In metal surface treatments, two processes stand out for their ability to enhance durability and corrosion resistance: anodizing and chemical film. As you go through the complexities of metal finishing, understanding these techniques is crucial for making informed decisions about your projects.
So, it’s important to know what’s the difference between anodizing and chemical film. Well, the key difference is the result you get from them. Anodizing creates a thicker, harder oxide layer, while chemical film forms a thinner, less durable layer
Learn the differences in detail and be thoroughly informed to pick the right finish techniques for your projects.
What is Anodizing?
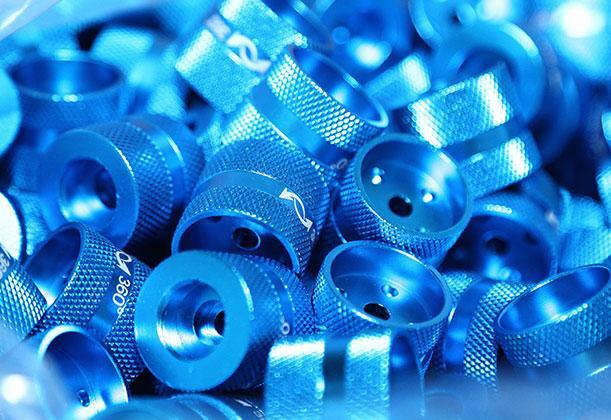
Anodizing is an electrochemical process that transforms the surface of the metal, particularly aluminum, into a durable, corrosion-resistant oxide layer. This technique doesn’t just coat the metal; it actually changes its surface structure, creating a layer that’s integral to the metal itself.
Features
When you opt for anodizing, you’re choosing a process with a unique set of characteristics:
- Integral Surface Layer: Unlike paint or plating, the anodized layer becomes part of the metal itself. This integration ensures exceptional adherence and durability.
- Customizable Thickness: You can control the thickness of the anodized layer, typically ranging from 0.0002 to 0.001 inches. This flexibility allows you to tailor the finish to your specific requirements.
- Porous Structure: The anodized surface features a microscopic porous structure. This porosity not only accepts dyes and sealants but also contributes to the finish’s unique properties.
- Colour Options: While natural anodizing produces a clear finish, you have the option to introduce vibrant colors through dye processes. The porous nature of the anodized layer allows for deep, lasting coloration.
- Electrical Insulation: The oxide layer created during anodizing serves as an excellent electrical insulator, a property that’s particularly valuable in certain electronic applications.
- Heat Dissipation: Contrary to popular belief, anodized surfaces can actually improve heat dissipation in some cases, making it an interesting choice for thermal management applications.
Applications
The versatility of anodizing makes it suitable for a wide range of applications:
- Aerospace: You’ll find anodized components in aircraft structures, where the lightweight nature of aluminum combines with the protective properties of anodizing.
- Architecture: Anodized aluminum is extensively used in building facades, window frames, and decorative elements, offering both aesthetic appeal and weather resistance.
- Consumer Electronics: Your smartphones, laptops, and tablets likely feature anodized aluminum casings, providing a sleek look and scratch resistance.
- Cookware: Many high-end pots and pans utilize anodized aluminum for its non-stick properties and durability.
- Sporting Goods: From bicycle frames to fishing reels, anodized components offer lightweight strength and corrosion resistance in outdoor gear.
- Industrial Machinery: Anodizing protects critical components in harsh industrial environments, extending the life of equipment.
- Automotive: You’ll see anodized parts in both exterior and interior automotive applications, from wheel rims to trim pieces.
- Marine Equipment: The corrosion resistance of anodized aluminum makes it ideal for boat parts and marine accessories.
Pros
When considering anodizing, you’ll benefit from several advantages:
- The integrated nature of the anodized layer provides exceptional wear resistance.
- Anodizing significantly enhances the metal’s ability to withstand corrosive environments.
- With a range of color options and finishes, you can achieve the desired look for your product.
- Anodized surfaces are easy to clean and maintain their appearance over time.
- The process uses fewer harmful chemicals compared to many other metal finishing techniques.
Cons
Despite its many benefits, anodizing does have some limitations:
- For small production runs, anodizing can be more expensive than some alternative finishes.
- Achieving exact colour matches can be challenging, especially across different batches.
What is Chemical Film?
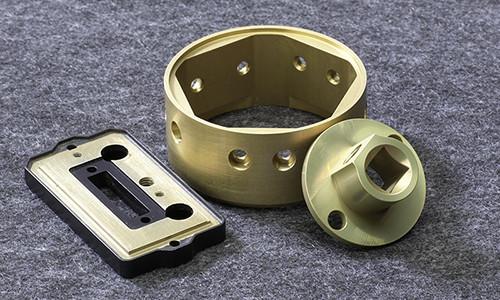
Chemical film, often referred to as chromate conversion coating, is a chemical process that creates a protective layer on metal surfaces. Unlike anodizing, chemical film doesn’t require an electrical current and relies solely on chemical reactions to form the protective coating.
Features
When you choose chemical film treatment, you’re opting for a process with distinct characteristics:
- Thin Protective Layer: Chemical film creates an extremely thin layer, typically measuring only a few micrometers in thickness.
- Self-Healing Properties: The chromate in the film can provide some self-healing capabilities, offering continued protection even if the surface is slightly scratched.
- Uniform Coverage: Chemical film excels at providing even coverage, even on complex shapes and in recessed areas.
- Color Indication: The color of the chemical film can indicate the level of protection, with darker colors generally offering more corrosion resistance.
- Electrical Conductivity: Unlike anodizing, chemical film maintains the electrical conductivity of the base metal.
- Paint Adhesion: Chemical film provides an excellent base for paint adhesion, making it a popular choice for priming surfaces before painting.
Applications
Chemical film finds its way into various industries and applications:
- Aerospace: You’ll find chemical film used on aluminum aircraft components, particularly where electrical conductivity needs to be maintained.
- Automotive: It’s commonly used on fasteners, brackets, and other components in the automotive industry.
- Electronics: Chemical film protects electronic housings and chassis while maintaining electrical conductivity.
- Military Equipment: Many military specifications call for chemical film treatment on various components.
- Fasteners: Bolts, nuts, and other fasteners often receive chemical film treatment for corrosion protection.
- Hydraulic Systems: Components in hydraulic systems benefit from the thin, protective layer of chemical film.
- Machinery Parts: Various industrial machinery parts are treated with chemical film to enhance their durability.
- Telecommunications Equipment: Chemical film protects outdoor telecommunications equipment from environmental factors.
Pros
Chemical film offers several advantages that make it an attractive option:
- For many applications, chemical film is more economical than anodizing, especially for smaller parts or lower production volumes.
- The chemical process is relatively fast, allowing for higher throughput in production settings.
- While primarily used on aluminum, chemical film can be applied to a wider range of metals compared to anodizing.
- Unlike anodizing, chemical film doesn’t significantly impact the electrical conductivity of the base metal.
- If you’re planning to paint a metal surface, chemical film provides an ideal substrate for paint adhesion.
Cons
Despite its benefits, chemical film does have some limitations:
- The thin layer provided by chemical film is less durable than anodizing when it comes to wear and abrasion.
- Traditional chemical film processes use hexavalent chromium, which is facing increasing environmental regulations.
Anodizing vs Chemical Film: How to Choose?
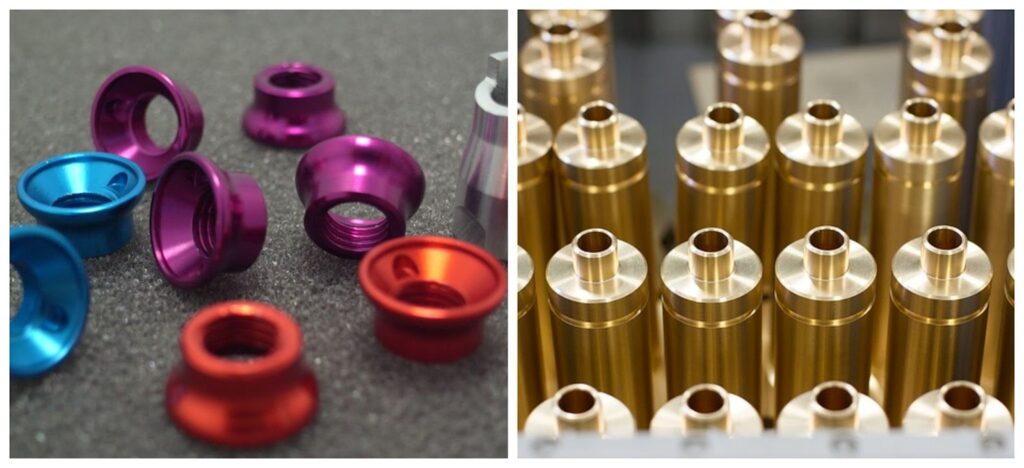
Selecting between anodizing and chemical film is a critical decision that can significantly impact the performance, longevity, and cost-effectiveness of your metal components. To make the right decision you have to consider the following factors and choose the one that best fits your needs.
Base Material
The type of metal you’re working with is the primary determining factor in your surface treatment choice. Different metals react differently to various treatments, and some processes are only suitable for specific materials.
Comparison
- Anodizing: Primarily suitable for aluminum and its alloys. It can also be used on titanium and magnesium, but the process and results differ.
- Chemical Film: More versatile, applicable to a wider range of metals including aluminum, magnesium, zinc, cadmium, copper, and silver.
If you’re working exclusively with aluminum, both options are viable. For other metals, chemical film is likely your only choice between these two processes.
Durability and Wear Resistance
The longevity of your component often depends on its ability to withstand wear and tear. In applications where parts are subject to frequent contact or abrasion, durability is crucial.
Comparison
- Anodizing: Provides excellent wear resistance. The hard oxide layer created by anodizing is integral to the metal surface and can significantly extend the life of the component.
- Chemical Film: Offers moderate wear resistance. The thin conversion coating provides some protection, but it’s not as durable as anodizing, especially in high-wear applications.
For components that will undergo frequent handling, movement, or abrasion, anodizing is generally the superior choice.
Corrosion Resistance
Corrosion can significantly reduce the lifespan of metal components and compromise their functionality. In harsh environments or outdoor applications, corrosion resistance is often a top priority.
Comparison
- Anodizing: Provides excellent long-term corrosion resistance. The thick oxide layer acts as a robust barrier against corrosive elements.
- Chemical Film: Offers good corrosion resistance, especially in the short to medium term. It can provide self-healing properties for minor scratches but generally doesn’t match the long-term protection of anodizing.
For long-term exposure to corrosive environments, anodizing is typically the better choice. For short-term protection or milder conditions, chemical film may be sufficient.
Aesthetic Considerations
In many applications, especially consumer products or architectural elements, the appearance of the finished product is crucial. The ability to achieve specific colors or finishes can be a deciding factor.
Comparison:
- Anodizing: Offers a wide range of color options through dye processes. It can also provide various finishes from matte to high gloss.
- Chemical Film: Limited color options, typically resulting in gold, clear, or green finishes. The color often indicates the level of protection rather than serving an aesthetic purpose.
If appearance is a primary concern and you need specific colors or finishes, anodizing is the clear winner.
Electrical Properties
In electrical or electronic applications, the surface treatment’s impact on conductivity can be critical. Some components require insulation, while others need to maintain conductivity.
Comparison:
- Anodizing: Creates an electrically insulating layer on the metal surface. This can be advantageous in some electronic applications but may be a drawback in others.
- Chemical Film: Maintains the electrical conductivity of the base metal. The thin conversion coating doesn’t significantly impede electrical flow.
If you need to maintain electrical conductivity, chemical film is the better choice. For applications requiring electrical insulation, opt for anodizing.
Cost and Production Volume
Budget constraints and production scale can significantly influence your choice of surface treatment. The cost-effectiveness of each process can vary depending on the size and quantity of parts being treated.
Comparison:
- Anodizing: Generally more expensive for small volumes or individual parts. However, it becomes more cost-effective for larger production runs.
- Chemical Film: More economical for small volumes or one-off treatments. The simpler process and equipment requirements often result in lower costs for smaller batches.
For small production runs or prototype parts, chemical film might be more cost-effective. For large-scale production, especially of aluminum parts, anodizing can offer better value in the long run.
Processing Time
In industries with tight production schedules, the time required for surface treatment can be a critical factor. Faster processing can lead to quicker turnaround times and increased productivity.
Comparison:
- Anodizing: Generally requires more time due to the multiple steps involved, including pre-treatment, anodizing, dyeing (if applicable), and sealing.
- Chemical Film: Typically a faster process, often completed in a single step. This can lead to quicker turnaround times.
If rapid processing is crucial, chemical film has the advantage. However, if the superior properties of anodizing are required, the longer processing time may be justified.
Environmental Considerations
Environmental regulations are becoming increasingly stringent, and the environmental impact of manufacturing processes is a growing concern for many companies.
Comparison:
- Anodizing: Generally considered more environmentally friendly. While it does use chemicals, they are typically less harmful than those used in traditional chemical film processes.
- Chemical Film: Traditional processes often use hexavalent chromium, which is facing increasing environmental scrutiny and regulation. However, more environmentally friendly alternatives are being developed.
If environmental impact is a primary concern, anodizing may be the better choice. However, it’s worth investigating newer, more eco-friendly chemical film processes if this treatment is preferred for other reasons.
Table Contrast
Want a quicker way to solve the dilemma? Then, here’s a comparison table to show you the technical differences between the two.
Feature | Anodising | Chemical Film |
Process Type | Electrochemical | Chemical |
Typical Thickness | 0.0002 to 0.001 inches | A few micrometres |
Wear Resistance | High | Moderate |
Corrosion Resistance | Excellent | Good |
Colour Options | Wide range | Limited (typically gold, clear, or green) |
Electrical Properties | Insulating | Conductive |
Cost for Small Volumes | Higher | Lower |
Processing Time | Longer | Shorter |
Environmental Impact | Lower | Higher (due to chromium use) |
Suitable Metals | Primarily aluminum | Wider range, including aluminum |
Paint Adhesion | Good | Excellent |
Durability | Long-term | Short to medium-term |
Self-Healing | No | Yes (limited) |
Temperature Resistance | High | Moderate |
Conclusion
Summing it up, now that you know the difference between anodizing and chemical film, you can easily decide on one. Each technique has unique characteristics that make it ideal for certain scenarios.
For instance, anodizing is ideal for applications where long-term performance and appearance are crucial. On the other hand, chemical film is suitable for a wider range of metals and applications where conductivity must be maintained.
Great, Together