Introduction
CNC milling is one of the most used CNC machining operations for manufacturing. All CNC processes share some similarities, such as automation through computer codes and programs, ensuring high precision. CNC milling is distinct and highly versatile, making it a mainstay in various industries.
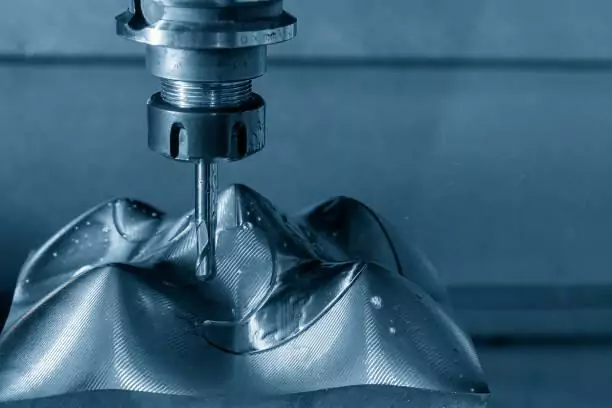
This article is a comprehensive guide to CNC milling operations. It encompasses all you need to know about the process, its capabilities, benefits, limitations, and applications, which may prove pivotal before choosing it for your next manufacturing project.
What Is CNC Milling?
CNC milling is an automated process that uses a series of rotating cutting tools to remove components of a workpiece. As the name of the process suggests, the operation uses computer-controlled machines to exert precise movement of the cutters, ensuring dimensional accuracy.
The process is highly versatile, suitable for various operations, performing various milling operations, creating undercuts, pockets, internal channels, and other intricate features. CNC milling offers numerous advantages.
How Does CNC Milling Work?
CNC milling is one of the most used CNC machining techniques. While milling, drilling, and turning are all aspects of CNC machining, there are intricate distinctions between each process. That said, this section will discuss precisely how CNC milling works.
Preparation of CAD Files
All CNC machining operations start with creating the Computer-Aided Design (CAD) that serves as the 2D or 3D format of the intended product. To prepare a CAD file for CNC milling involves using software like SolidWorks or Autodesk. This CAD file serves as the okie print for the entire milling process, with specifications indicating the part’s shape, dimensions, geometry, tolerance, finishing, and other intricate features.
Export Design to CNC Compatible Format
After creating the CAD file, you must convert it into what the CNC device can understand using appropriate Computer-Aided Manufacturing (CAM) software. This software, such as Convert.emachineshop.com and cad-exchanger, translates the design into machine-readable codes (often G or M-codes); this includes the tool path and movement, cutting sequence, feed rate, and other intricate parameters of the milling process.
Machine Setup
After changing the CAD files into machine-readable formats such as STL and STEP, the CNC machine is ready for actual milling. Then, the machinist or operator confirms the appropriate CNC milling machine setup. This includes securing the workpiece in the machine, loading the proper cutting tools, and setting coordinates for accurate positioning.
Milling
Upon confirmation of the accurate machine setup, the actual milling process can commence. The machine will have to attach the cutters to the spindle and set up the device to kickstart milling. The cutters will move along specific paths as indicated by the codes, cutting and removing pieces of material from the workpiece in a controlled and specified manner.
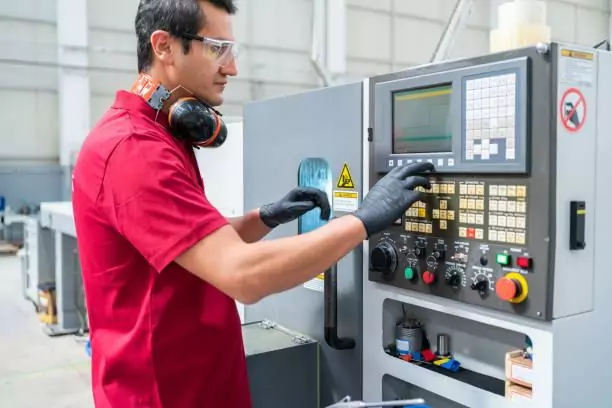
Types of CNC Milling Operations
CNC milling involves a series of different cutting operations, each specific for distinct machining purposes. Below is a concise but detailed overview of CNC milling types.
Face Milling
As a type of CNC milling operation, face milling is when the cutting tool – usually a face milling cutter – rotational axis is right-angled to the surface of the workpiece. The cutting tools have cutting teeth at the tool’s face and periphery. While the peripheral teet is responsible for the actual cutting operation, face teeth help in finishing. Therefore, face-milled parts tend to have high-quality, precise, and smooth surface finishing.
Face milling is typically for creating flat surfaces and contours on already machined parts; compared to other milling operations, it also serves as a type of surface finishing. This CNC milling process may include different types, such as side milling and end milling in CNC milling.
End Milling
End milling uses specific cutters, called end mills, to remove materials off a workpiece, creating axial cuts. The mills come in varying designs, such as the square end, ball end, and flat surface end mills. End milling is for creating flat surfaces, contours, and slots.
Side Milling
As the name suggests, side milling involves cutting along the sides of a workpiece. As the side mill cutters cut through the material slides, it creates some sort of lateral motion. This milling process is suitable for creating flat vertical and angular surfaces, reshaping the sides of a part, or removing extra material off the workpiece edges.
Either vertical or horizontal CNC milling machines can perform all kinds of face milling operations.
Plain Milling
In this milling operation, the rotation axis of the cutting tool is parallel to the workpiece’s surface. Because plain milling is typically used for plain horizontal surfaces, it is sometimes called surface or slab milling. Like other milling operations, it uses specific cutters – plain milling cutters – with the cutting teeth predominant at the periphery that cuts through the workpiece.
Plain milling could employ narrow or wide cutters to create vertical, cross, or longitudinal cuts, depending on the milling specifications or applications. For example, narrow cutters are tailored for wider cuts, while the broader ones are for cutting through larger surface areas. Plain milling is a versatile operation suitable for creating flat surfaces, keyways, or slots.
Form Milling
Form Milling is the go-to milling operation for creating complex, irregular shapes, outlines, and contours on a workpiece. The process utilizes formed milling cutters or fly cutters specific for this operation to create these contours on parts with curved and flat surfaces or completely curved surfaces – either in concave or convex orientation.
This operation creates semi-circular or hemispherical cavities, beads, and contours, including intricate designs and custom features. However, because of the complexities and surface curvature, this operation is slightly slower than regular milling operations, up to 30 percent.
Angular Milling
As the name suggests, angular milling involves milling operations where the cutting edge of the cutters is placed at an angle to the surface of the workpiece. It’s pretty similar to plain milling, with the main distinction being the angular setup of the cutting axis.
Angular milling uses single-angle millers to create angular features such as serrations, bevels, chamfers, and groves. These cutters have angled cutting edges, making them suitable for working angles at 45, 50, 55, or 60 degrees, such as in making dovetails. There are also double angular cutters, which typically have V-shaped teeth and are best suited for milling flat surfaces at angles 90, 60, and 45 degrees.
Other Types
Besides the more predominant types of CNC milling operations, below are some other types.
Peripheral Milling
Peripheral milling is similar to plain milling, with its cutting axis typically parallel to the workpiece. It involves cutting along the outer edge – the periphery – of a workpiece. This milling technique is suitable for parts that require delicate details at the edges and for creating profiles, contours, and grooves.
Slot Milling
Slot milling is also called groove milling, with either name describing the technique. It is used explicitly for creating slots and grooves in a workpiece. The operation is highly versatile and used for creating T-slots and keyways.
Thread Milling
Again, as the name suggests, thread milling is specific for creating threaded features on a workpiece through the rotatory movement of the cutting tool. Whether internal or external threads, the technique creates precise and accurate threading features in a workpiece.
Pocket Milling
Pocket milling operation creates enclosed pockets or recesses, like undercuts in a workpiece. The technique is specific for creating internal delicate features such as pockets for bearings.
Material Selection for CNC Milling Operations
CNC milling is compatible with various material types. This section will discuss material selection for CNC milling process in two categories.
Factors that Determine Choice of Materials for CNC Milling
Before selecting materials, there are critical factors that you must consider. They help determine the suitability of the material for a specific milling project.
Below are some of the critical factors that require such considerations.
- Parts’ Tolerance: The tolerance rating of a material influences the dimensional accuracy of the final product. Therefore, when manufacturing parts with tight-tolerance specifications, you must factor in the parts tolerance to ensure that your end product suits its intended application.
- Cost: Material cost is another critical factor, with some materials being quite expensive. Balancing material costs with desired property and factoring your budget is highly vital.
- Part’s Function: The intended function of the fabrication also plays a crucial role in material choice. For example, in the aerospace industry, aluminum or titanium are the go-to materials for applications that require considerable strength and are lightweight. However, if strength is the defining criterion, stainless steel may be a more suitable material.
- Stress: Again, different materials have varying stress and fatigue resistance. Therefore, depending on the project’s requirement, the tensile strength of the material is a crucial factor to prevent deformation or even fabrication failure.
Examples of Materials for CNC Milling
One of the main benefits of CNC operations, including CNC milling, is its compatibility with a vast range of materials. Below are typical materials that suit CNC milling.
- Metals and Aloys: This includes lightweight and high-density metals and alloys. Examples of metals for CNC milling include aluminum, steel, stainless steel, titanium, brass, and copper.
- Plastics: CNC milling is compatible with various plastics and resins, especially engineering-grade polymers. Examples include acrylic, nylon, polyethylene, polypropylene, PVC, etc.
- Others: This includes other kinds of materials besides metals and plastics. Materials like composites, wood, and sometimes ceramics are used for CNC milling.
Advantages of CNC Milling
CNC milling is versatile, making it one of the most preferred methods in various industries. Below are some of its main benefits.
High Precision and Dimensional Accuracy
Like all CNC operations, CNC milling is a high-precision operation, as it creates parts with impeccable precision and dimensional accuracy. Since it’s a computer-controlled process, there’s little human interference. Therefore, there are minimal risks of error, like in manual machining. This makes it a suitable technique for parts and components with tight tolerance specifications of up to ±0.001 inches; in fact, some machines can achieve ±0.0005 inches.
Compatibility With Vast Materials Options
CNC milling is compatible with vast kinds of material options. We already discussed some material choices available to CNC machinists during parts fabrication. The device can machine workpieces made of varying materials, including plastics, metals, alloys, composites, and even wood and sometimes ceramic.
Quick and Efficient
Since the operations of CNC milling are computer-guided, it is a highly efficient method. After setting up the computer-aided design and coding the machine, it can carry out its operations independently. The high level of automation and repeatability of CNC milling helps to reduce lead times, as the device can operate 24/7 if necessary, further increasing production rates. Therefore, you have a higher chance of meeting tight deadlines.
Suitable for Complex Geometries
Regardless of design constraints and geometric complexities, CNC milling operations are suitable. Provided the instructions and codes guiding the operation of the device are optimized correctly, it ensures precise control of the cutter’s tool path and depth for high accuracy. Generally, CNC milling processes are the go-to machining operations for creating intricate features, including pockets, undercuts, and contours.
Limitations to CNC Milling
Even with its numerous advantages, CNC milling still has some limitations. Understanding the shortcomings is critical for ensuring your CNC milling projects achieve all the intended specifications.
High Initial Costs
Generally, all CNC machines, including CNC milling equipment and software, are expensive. Therefore, the initial CNC milling machine setup is usually cost-intensive, which is often a limitation, especially for startups and small-scale businesses. However, since these machines and their other components are highly durable, the long-term benefit of acquiring the device may outweigh its initial cost.
Tool Wear
Tool wear and tear is more or less a constant in CNC milling. The constant contact between the cutting tool and the workpiece gradually wears the cutters. Other factors, such as the hardness of the material and increased cutting speeds, may increase tool wearing. When this happens, the tools require replacement or periodic sharpening, increasing maintenance costs.
Requires Expertise
CNC milling machines require expert machinists and operators to ensure optimum machining. The device requires correct coding and programming, which often requires the machinists to have a sound understanding of programming languages. Also, other aspects such as tool selection, machining techniques, machine and workpiece setup, troubleshooting, and problem diagnosis all require the services of experts.
Applications of CNC Milling Operations
CNC milling is arguably the most used precision machining technique because of its vast applications in various industries. Below are some:
- Aerospace Industry: Aircraft parts, structural elements, engine components, and other specialized parts with tight tolerance and quality standards and strict safety measures.
- Agriculture: Parts for large agricultural machinery, irrigation systems, and specialized toolings
- Automotive Industry: Engine parts, chassis components, transmission and gearing systems, car interior and exterior parts.
- Electronics: Electronic casings and enclosures, heat sinks
- Energy and Renewable Energy: Generator parts, turbines, solar panel components, and renewable energy systems
- General Manufacturing and Custom Parts Fabrication: Creation of custom parts, molds, toolings, machine parts, and custom automotive components
- Medical Industry: Surgical instruments and implants, prosthetics, orthopedic equipment, dental tools, and other features with strict safety and quality specifications
Factors that Determine the Cost of CNC Milling
Different factors can affect the total cost of CNC milling operations. Below is a brief overview of some of them.
Design Complexity
The design’s complexity plays a crucial role in the total cost of CNC milling services. Parts with more intricate and delicate designers tend to require special cutting tools, increased expertise levels, and longer lead times, resulting in increased costs. In fact, some complex geometries, especially those with extra features like undercuts, require multi-axis machining, which is even more expensive than conventional CNC machines.
Types of CNC Milling Machine
The choice of the CNC milling machine also plays a pivotal role in CNC milling costs. If a design requires more sophisticated CNC devices, or say, a client specifically asked for advanced CNC machines – the multi-axis machines – they’ll have to pay more. Indeed, these machines offer extended capabilities and ensure optimal fabrication, regardless of the complexities. However, they also attract more costs.
Choice of Material
The selected material for CNC milling purposes also affects the total costs. Material impacts costs in two ways: first, the actual material cost. Some materials like iron, aluminum, and steel are relatively cheap, while titanium and nickel-based alloys are expensive. The other way the choice of material affects costs is the ease of machining. Materials like titanium are challenging to machine and may result in longer production times, increased tool wear, and maintenance requirements, resulting in increased CNC milling costs.
Production Volume
The volume of production also impacts CNC milling costs. While you’d expect low-volume production to be cheaper than high-volume, it’s not that direct, especially when discussing the cost per part. CNC machining is expensive, but it’s cost-effective for bulk manufacturing.
This is because the cost of manufacturing a few products and large products share similarities in the cost factors, including coding, tooling, setup costs, tool changing, etc. Therefore, besides buying more materials in bulk production, other integral aspects of the project are shared over the total fabrication, resulting in reduced costs per part.
Choice of Surface Finishing
While CNC machining yields parts with high precision and accuracy, requiring little to no surface finishing, you can still choose to engage in these operations to improve the part further. However, the selected finish and post-processing operations influence the total costs. Therefore, if on a strict budget, consider a less cost-intensive surface finish for your part or leave it as machined.
Future Trends in CNC Milling Services
With non-stop technological advancements, CNC milling operations continue to witness improvements to meet modern and futuristic manufacturing demands. This section will discuss the prominent trends that encompass the future of CNC milling services.
Automation of the Milling Processes
CNC automation is integral to CNC milling operations. Besides the operational codes of these devices, integrating robotic systems into CNC machines can further reduce human interference, increasing precision. Manufacturers and OEMs can use robots to carry out simple tasks such as tool changing, material handling, workpiece loading and unloading, and even quality analysis. Automating these processes helps enhance the repeatability and efficiency of CNC operations.
Machine Learning (ML) and Use of Artificial Intelligence (AI)
Machine learning and AI are already making headway in CNC milling. Coders and software engineers can use this tech to equip CNC devices with learning abilities, further optimizing machining operations.
Integrating ML and AI algorithms may help predict tool wear, a favorable took path, predict and prevent machining defects, minimize wastes, and modify cutting parameters in real-time. This may also include features like self-monitoring, scheduling maintenance, and diagnosing itself in the case of a fault. These features result in increased tool life and overall machine efficiency.
Conclusion
CNC milling is a popular manufacturing technique for various industrial applications. The method offers vast capabilities, ranging from simple manufacturing to the fabrication of sophisticated components with intricate design features.
Even with the ever-dynamic manufacturing world, CNC milling has refused to stop evolving, ensuring it’ll remain a mainstay for years.
Zintilon’s Custom CNC Milling Services
Reading this article this far, you probably have a detailed understanding of CNC milling. However, you still need to partner with a service, as acquiring the machines for your project is cost-intensive, especially if it’s just for a small-scale or one-time custom part fabrication.
Zintillon is an expert in offering high-quality CNC milling services. Whether it’s simple parts or complex parts fabrication with tight tolerance specifications, we adhere to your requirements.
Our facility boasts highly skilled operators and the necessary equipment to give life to your dream project. Besides CNC milling, we offer other CNC machining operations – turning, drilling, etc., including related technology like EDM, sheet metal fabrication, and die casting.
FAQs
Is CNC Milling Different From CNC Machining?
CNC milling is a subset of CNC machining operations. Indeed, CNC milling is vast; it involves explicitly using rotating cutters to reshape a material. On the other hand, CNC machining includes various processes, including milling, boring, turning, drilling, and routing, among others.
Why is Milling Better than Turning?
Milling offers a broader range of applications. It is suitable for creating flat and complex shapes, including contours, recesses, undercuts, and other intricate details. On the other hand, turning is preferred for cylindrical structures.
What is the Difference Between Manual Milling and CNC Milling?
Manual milling operation requires human operators to control the machine’s functions, while CNC milling is automated and controlled by computer programs and codes. Therefore, CNC milling can create complex parts and offers precision and repeatability beyond manual milling.
What’s the Difference Between CNC Milling and CNC Turning?
In CNC milling, rotary cutting tools remove pieces of a workpiece, while in CNC turning, the cutters are stationary, with the workpiece rotating as pieces are chipped off. While both subtractive manufacturing processes may seem similar, they serve different purposes. Turning is more specific for cylindrical components, while milling has more vast applications, ranging from flat to complex structures.
Great, Together