Buying a CNC machine is a pretty hefty investment, which is why you have to be very careful that you are buying the right one. The most common dilemma a lot of people face with these machines is between a CNC router vs a CNC mill vs a CNC lathe.
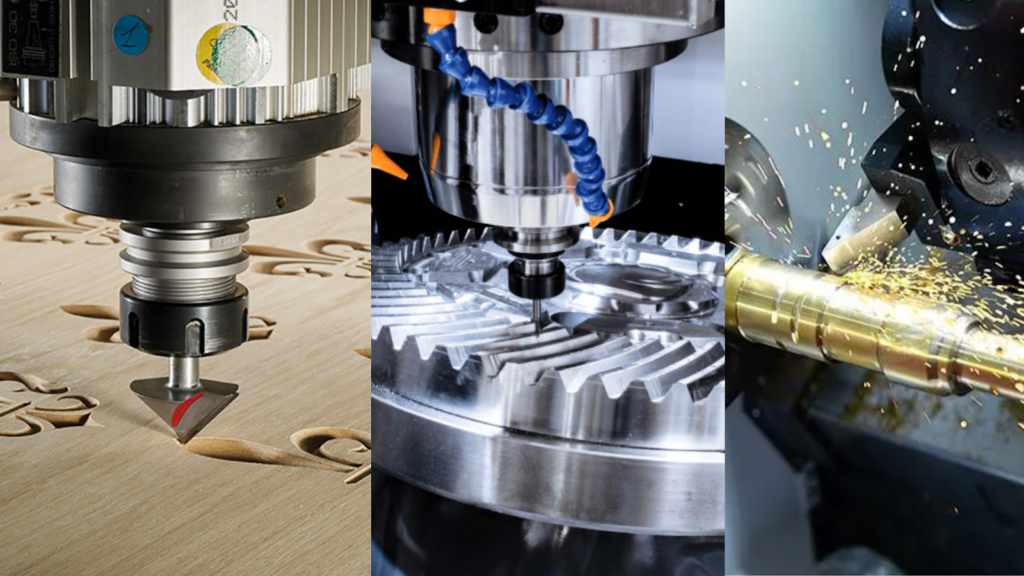
In this detailed guide below, we will explor the three different types of CNC machines and find out which one is suitable for what purpose. After going through all of them, you will know exactly which machine will be the perfect choice for your particular CNC machining projects. Let’s get started.
What is a CNC Router?
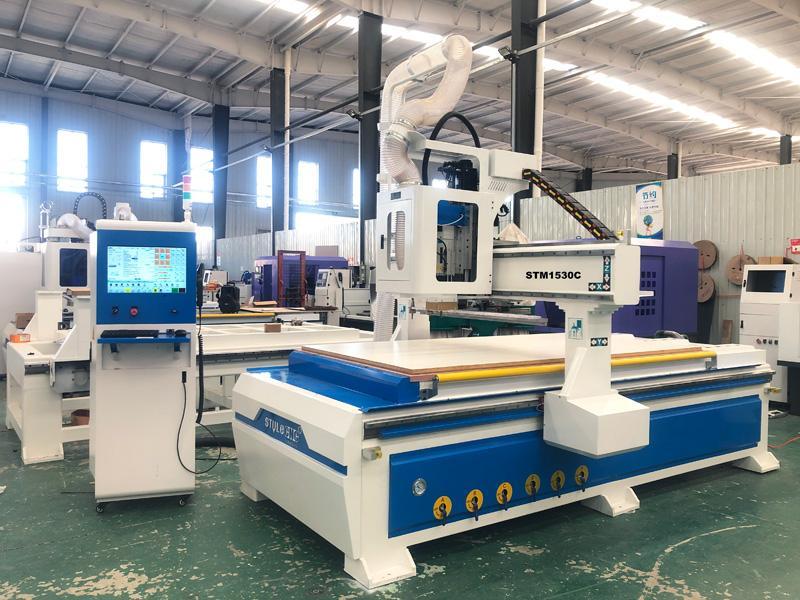
A CNC router is an automated cutting machine used in manufacturing and prototyping processes. It utilizes computer-controlled cutting tools to carve, drill, and shape various materials, including wood, plastics, metals, and composites.
CNC routers operate on a similar principle to CNC milling machines but are typically designed for larger, flatter workpieces and softer materials.
How Does It Work?
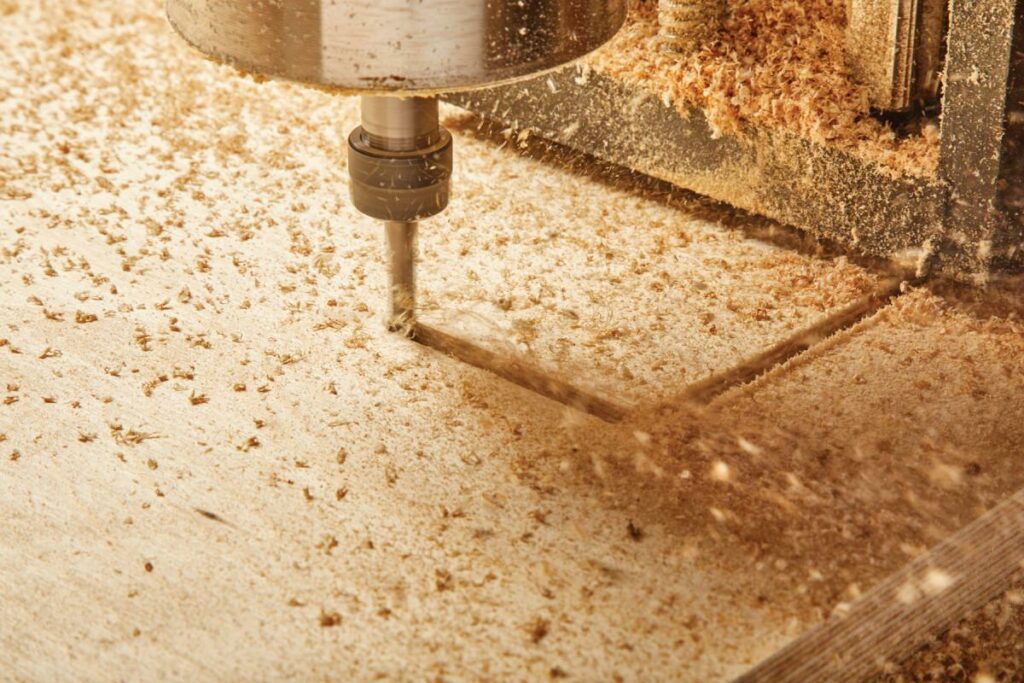
CNC routers function by translating digital designs into precise cutting instructions. The process begins with creating a design using Computer-Aided Design (CAD) software. This design is then converted into a series of commands, known as G-code, which direct the router’s movements.
The router consists of a cutting tool mounted on a gantry system that moves along X, Y, and Z axes. As the machine reads the G-code instructions, it guides the cutting tool across the workpiece, removing material to create the desired shape or pattern.
Ideal Applications
CNC routers are versatile tools suited for a wide range of applications, including:
- Woodworking: Furniture making, cabinetry, and decorative panels
- Sign making: Creating custom signage for businesses and events
- Aerospace: Fabricating lightweight components and moulds
- Automotive: Producing interior trim pieces and prototypes
- Electronics: Manufacturing circuit boards and enclosures
- Art and sculpture: Crafting intricate designs and 3D artworks
Features
- Multi-axis Capability
Advanced CNC routers can operate on multiple axes, typically three (X, Y, Z) or five axes. This allows for complex 3D cutting and contouring, enabling the creation of intricate shapes and patterns. Multi-axis functionality expands the range of possible designs and improves overall versatility.
- Automatic Tool Changing
Many CNC routers feature automatic tool-changing systems, allowing the machine to switch between different CNC cutting tools without manual intervention. This feature enhances efficiency by reducing downtime between operations and enables the completion of complex projects requiring multiple tool types in a single setup.
- Vacuum Table and Clamping Systems
CNC routers often incorporate vacuum tables or clamping systems to securely hold workpieces in place during cutting operations. Vacuum tables use suction to grip flat materials while clamping systems can accommodate irregularly shaped pieces. These features ensure precise cutting by preventing workpiece movement and vibration.
- Dust Collection and Extraction
To maintain a clean working environment and protect both the machine and operators, CNC routers typically include integrated dust collection and extraction systems. These systems capture and remove debris and dust generated during cutting, improving air quality, visibility, and overall safety in the workspace.
- Software Integration and Simulation
Modern CNC routers integrate seamlessly with CAD/CAM software, allowing for efficient design-to-production workflows. Advanced software packages offer simulation capabilities, enabling operators to visualize and optimize cutting paths before actual machining begins. This feature helps identify potential issues, reduce material waste, and improve overall efficiency.
Pros
- CNC routers can operate continuously with minimal human intervention, significantly increasing output compared to manual methods.
- The computer-controlled nature of CNC routers ensures high precision and consistency across multiple production runs.
- Automation reduces the need for skilled manual labour, potentially lowering overall production costs.
- CNC routers can easily accommodate design changes and produce complex shapes that would be difficult or impossible to create manually.
- Advanced nesting software allows for efficient use of materials, minimizing waste and reducing costs.
Cons
- CNC routers can be expensive to purchase and set up, requiring a significant upfront investment that may be challenging for smaller businesses.
- Operating CNC routers and associated software requires specialized training, which can be time-consuming and may necessitate additional staff education or the hiring of skilled operators.
What is a CNC Mill?
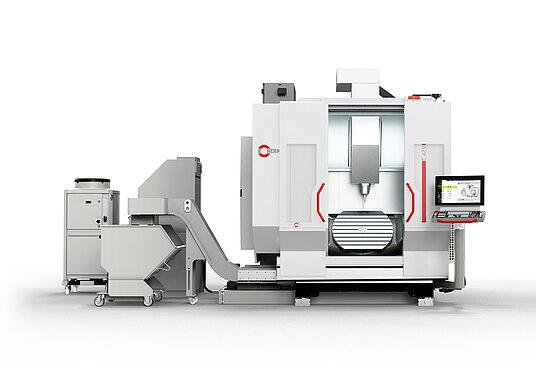
A CNC mill is a sophisticated machining tool used in manufacturing to cut and shape solid materials with high precision. It uses computer-controlled cutting tools to remove material from a workpiece, creating complex three-dimensional parts.
CNC mills are versatile machines capable of performing various operations such as drilling, boring, facing, and contouring on materials like metals, plastics, and composites.
How Does It Work?
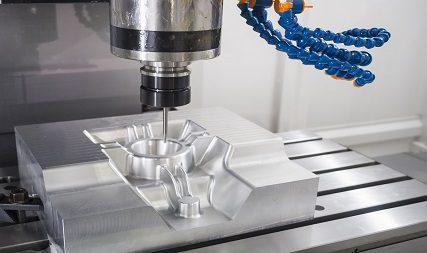
CNC mills operate by translating digital design data into precise mechanical movements. The process begins with creating a 3D model using Computer-Aided Design (CAD) software. This model is then converted into a set of instructions, known as G-code, which directs the mill’s movements.
The mill consists of a spindle that holds and rotates cutting tools and a table that secures the workpiece. The machine moves either the spindle or the table (depending on the configuration) along multiple axes. As the mill reads the G-code instructions, it guides the cutting tool to remove material from the workpiece, creating the desired shape with high accuracy.
Ideal Applications
CNC mills are ideal for a wide range of applications, including:
- Aerospace: Manufacturing precision components for aircraft and spacecraft
- Automotive: Producing engine parts, transmission components, and prototypes
- Medical: Creating implants, surgical instruments, and medical devices
- Mould making: Fabricating complex moulds for injection moulding and die-casting
- Electronics: Manufacturing heat sinks, chassis, and precision components
- Tool and die: Producing custom tools, fixtures, and dies for various industries
Features
- Multi-axis Capability
CNC mills can operate on multiple axes, typically three (X, Y, Z) or five axes. This allows for complex 3D machining, enabling the creation of intricate geometries and undercuts. Multi-axis functionality expands the range of possible parts and improves overall versatility, allowing for the machining of complex components in a single setup.
- High-Speed Spindles
Modern CNC mills feature high-speed spindles that can rotate at tens of thousands of RPM. These high-speed spindles allow for faster material removal rates, improved surface finish, and the ability to work with a wide range of materials. They also enable the use of smaller cutting tools for intricate details.
- Automatic Tool Changing
Many CNC mills incorporate automatic tool changing systems, allowing the machine to switch between different cutting tools without manual intervention. This feature enhances efficiency by reducing downtime between operations and enables the completion of complex parts requiring multiple tool types in a single setup.
- Coolant Systems
CNC mills typically include advanced CNC coolant systems that deliver cutting fluid or coolant to the cutting zone. These systems help manage heat generation, improve tool life, enhance surface finish, and aid in chip evacuation. Some mills feature through-spindle coolant delivery for improved performance in deep-hole drilling and other challenging operations.
- Probing and Measurement Systems
Advanced CNC mills often incorporate probing systems for in-process measurement and inspection. These systems can automatically measure workpiece dimensions, detect tool wear, and make real-time adjustments to ensure part accuracy. This feature reduces setup time, improves quality control, and enables adaptive machining strategies.
Pros
- CNC mills can achieve extremely tight tolerances, often in the range of microns, ensuring high-quality and consistent parts.
- The multi-axis capabilities allow for the creation of complex 3D shapes and features that would be difficult or impossible to produce manually.
- Computer control ensures that parts can be reproduced with high consistency, making CNC mills ideal for both prototyping and production runs.
- CNC mills can perform a wide range of operations (milling, drilling, boring, tapping) on various materials, often in a single setup.
- Automation minimizes the risk of errors associated with manual machining, leading to higher quality and less waste.
Cons
- CNC mills represent a significant investment, with advanced machines costing hundreds of thousands of dollars, which can be prohibitive for smaller businesses.
- Programming and operating CNC mills require specialized skills and knowledge, necessitating significant training or the hiring of skilled machinists.
What is a CNC Lathe?
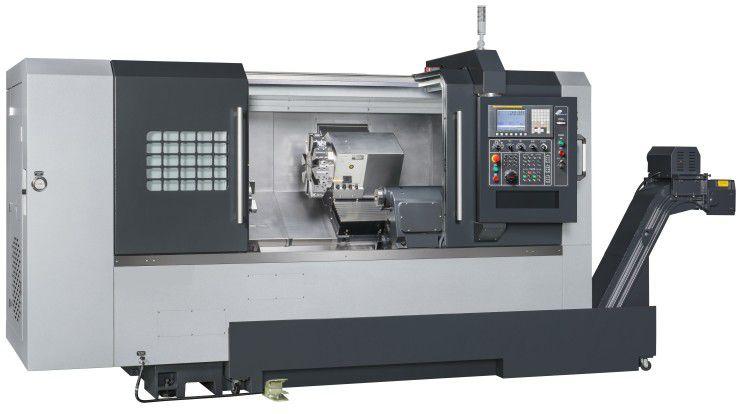
A CNC (Computer Numerical Control) lathe is an automated machine tool used in manufacturing to create cylindrical parts with high precision. It uses computer-controlled cutting tools to remove material from a rotating workpiece, typically producing parts with circular cross-sections.
CNC lathes are essential in modern manufacturing for their ability to create complex, symmetrical parts quickly and accurately.
How Does It Work?
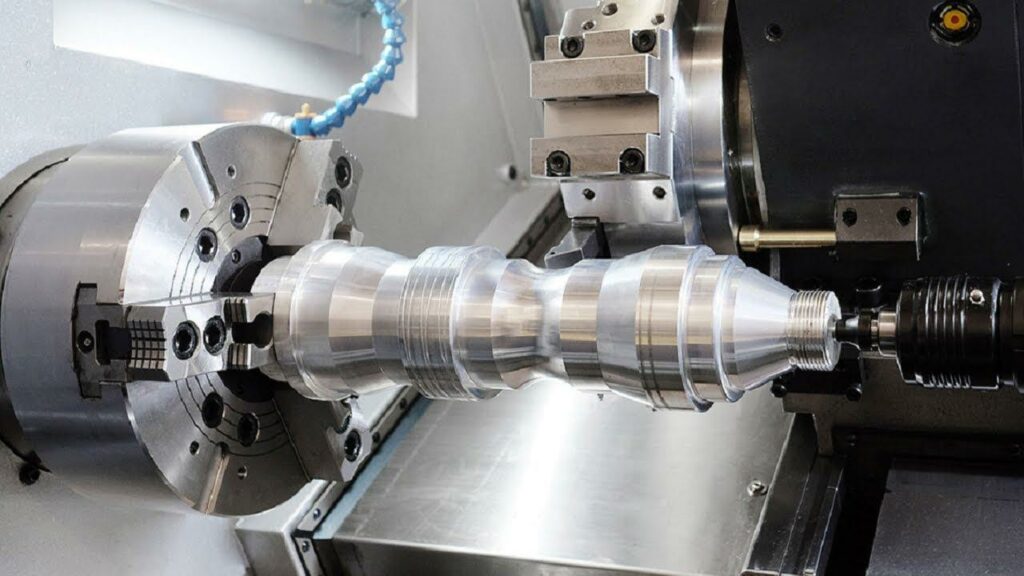
CNC lathes operate by translating digital design data into precise mechanical movements. The process begins with creating a part design using Computer-Aided Design (CAD) software. This design is then converted into a series of instructions, known as G-code, which directs the lathe’s movements.
In a CNC lathe, the workpiece is held in a chuck that rotates at high speed. Cutting tools mounted on a turret move along the X and Z axes (and sometimes Y axis in more advanced machines) to remove material from the rotating workpiece. As the lathe reads the G-code instructions, it guides the cutting tools to shape the workpiece, creating the desired part with high accuracy.
Ideal Applications
CNC lathes are ideal for a wide range of applications, including:
- Automotive: Producing shafts, pistons, and other cylindrical engine components
- Aerospace: Manufacturing turbine parts, fasteners, and precision fittings
- Oil and Gas: Creating drilling components, valves, and pipe fittings
- Medical: Fabricating implants, surgical instruments, and medical device components
- General Manufacturing: Producing bolts, screws, bearings, and other turned parts
- Electronics: Creating housings, connectors, and precision components
Features
- Live Tooling
Modern CNC lathes often feature live tooling capabilities, where rotating cutting tools can perform milling, drilling, and other operations on the workpiece while it’s mounted in the lathe. This feature allows for the creation of complex parts with both turned and milled features in a single setup, increasing efficiency and accuracy.
- Multi-axis Turning
Advanced CNC lathes Integrated CNC milling machine functionality, can operate on multiple axes, typically including X, Z, and C axes, with some machines also incorporating Y-axis movement. This multi-axis capability allows for the creation of complex contours, off-centre features, and even some milling operations, greatly expanding the range of parts that can be produced on a lathe.
- Automatic Tool Changing
Many CNC lathes incorporate automatic tool-changing systems, allowing the machine to switch between different cutting tools without manual intervention. This feature enhances efficiency by reducing downtime between operations and enables the completion of complex parts requiring multiple tool types in a single setup.
- Sub-spindle Systems
Some CNC lathes feature sub-spindle systems that allow for simultaneous machining on both ends of a workpiece or for parts to be automatically transferred for back-end operations. This capability increases productivity by reducing handling time and enabling complete part production in a single machine.
- Integrated Measurement and Inspection
Advanced CNC lathes often include integrated probing and measurement systems for in-process inspection. These systems can automatically measure part dimensions, detect tool wear, and make real-time adjustments to ensure part accuracy. This feature improves quality control and reduces scrap rates.
Pros
- CNC lathes can produce parts much faster than manual lathes, making them ideal for high-volume production.
- Computer control ensures that parts can be reproduced with high consistency, even across long production runs.
- Advanced CNC lathes can create complex profiles and features that would be difficult or impossible to achieve manually.
- Automation reduces the need for constant operator intervention, potentially lowering overall production costs.
- Modern CNC lathes can often perform turning, milling, and drilling operations in a single setup, reducing the need for multiple machines.
Cons
- CNC lathes represent a significant upfront cost, which can be challenging for smaller businesses or workshops to justify.
- Creating efficient and accurate CNC programs requires specialized skills and knowledge, necessitating trained programmers or extensive operator training.
Conclusion
To conclude the decision of CNC router vs CNC mill vs CNC lathe mostly depends on the projects you are working on. For instance, if you are working with wood, plastics, and composites, and need carving and sign-making purposes, then a CNC router is the perfect choice.
On the other hand, you have a CNC mill and a CNC lathe, here the choice of material is pretty similar. But the easiest way to decide is considering the part complexity. If you are making a cylindrical part, your best bet is a CNC lathe, and if you are making a complex geometrical shape, then go with a CNC mill.
Great, Together