profiles, while counterbore holes necessitate precise machining to achieve the flat-bottomed cavity, which adds to the overall complexity and expense. Manufacturers must consider these factors when selecting the hole type, balancing the specific application requirements with budget constraints and production capabilities.
Contrast Table
Feature | Countersink Hole | Counterbore Hole |
Shape | Conical, V-shaped entry | Cylindrical, flat-bottomed cavity |
Surface Finish | The fastener sits flush or below the surface | The fastener head sits below the surface |
Application | Woodworking, decorative assemblies, electronics | Structural applications, heavy machinery |
Fastener Compatibility | Flat-head screws, oval-head screws | Socket head cap screws, hex bolts |
Primary Benefit | Enhanced aesthetics, reduced stress concentration | Increased mechanical strength, alignment stability |
Manufacturing Complexity | Simple, cost-effective | More complex, relatively higher cost |
Typical Material | Plastic, wood, light metals | Steel, aluminum, heavy metals |
Common Usage | Decorative hardware, electronics housings | Machinery assembly, automotive parts |
Conclusion
Understanding the key differences between countersink and counterbore holes is essential for making informed decisions in machining and assembly projects. While countersink holes provide a flush, aesthetically pleasing finish, counterbore holes offer superior mechanical strength and stability for structural applications. Selecting the right type of hole based on the intended use and fastener type will ensure optimal performance and reliability.
For businesses seeking precision machining services, Zintilon offers comprehensive solutions, including countersinking and counterboring. With a commitment to quality and customer satisfaction, Zintilon’s skilled team ensures that every component is manufactured to the highest standards, making it a reliable partner for all your machining needs.
Great, Together