Sheet metal stamping defects can significantly impact your production quality and bottom line. While these defects are common in manufacturing operations, understanding their root causes and implementing preventive measures can help you maintain consistent quality and reduce waste.
In this guide, we will try to explore them and tell you how to prevent common defects in sheet metal stamping. So, if you are starting with sheet metal stamping, then this guide can be perfect for you to ensure part quality.
Preventing Defects in Sheet Metal Stamping
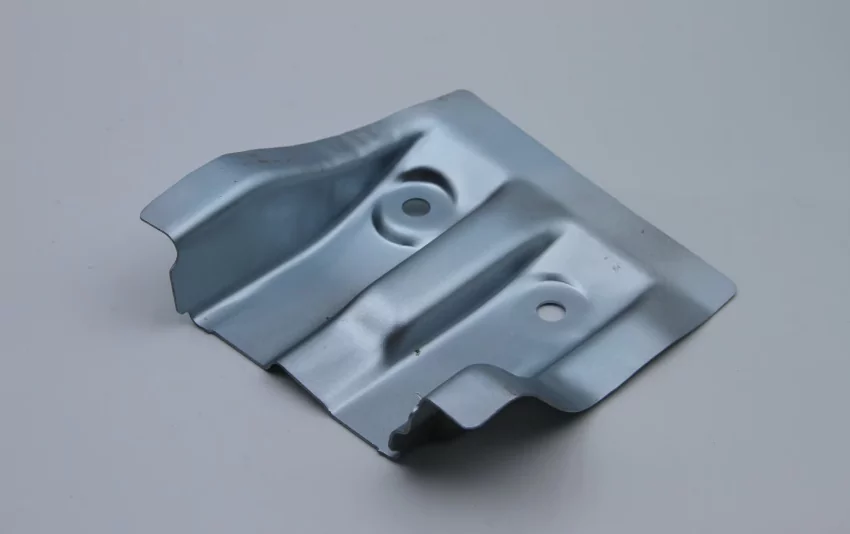
While corrective measures are necessary, a proactive approach to quality control is paramount. By focusing on prevention, you can minimize material waste, reduce production delays, and ultimately enhance their bottom line. Here are some key factors to prevent defects in sheet metal stamping.
Material Selection and Handling
First, you have to implement strict incoming inspection procedures to verify material properties against specifications. Utilize advanced techniques like ultrasonic testing and eddy current testing to detect hidden flaws.
Store materials in a controlled environment to prevent corrosion, contamination, and deformation. Ensure proper stacking and handling to avoid scratches, dents, and edge damage.
Anneal or normalize materials to achieve desired mechanical properties and improve formability.
Tooling Design and Maintenance
Employ computer-aided engineering (CAE) software for precise tool design and simulation to predict potential problems like wrinkling, tearing, and springback. Consider material flow, blank shape, and die clearance to minimize deformation and stress concentrations.
Implement a preventive maintenance program for all stamping tools, including regular inspections, sharpening, and repairs. Utilize proper lubrication and cooling to reduce wear and tear. Conduct thorough tryouts before full-scale production to identify and address any tooling issues.
Process Control
Accurately set press parameters such as tonnage, speed, and stroke length to optimize forming conditions. Utilize automated systems for consistent and repeatable press settings.
Implement real-time process monitoring systems to track key process parameters and identify deviations from target values. Conduct regular data analysis to identify trends and potential issues. Provide comprehensive training to operators on safe operating procedures, quality control techniques, and troubleshooting.
Quality Assurance
Conduct regular in-process inspections at critical stages of the stamping process to identify and correct defects early on. Utilize appropriate inspection methods such as dimensional checks, visual inspections, and gauge measurements.
Implement SPC techniques to monitor process variability and identify trends that could lead to defects. Utilize control charts to track key process parameters and identify out-of-control conditions. Conduct a thorough root cause analysis of all defects to identify the underlying causes.
Lean Manufacturing Principles
Minimize waste in all areas of the stamping process, including material waste, scrap, and rework. Use lean manufacturing principles such as 5S, visual management, and continuous improvement.
Optimize material flow and process sequences to minimize handling time and reduce the risk of damage. Eliminate unnecessary steps and bottlenecks in the production process.
Identifying the Most Common Stamping Defects
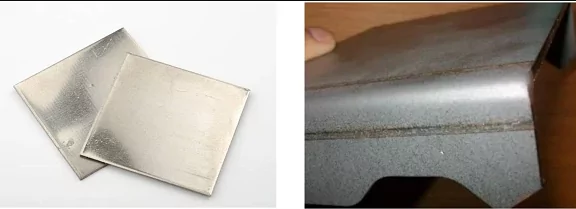
Understanding the various defects that can occur during the stamping process is your first line of defense. Here are the most common sheet metal stamping defects.
Wrinkling
Wrinkling occurs when excess material flows into the die cavity during the stamping process. You’ll notice this defect as unwanted folds or creases in the finished part. Several factors can contribute to wrinkling:
- Insufficient blank holder force
- Improper die clearance
- Incorrect material thickness
- Uneven material flow during forming
To prevent wrinkling, ensure proper blank holder pressure and optimize your die design. You might need to adjust the blank holder force based on material thickness and properties.
Tearing
When your material stretches beyond its forming limit, tearing becomes a significant concern. This defect typically appears as splits or cracks in the formed part. Common causes include:
- Excessive punch force
- Sharp radius in die or punch corners
- Insufficient material thickness
- Poor material quality or incorrect grade selection
Prevent tearing by carefully controlling punch force and ensuring appropriate tool geometry. Consider using simulation software to validate your forming process before production.
Springback
Springback occurs when the metal partially returns to its original shape after forming. This dimensional accuracy issue can cause significant problems in assembly operations. Key factors affecting springback include:
- Material properties (especially yield strength)
- Bend radius
- Forming angle
- Material thickness
- Tool temperature
To minimize springback, you’ll need to consider overbending or using appropriate compensation techniques in your tool design.
Surface Defects
Surface defects can manifest as scratches, dents, or die marks on your finished parts. These issues often result from:
- Worn or damaged tooling
- Improper material handling
- Insufficient lubrication
- Contaminated material surfaces
Regular tool maintenance and proper material handling procedures are essential for preventing surface defects.
Adjusting Press Settings for Consistent Results
Proper press settings are paramount in achieving consistent quality and preventing defects in sheet metal stamping operations. These settings directly influence material flow, deformation, and the final part dimensions and properties.
Press Force Control
Precisely calculate the required tonnage based on material properties, part geometry, and desired deformation. Utilize finite element analysis (FEA) software to simulate forming processes and predict the necessary force.
Implement real-time force monitoring systems, such as load cells, to continuously track the force applied during the stamping process. This data provides valuable insights into material behavior and potential issues.
When adjusting press force, proceed gradually to minimize the risk of unexpected results, such as part breakage or excessive deformation. Monitor part quality closely during adjustments and make fine-tuning adjustments as needed.
Stroke Length and Speed Control
Set the stroke length precisely to ensure sufficient material deformation without causing excessive thinning or tearing. Consider factors such as die clearance, part geometry, and material thickness.
Control the press speed to avoid material strain rate issues. High strain rates can lead to increased stress and potential for cracking, while excessively slow speeds can increase the risk of springback.
Adjust stroke length and speed based on the specific material being stamped. Different materials exhibit varying degrees of strain rate sensitivity. For complex parts with varying deformation requirements, consider implementing variable speed control. This allows for optimized forming conditions throughout the stroke.
Die Height Adjustment
Maintain consistent shut height across your tooling to ensure uniform deformation and prevent part distortion. Inconsistent shut height can lead to variations in part thickness and dimensional accuracy.
Utilize precision die height adjustment systems, such as hydraulic or pneumatic cylinders, for accurate and repeatable settings. Implement regular checks of die height settings to ensure they remain within specified tolerances. Document optimal die height settings for each tool to facilitate setup and troubleshooting.
Blank Holder Pressure Control:
Calculate the appropriate blank holder pressure based on material properties, part geometry, and desired deformation. Consider factors such as material thickness, tensile strength, and the risk of wrinkling or tearing.
Integrate pressure monitoring systems to track blank holder pressure during the stamping process. Utilize pressure transducers to measure and control pressure in real-time. For complex geometries, adjust pressure zones within the blank holder to control material flow and prevent localized deformation.
Maintain consistent blank holder pressure throughout the stroke to ensure uniform material deformation and prevent defects such as wrinkles, buckles, and tears.
Using the Right Material to Avoid Cracking
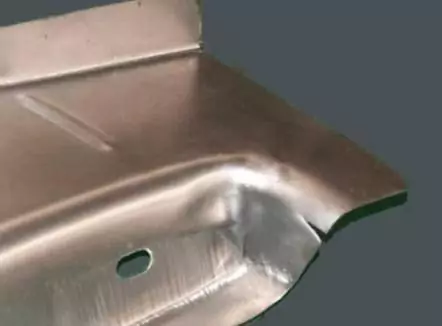
Material selection and handling play crucial roles in preventing stamping defects. Understanding material properties and requirements will help you achieve better results.
Material Grade Selection
Choosing the right material grade is a critical first step. Consider these factors:
- Part Design Requirements
Determine the specific mechanical properties required for the part, such as tensile strength, yield strength, ductility, and hardness. Consider the part’s intended use and the loads it will be subjected to.
- Forming Complexity
Select a material with sufficient formability to withstand the complex deformations required for the part. Consider the number of bends, draws, and other forming operations involved.
- Required Mechanical Properties
Ensure the material meets the desired strength, stiffness, and other mechanical properties after forming. Consider factors such as fatigue resistance, corrosion resistance, and temperature resistance.
- Cost Considerations
Evaluate the cost of different material options, taking into account factors such as material price, availability, and potential for scrap.
- Surface Finish Requirements
Select a material that can achieve the desired surface finish after forming. Consider factors such as the need for painting, plating, or other surface treatments.
Material Thickness Considerations
Proper material thickness is essential for successful stamping and preventing cracking.
- Calculate Minimum Thickness Requirements
Determine the minimum material thickness required to withstand the forming forces and prevent excessive thinning or tearing. Consider factors such as part geometry, forming operations, and material properties.
- Balance Formability and Structural Requirements
Find a balance between material thickness for adequate formability and sufficient thickness to meet the part’s structural requirements.
- Account for Stretching During Forming
Consider the amount of material stretching that will occur during forming and adjust the initial thickness accordingly.
- Maintain Consistent Thickness Across Blanks
Ensure consistent material thickness across all blanks to prevent variations in part dimensions and performance.
Material Storage and Handling
Proper storage and handling practices are essential to maintain material quality and prevent defects.
- Store Materials in Controlled Environments
Protect materials from environmental factors such as moisture, temperature fluctuations, and contaminants. Store materials in a clean, dry, and well-ventilated environment.
- Implement Proper Material Rotation Procedures
Use a first-in, first-out (FIFO) system to ensure that older materials are used first. This helps prevent material degradation and provides consistent material properties.
- Use Appropriate Handling Equipment
Use appropriate handling equipment, such as forklifts and hoists, to prevent damage to the material during transport and storage. Avoid dropping, dragging, or mishandling materials.
- Maintain Cleanliness and Organization
Keep the storage area clean and organized to prevent contamination and damage to materials.
Material Testing and Verification
Regular material testing is crucial to ensure consistent material quality and prevent defects.
- Implement Incoming Material Inspection Procedures
Inspect incoming materials to verify that they meet the specified requirements. Conduct visual inspections, dimensional checks, and other relevant tests.
- Conduct Regular Material Testing
Conduct regular tests on materials, such as tensile tests, hardness tests, and chemical analysis, to verify their properties. This helps identify any variations in material properties and take corrective actions.
- Document Material Properties
Maintain accurate records of material properties, including test results and certifications. This documentation provides a valuable reference for future production runs.
Maintenance Tips for Reducing Errors in Stamping
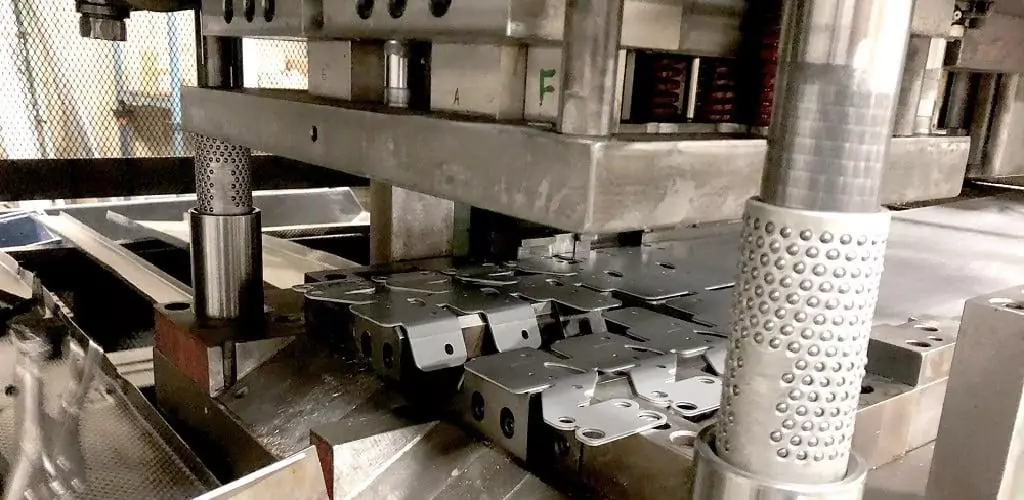
A well-maintained stamping operation is essential for preventing defects. Implement these maintenance practices to ensure consistent quality.
Tool Maintenance
A great way to reduce errors in your stamping process is through regular tool maintenance. With tool maintenance alone, you can prevent many common defects. Such as –
- Implement scheduled inspection programs
- Monitor tool wear
- Maintain proper tool alignment
- Document maintenance procedures and schedules
Press Maintenance
Aside from the tools, you have to also take care of the press. Keep your presses in optimal condition, and you won’t have to bother too much about defects.
- Follow the manufacturer’s maintenance recommendations
- Monitor press alignment and gibs
- Check hydraulic and pneumatic systems regularly
- Maintain proper lubrication
Die Maintenance
Along with the tool and press, you should pay attention to the die as well. Proper die maintenance ensures better part quality and prevents defects. Here’s how you maintain dies –
- Clean and inspect dies regularly
- Monitor die wear points
- Maintain proper die clearances
- Document die maintenance history
Preventive Maintenance Planning
Lastly, you must incorporate all these processes into proper maintenance planning. This will help you stay more consistent with the process.
- Create detailed maintenance schedules
- Train maintenance personnel properly
- Document all maintenance activities
- Monitor maintenance effectiveness
Conclusion
To sum up, preventing defects in sheet metal stamping requires a comprehensive approach. It’s a combination of proper material selection, precise press settings, and regular maintenance. With our guide, you get the details of each approach. Now, you just have to follow them and use them in your process. If you want an easier solution, then go for a professional manufacturing company. Stop asking yourself, “Where is the best sheet metal fabrication near me?”. Simply head over to Zintilon and get the best sheet metal stamping services free of any common defects.
Great, Together