Tack welds over the years have proven quite effective in improving the weld quality for final outputs. When you start getting into tack welds, you will come across the dilemma of choosing the right type of tack weld for your particular use.
To make the right choice, you need to know what are the types of tack welds and their applications. Without having any idea about them, you can’t decide which suits your project the best.
So, let’s go ahead and explore the types of tack welds and their application in various scenarios.
Types of Tack Welds and Their Uses
There are different types of tack welds out there. Each one serves a unique purpose and is used in different aspects. Let’s explore the different types before we dive into the details.
Standard Tack Weld
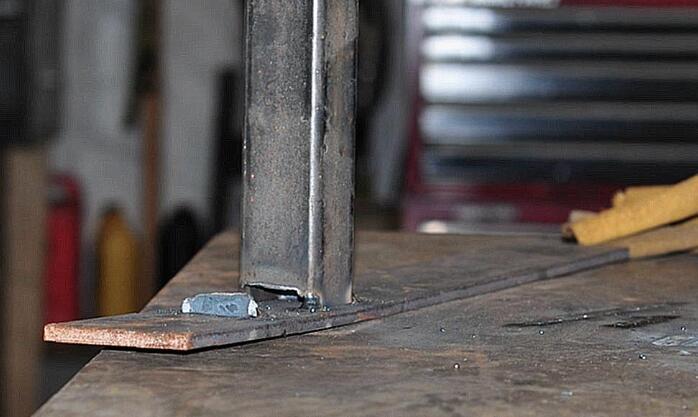
The most common type, standard tack welds, are applied in short, controlled arcs, creating small, evenly spaced deposits. They serve as the foundation for most welding assemblies, providing essential support and maintaining accurate alignment throughout the welding process.
Created using a standard welding process with the typical metal welder, such as MIG, TIG, or stick, with short, controlled arcs to deposit a small amount of weld material.
Uses
- General Support: Holding components in place during assembly and preventing movement.
- Weight Distribution: Preventing heavy components from breaking free during welding.
- Alignment: Ensuring accurate positioning of parts before the final weld.
Bridge Tack Weld
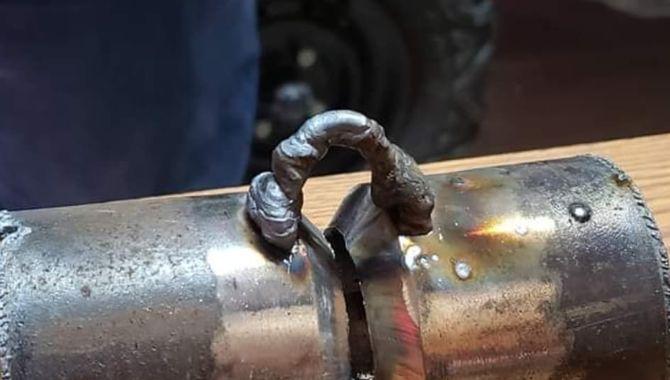
Designed to bridge minor gaps between components, bridge tacks are applied sequentially, alternating between sides to allow for cooling and minimize distortion. This technique ensures a gradual and controlled closure of the gap, preventing potential warping or misalignment.
Applied in a series of small, alternating tacks on each gap side. This allows the previously applied tack to cool before the next one is made, minimizing distortion.
Uses
- Gap Bridging: Overcoming minor misalignments or material imperfections.
- Distortion Control: Reducing the risk of warping or twisting during welding.
- Suitable for: Processes like Flux-Cored, MIG, and TIG welding due to their ease of arc initiation.
Thermit Tack Weld
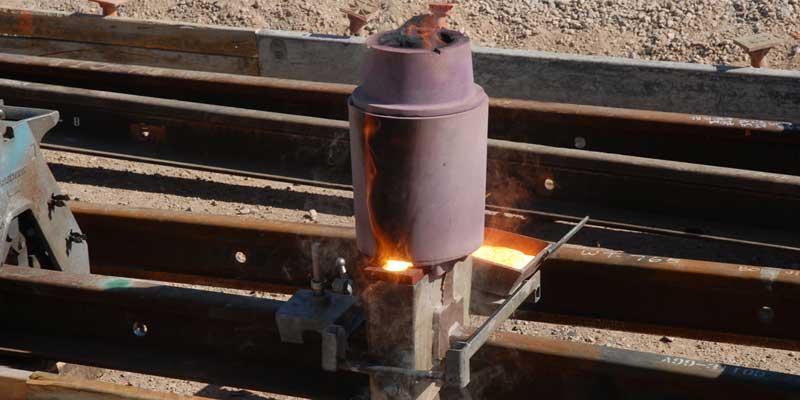
Utilizing an exothermic reaction of specialized metals, thermit tacks generate intense localized heat, rapidly melting the materials at the joint. This method is particularly valuable for joining dissimilar metals or in situations where conventional welding techniques prove challenging.
A mixture of magnesium, aluminum, and iron oxide powder is ignited, producing intense heat (over 4000°F). This localized heat melts the metals at the joint, creating a strong bond.
Uses
- Joining Dissimilar Metals: Effective for joining materials that are difficult to weld with conventional methods.
- Rapid Repairs: These can be used for quick field repairs in certain situations.
- Specialized Applications: Primarily used in industrial and construction settings requiring high heat.
Hot Tack Weld
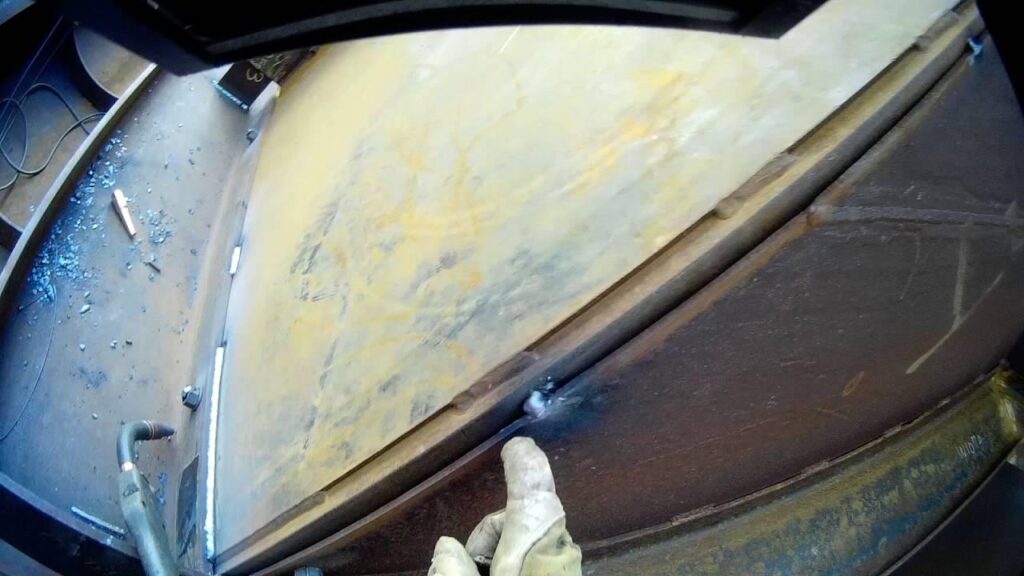
Involving the deposition of a larger bead of weld material followed by a forceful impact with a sledgehammer, hot tacks are employed to bridge larger gaps and achieve precise alignment. This method requires careful control and is typically reserved for situations where other techniques are not feasible.
A larger bead of weld material is laid down, creating a temporary connection. The welded area is then struck with a sledgehammer to force the components into contact.
Uses
- Overcoming Large Gaps: Suitable for bridging significant gaps between components.
- Forceful Alignment: The impact from the sledgehammer can help to align parts more precisely.
- Limited Applications: Primarily used in situations where other methods are not feasible.
Ultrasonic Tack Weld
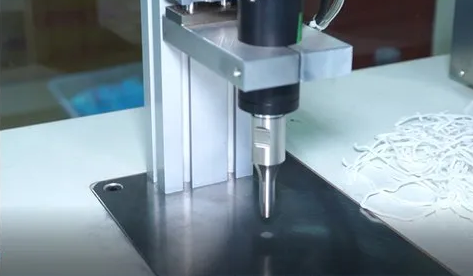
Leveraging high-frequency vibrations to generate heat through friction, ultrasonic tacks offer a precise and controlled method for joining materials. This technique is particularly well-suited for delicate materials or those sensitive to excessive heat, minimizing the risk of damage or distortion.
An ultrasonic welding tool applies rapid, high-frequency vibrations to the joint interface. This friction generates heat, melting the materials at the contact points.
Uses
- Joining Plastics and Other Non-Metals: Often used for joining plastics and other non-metallic materials.
- Joining Dissimilar Metals: This can be effective for joining materials that are difficult to weld with traditional methods.
- Precise Applications: Suitable for applications requiring precise control and minimal heat input.
Temporary Tack Welds for Assembly Alignment
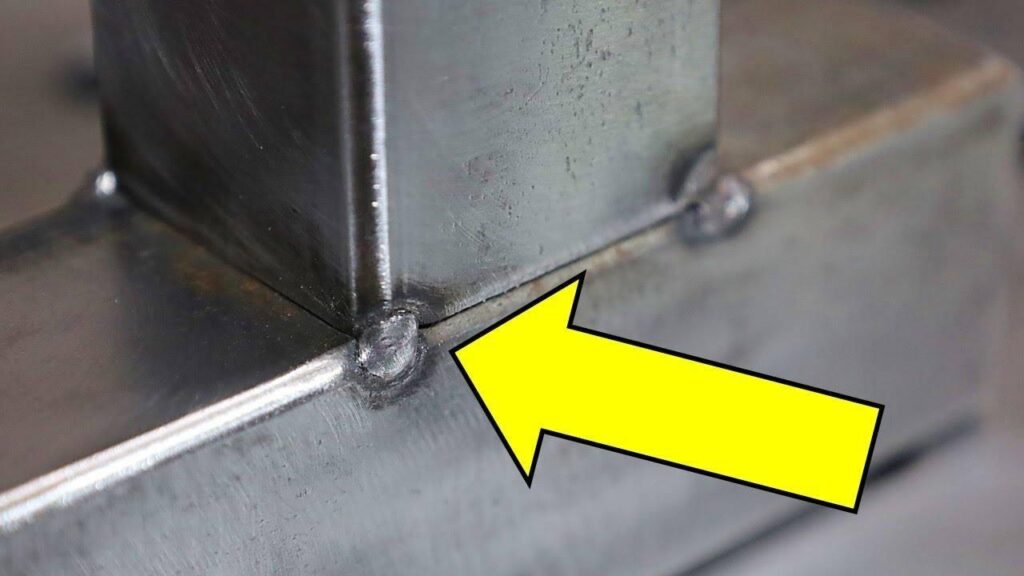
Temporary tack welds are small, localized welds strategically placed to hold components in precise alignment before the final welding operation. They act as temporary fixtures, preventing movement or shifting of the parts during handling, manipulation, or the final welding process.
- Securing Components: Tack welds create a temporary bond between the components, preventing them from moving out of position. This is crucial for maintaining the desired fit-up and ensuring accurate alignment for the final weld.
- Minimizing Distortion: By holding the components securely, tack welds can minimize the risk of distortion caused by handling, gravity, or the heat input from the welding process itself.
- Facilitating Handling: Tack welds make it easier to handle and manipulate large or complex assemblies without fear of the components shifting or separating.
Reasons to Choose Temporary Tack Welds
- Flexibility and Adjustability
Temporary tack welds allow for fine-tuning of component positions before the final weld. If misalignments are detected, tacks can be easily removed and reapplied to correct the issue, offering greater flexibility compared to rigid fixtures.
- Reduced Reliance on Complex Fixturing
Tack welding minimizes the need for expensive and time-consuming custom fixtures. This can significantly reduce upfront costs, especially for smaller production runs or projects with unique geometries.
- Improved Workability and Handling
Tack welds provide secure temporary connections, making it easier to handle, manipulate, and transport large or complex assemblies without the risk of components shifting or separating. This enhances safety and efficiency in the production process.
- Minimized Distortion Control
By holding components securely in place, tack welds can help to minimize distortion caused by the heat input from the welding process itself. This is crucial for ensuring dimensional accuracy and maintaining the integrity of the final assembly.
Permanent Tack Welds for Structural Support
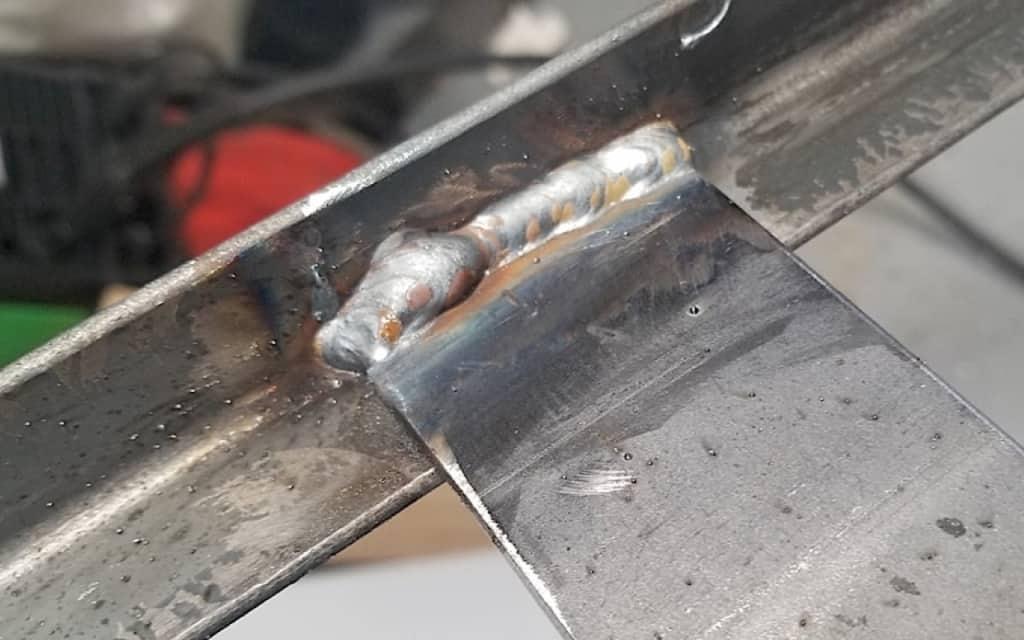
Permanent tack welds are designed to remain integral to the final welded joint. Unlike temporary tacks, which are often removed or consumed during the final welding process, permanent tacks are intentionally left in place to contribute to the assembly’s overall strength and structural integrity.
- Reinforcement of Critical Areas: Permanent tacks can be strategically placed in high-stress or vibration areas to provide additional support and reinforce the final weld. This is particularly important in applications where the structure is subjected to significant loads or dynamic forces.
- Improved Fatigue Resistance: By distributing stress more evenly, permanent tacks can help improve the welded joint’s fatigue resistance, reducing the likelihood of cracks or failures over time.
- Enhanced Load-Bearing Capacity: In some cases, permanent tacks can significantly increase the structure’s load-bearing capacity, making it more robust and reliable.
Reasons to Choose Permanent Tack Welds
- Increased Strength and Durability
Permanent tacks provide a significant boost to the overall strength and durability of the welded joint, making it better able to withstand demanding operating conditions.
- Improved Fatigue Resistance
By distributing stress more evenly, permanent tacks can help to minimize the risk of fatigue failures, ensuring a longer service life for the structure.
- Enhanced Load-Bearing Capacity
For applications requiring high load-bearing capacity, permanent tacks can be crucial in ensuring the structural integrity of the assembly.
- Reduced Risk of Failure
By providing additional support in critical areas, permanent tacks can help to reduce the risk of weld failures, improving the overall safety and reliability of the structure.
Spot Tack Welds for Thin and Lightweight Metals
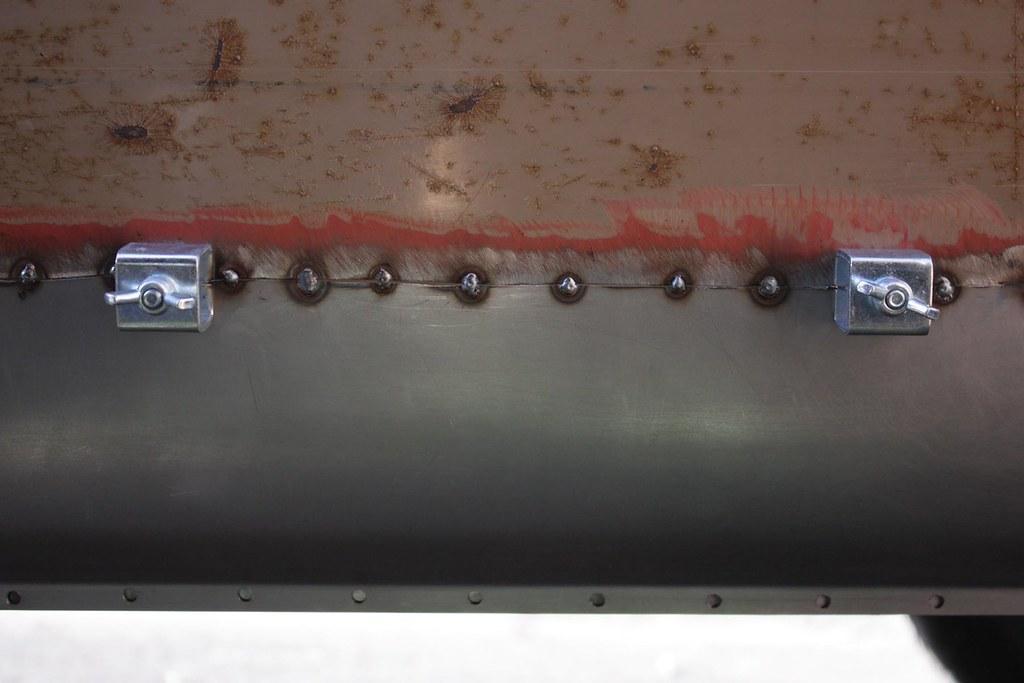
Spot tack welds are small, localized welds specifically designed for joining thin sheets of metal. These welds are characterized by their small size and limited penetration, minimizing the risk of warping, distortion, or weakening of the parent material.
- Minimal Heat Input: Spot tacks utilize a focused heat source, minimizing the overall heat input to the material. This reduces the risk of excessive heat distortion, which can be a significant concern when working with thin, lightweight metals.
- Localized Strength: While small, spot tacks provide localized strength, effectively holding the sheets together without significantly affecting the material’s overall properties.
- Versatility: Spot tacking can be used to join various thin metals, including steel, aluminum, and stainless steel, making it a versatile technique in sheet metal fabrication.
Reasons to Choose Spot Tack Welds
- Minimized Distortion
The localized heat input and small weld size minimize the risk of heat distortion, a critical consideration when working with thin, lightweight materials.
- Preservation of Material Properties
Spot tacks minimize the impact on the material’s strength and ductility, preserving the thin metal sheets’ desired properties.
- Versatility and Applicability
Suitable for a wide range of thin metal applications, including sheet metal fabrication, automotive manufacturing, and the production of lightweight structures.
- Efficiency
Spot tacking can be a fast and efficient method for joining thin sheets, increasing productivity in manufacturing processes.
Choosing the Right Tack Weld for Your Application
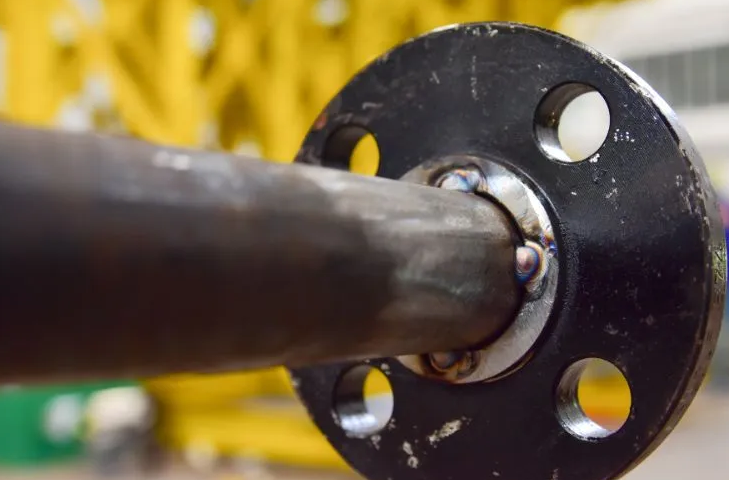
Selecting the appropriate tack weld type is crucial for ensuring a successful and efficient welding process.
Factors to consider
Several factors must be considered to make the best choice:
Metal Thickness
The selection of tack weld size is intimately linked to the thickness of the base metal. Thin materials necessitate smaller tacks to minimize heat input and mitigate the risk of distortion or even burn-through.
Conversely, thicker materials demand larger tacks to provide sufficient support and prevent movement during handling and subsequent welding operations.
Joint Type
The specific joint configuration exerts a significant influence on tack weld placement.
- Butt joints, for instance, often require a series of tacks along the joint line to ensure proper alignment and prevent gaps from forming.
- In contrast, lap joints may necessitate tacks at the overlapping edges to secure the components and prevent shifting.
Each joint type presents unique challenges that must be carefully considered when determining the optimal tack weld placement and size.
Welding Process
The choice of welding process significantly impacts the suitability of different tack weld types.
- With its inherent control over heat input, MIG welding is adaptable to a wide range of tacking applications.
- TIG welding, renowned for its precise control over heat, excels in delicate tacking operations, particularly on thin materials where minimizing distortion is paramount.
- Stick welding, while versatile, may offer less precise control over heat input compared to MIG or TIG.
Application Requirements
The final weld’s intended function dictates the tack welds’ necessary characteristics.
For applications demanding high strength and durability, permanent tacks that contribute to the overall strength of the joint are crucial.
In applications subject to cyclic loading or vibration, tack weld placement and size must be carefully considered to minimize stress concentrations and enhance fatigue resistance.
Material Properties
The inherent properties of the base metals significantly influence the tack welding process.
Materials with high thermal conductivity, such as aluminum, dissipate heat rapidly, necessitating faster welding speeds and potentially smaller tacks to prevent excessive heat input.
Materials with high coefficients of thermal expansion are more susceptible to distortion during welding. Therefore, carefully considering heat input and tack weld size is crucial to minimize the risk of warping or buckling.
How to Choose the Right Tack Weld
- Carefully analyze the specific requirements of the welding application, including the joint type, material properties, and intended use of the final weld.
- Select tack weld sizes appropriate for the thickness of the metals being joined. Avoid using excessively large tacks on thin materials, as this can increase the risk of distortion.
- Choose tack weld placements that will effectively maintain the desired joint alignment and minimize the risk of distortion during the final welding process.
- Consider the suitability of different welding processes for the specific application and choose tack weld types compatible with the selected process.
- Take into account the thermal properties and susceptibility to distortion of the materials being welded. Choose tack weld types and parameters that minimize the risk of heat-induced distortion.
Conclusion
To conclude, the types of tack welds, you can see there is no best choice in these options. Every single one has its unique application, and you need to determine which one aligns with your needs the best.
The goal of our discussion was to help you find the right pick for your particular need. Follow the tips and strategies we shared, and you will surely get the perfect tack weld type required for your project.
Great, Together