5 axis CNC machining uses a machine that can simultaneously move and rotate in five axes to machine a part. Its benefits include its high suitability for fabricating parts with complex designs and intricate details, accuracy, speed, and production efficiency.
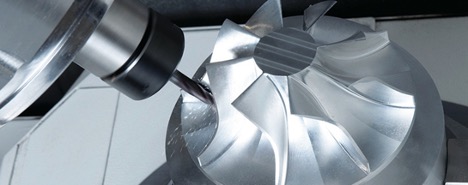
Picture the most sophisticated CNC machined part you have ever seen; there is a high chance that its manufacturers relied on 5-axis machining. However, using the process or outsourcing to a CNC machining center should only come after understanding it.
This article will guide you through the CNC machining process, aiming for successful integration into your project. It will define the process, explain how it works, and describe its typical applications.
What is 5 Axis CNC Machining?
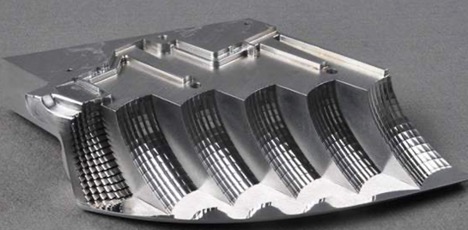
5 axis CNC machining is a class of CNC machining that relies on using a 5-axis CNC machine that can simultaneously move and rotate five axes (three linear and two rotational).
Generally speaking, the three linear axes are the fundamental axes that aid in cutting. The three rotational axes are auxiliary, and the machine can only access two. They only help properly orient the workpiece (they do not participate in cutting).
There is also a limit on the number of axes you can simultaneously link to five because it can lead to a higher control system complexity, programming complexity, and mechanical constraints.
The 5 axis CNC setup is more diverse than the traditional 3-axis and 4-axis CNC setup due to the number of axes it can move and rotate. Furthermore, its configuration eliminates the need for multiple setups. As a result, there is less need for supervision, and there is improved production efficiency.
What Does 5 Axis Stand for?
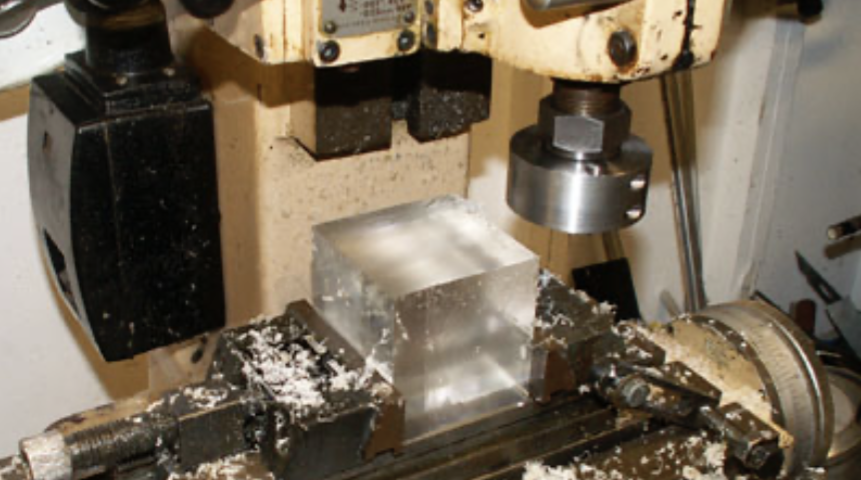
“5 axis” in the CNC machining technique represents the five axes the cutting tool can simultaneously move and rotate along. The typical CNC machine has three linear axes (fundamental axes) and three rotational axes (A, B, and C) and the 5 axis machine will move along the linear axes and two of the rotational axes.
X-axis
The X-axis represents the cutting tool’s horizontal movement along the machine bed length, and it can be left to right or right to left, depending on the machine configuration. Movement along the X-axis enables CNC machining operations like milling, drilling, and contouring.
Y-Axis
The Y-axis represents the cutting tool’s lateral movement and it can be front to back or back to front, depending on the machine configuration. Movement along the Y-axis enables CNC machining operations like side milling, slotting, and profiling.
Z-Axis
The Z-axis represents the cutting tool’s vertical movement. The movement can be up and down depending on the 5-axis CNC machine type. Movement along the Z-axis enables CNC machining operations such as drilling, tapping, and boring.
A-Axis
The A-axis represents the cutting tool’s rotational movement around the X-axis – tilting or swiveling. This axis allows more flexibility and compatibility with undercuts, chamfers, and angled features.
B-Axis
The B-axis represents the cutting tool’s rotational movement around the Y-axis. This axis allows for multi-sided machining and machining features like deep pockets, intricate contours, and curved surfaces.
C-Axis
The C-axis represents the cutting tool’s rotational movement around the Z-axis – it tilts or swivels vertically.
Comparison between 3-axis, 4-axis, 3+2-axis, and 5-axis CNC machining
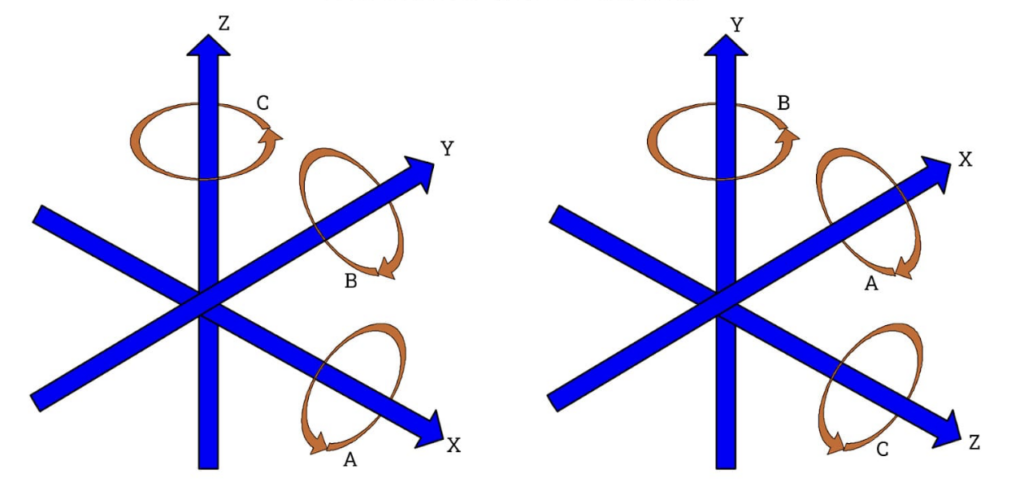
The significant difference between the different classes of CNC machines is the number of axes the cutting tool can move or rotate. The table below highlights the differences and similarities between 3-axis, 4-axis, 3+2-axis, and 5-axis CNC machines.
Feature | 3-Axis CNC Machining | 4-Axis CNC Machining | 3+2-Axis CNC Machining | 5-Axis CNC Machining |
Description | Suitable for basic CNC machining operations. The cutting tool can move along three axes (X, Y, and Z) | It is suitable for complex machining due to its ability to rotate along the horizontal axis. (i.e., the addition of the rotational axis (A-axis). | The cutting tool moves simultaneously in the 3-axis and rotates in two indexed rotational axes. However, switching from the three axes to the rotational axes requires constant repositioning. | The cutting tool can move simultaneously along five axes. |
X-Axis | Yes | Yes | Yes | Yes |
Y-Axis | Yes | Yes | Yes | Yes |
Z-Axis | Yes | Yes | Yes | Yes |
A-Axis | No | Yes | Yes | Yes |
B-Axis | No | No | Yes | Yes |
Types of 5 Axis CNC Machines
The main distinction between the different types of 5-axis CNC machines is the rotational axis location (machine spindle head or the table). Below are the three common types of 5-axis CNC systems so you can choose the right one for your project.
Head/Head
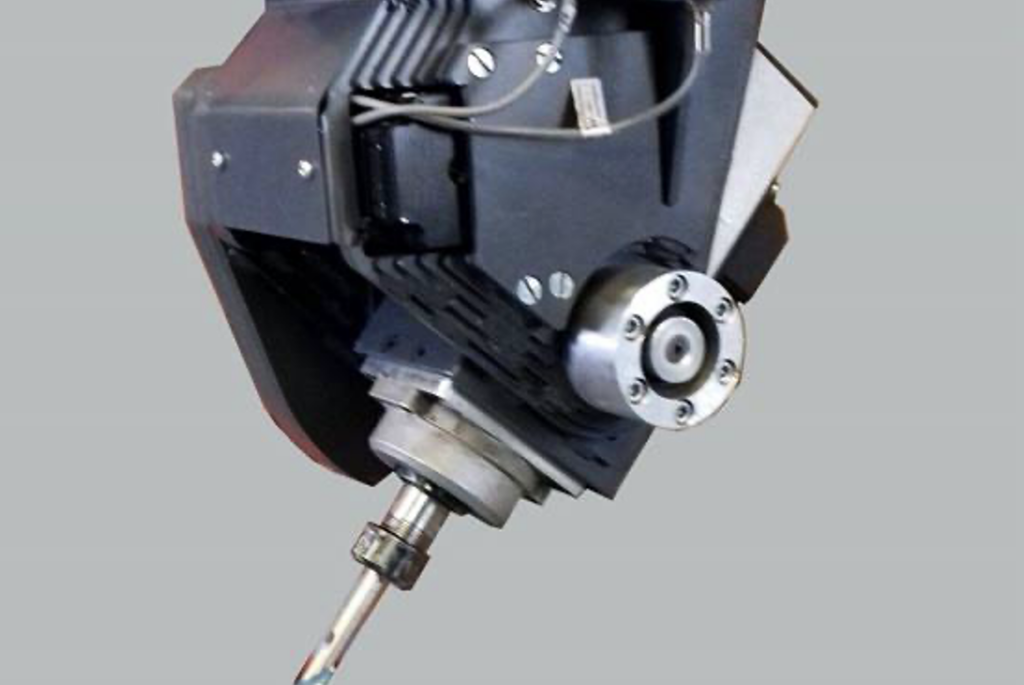
Head/Head 5-axis machines have two revolving axes in the machine spindle head. As a result, there is no tool interference as the table is fixed, which ensures a stationary workpiece.
The location of the revolving axis also ensures that the 5 axis machines under this category can move around the workpiece. Consequently, they are suitable for machining large parts. Conversely, there is still a limitation in movement due to the focus of the two rotary axes in the head and the stationary table.
Table/Head
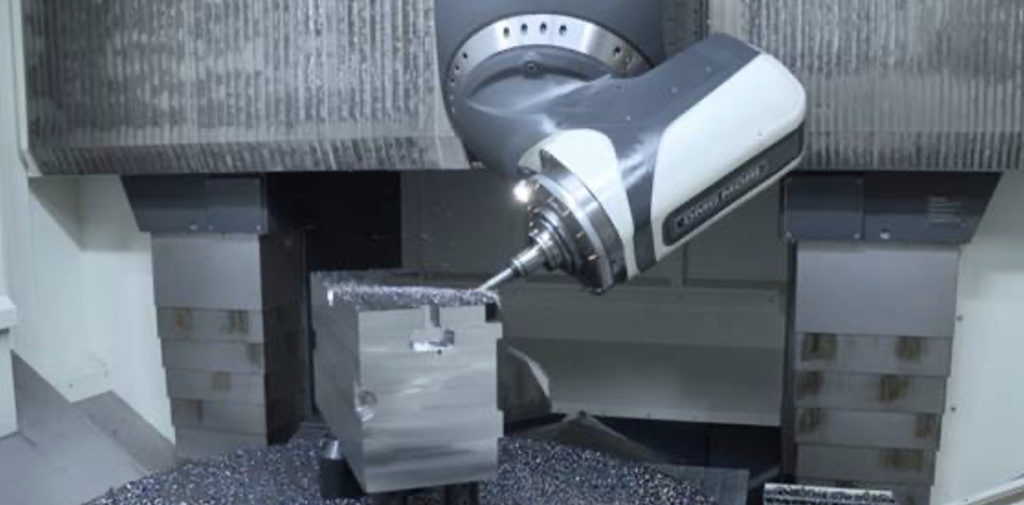
CNC machines with the Table/Head configuration have two rotary axes in the head and on the table. The revolving axis in the head has a restricted range due to its position, while the rotary shaft placed on the table has no limit.
An advantage of the Table/Head axis machining over the Head/Head is that there is no limitation because the parts are consistently revolving. Conversely, because the workpiece rests on the rotary axis, the number of items that can be machined is limited.
Table/Table
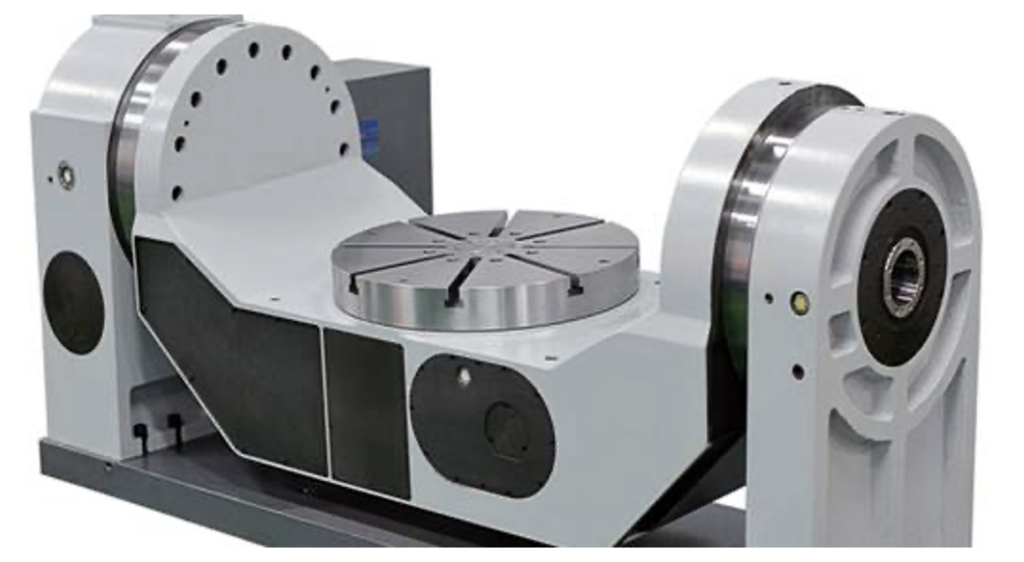
A table/table 5-axis machine has both rotary axes on the table. This limits the revolving axis, making the machine only suitable for machining undercuts. Furthermore, the Table/Table has a minimal work envelope and is slower (it does not come with motors) than other 5-axis CNC machine types. It is unsuitable for machining large or heavy components.
Pros of 5 Axis CNC Machining
5 axis CNC systems continue to be a good machining option for many part manufacturers due to the immense benefits highlighted below:
Suitable for complex designs
The most common reason part manufacturers go for 5 axis cnc machines is their suitability for complex machine shapes. Before its development, such parts are made using casting, a process known for its longer lead time. In contrast, 5-axis machines are fast, and their additional movements make it possible to machine parts at different angles and arcs without special fixtures or additional setups.
Reduced re-fixturing
5 axis CNC machining removes the need to make a part in sections, which needs fixturing. The machine can approach the workpiece at different angles at fewer setups.
Reduced labor cost-per-part
5-axis CNC machining eliminates time and cost because the machine operator does not touch the workpiece; re-fixturing is unnecessary.
Better surface finishes
Other CNC machines, especially 3-axis machines, require longer lead times for better surface finishes. However, 5-axis machines can achieve better surface finish in reduced time. You can ensure a better surface finish by using short-cutting tools for reduced vibration
Feature-to-feature accuracy
5-axis machines have a Zero or Home feature that reduces inaccuracies due to changes in the setup or losing alignment due to removing the part from the machine. Furthermore, there is a reduced possibility of incorrect alignment during machining.
Faster cutting speeds
5-axis CNC machines have shorter tools, which ensures faster cutting speeds, reduced load on the cutter, and reduced vibration and breakage, thereby increasing the tool’s longevity. Also, drilling is faster than traditional CNC machines due to the additional rotation axes that encourage better head orientation.
Cons of 5 Axis CNC Machining
Naturally, these types of CNC machines also have their limitations, and they include the following:
Cost
Incorporating a 5 axis CNC machine into your machine setup will incur a large cost higher than traditional CNC machining centers. Furthermore, the maintenance cost is higher due to its higher complexity. You can reduce the cost by outsourcing to a CNC machining provider that provides 5-axis machining service.
CAD / CAM Programming
Programming the motion of each axis is harder because the two additional rotational axes are incorporated alongside the three linear motions. This means you must consider each axis’s motion to prevent interference and collision. Because of the complexity and the need for machining precision and surface quality, you might require the service of a qualified CAD/CAM programmer.
Requires Advanced Operator Skills
Aside from the complex CAD/CAM programming, 5-axis machining requires highly skilled operators due to advanced technology.
How to Configure a 5 Axis CNC Machine
Configuring a 5-axis cnc machine is easy because it does not require complex clamping systems or fixtures to hold the workpiece.
Prepare Holding Equipment
Mount the workpiece securely at the machine table center using a zero clamp vice, hydraulic clamp, or a securely mounted block. Before machining, the workpiece must be secure and accessible from all five sides.
Prepare Cutting Tools
Prepare, measure, and load cutting tools and tool holders into the machine’s Automatic Tool Changer (ATC) magazine.
Perform Calibration
Before production starts, calibrate the machine using specific software and an automatic measuring probe. This ensures accurate calibration on all axes and minimizes tolerance accumulation.
Check for Potential Collisions
Before starting the machining cycle, carefully check for any potential collision areas. Verify the correctness of each position and the accuracy of every tool change.
Run Pre-Program Check
Allow the entire program to run step-by-step to verify the correctness of each position and tool change. This helps prevent crashes and ensures smooth operation.
Applications of 5 Axis CNC Machining
5-axis CNC machining reduces human errors, improves consistency, and ensures high-quality machining. The following industries use the CNC machining technique in their part manufacturing.
Aerospace Industry
The aerospace industry increasingly relies on 5-axis machining because of its accuracy and because many aerospace parts have complex designs and need machine-to-machine, difficult-to-reach areas. A typical example of 5 axis machined part is the turbine blades, first cast and then machined to achieve the desired shape and surface finish.
Automotive Industry
The automotive industry relies on 5-axis machines due to the need for consistency and the tight tolerance required in making its tools. The industry mostly favors low-cost manufacturing options such as die-casting and injection molding, with the 5 axis CNC machines used in mold manufacturing and other tooling processes.
Medical Industry
The medical industry requires a manufacturing process that can achieve quality and is compatible with different materials. Although 3- and 4-axis machining is suitable for the industry, when working with complex parts, 5 axis machining is better. Furthermore, CNC machines are applicable in medical impellers and CT scanner components.
Energy Industry
The energy industry is the backbone of all other sectors; it requires advanced components pushing engineering and material use limits. Hence, it continuously relies on 5-axis CNC machining. Examples of 5-axis CNC machined parts in the energy industry are drill bits, pistons, cylinders, rods, cylinders, and valves.
Industrial sector
The industrial sector has an enormous scope, requiring complex components for which 5-axis machines are also suitable. However, they function more in a supporting role as general CNC machines such as 3- and 4-axis machines are the common options due to the cost and the general types of parts produced.
Tips for 5 Axis CNC Machining
To maximize productivity and efficiency during 5-axis machining, you can explore the practices and tips highlighted below:
Optimize your tool paths
Optimizing the tool path involves selecting the most efficient and effective paths to ensure minimal waste and maximum accuracy during machining. Software tools can be used to optimize the tool paths. Adaptive milling, which allows the CNC machine to adjust the cutting speed and depth based on the workpiece, can also be used.
Use the right tools and materials
Use the right tool and material to ensure high-quality machined parts, reduced waste, and shorter machining time.
When selecting the tool, consider the following:
- Material being cut
- Depth of cut
- Desired finish.
High-speed steel (HSS) tools are the best for soft materials, carbide tools are suitable for harder materials, and diamond-coated tools are suitable for abrasive materials such as composites and ceramics.
When selecting a material, consider its properties and how they align with the final part of the application. For example, choose titanium or stainless steel for high-strength parts and aluminum or magnesium for lightweight parts.
Maintain your machine and tools
Regular maintenance of the 5-axis CNC milling machine and other tools will ensure you operate at peak performance, reduce downtime, and improve part quality. Maintenance practices include:
- Keeping the machine clean regularly
- Lubricate the machine components as per the manufacturer’s recommendations
- Sharpening and replacing the tools using the manufacturer’s recommendations
Optimize your cutting parameters
Optimize cutting parameters such as cutting speed, feed rate, and depth of cut to reduce machining time and improve part quality. You can start with low values and gradually increase them for the desired result. Furthermore, they should be monitored during machining and adjusted as necessary.
Use simulation software
With simulation software such as VERICUT, you can visualize the 5 axis CNC machining process before machining begins. As a result, you can optimize your tool paths, cutting parameters to improve the tool path.
Zintilon 5-Axis CNC Machining Service
Ensuring quality in 5 axis CNC machining requires skills. Hence, the best way to achieve quality at an affordable cost is by outsourcing to a reputable 5 axis CNC machining service provider.
At Zintilon, we offer quality 5 axis CNC machining services for different industries. Our teams of engineers are experts in CNC machining materials selection and will offer you recommendations for high-quality machining
Contact us today and experience a faster lead time and competitive market pricing.
Conclusion
5-axis CNC machining allows you to make parts with complex designs while enjoying benefits such as easier machining operations, speed, and production efficiency. This article discussed the machining class, how it works, and its applications. Looking for a CNC machining service? Contact us.
FAQ
What is the most used CNC machine?
The most used CNC machine is the 3-axis CNC machine. Its simple setup allows the cutting tool to move along the three axes (X, Y, and Z), making it suitable for basic CNC machining operations such as milling, drilling, and other cutting operations.
How many axes can a CNC machining have?
The number of axes a CNC machine can move can be up to 12, allowing movement along X, Y, Z, A, B, and C axes. Generally, CNC milling machines utilize 2 to 3 of the fundamental axes and two or three rotational axes used to different degree by the 3-axis, 4-axis, or 5-axis machines. This axis aids in cutting. However, any axis aside these are auxiliary, and they only aid in the orientation of the workpiece. Linking a higher number can lead to a more complex control system and programming and mechanical constraints.
Is there a 7 or 6-axis CNC machine?
Yes, there are 6-axis and 7-axis CNC machines with additional rotational axes along the standard X, Y, and Z axes. These machines have increased flexibility and higher precision and are applicable in industries that require very tight tolerances. However, they are not common because the complex control and programming and mechanical constraints that occur when you connect more than 5 at a time doesn’t make sense.
Great, Together