In the world of semiconductor manufacturing and microelectronics, etching plays a crucial role in creating intricate patterns and structures on various materials. Often people struggle to pick between wet etching and dry etching.
Today we will end that struggle with a detailed guide to learn what is the difference between wet and dry etching. We dive deep into both the techniques and give you a little comparison at the end as an overview to choose one.
So, if you are also having trouble picking the right etching technique, go through the whole guide to find your solution.
Wet vs Dry Etching: Which One is Stronger
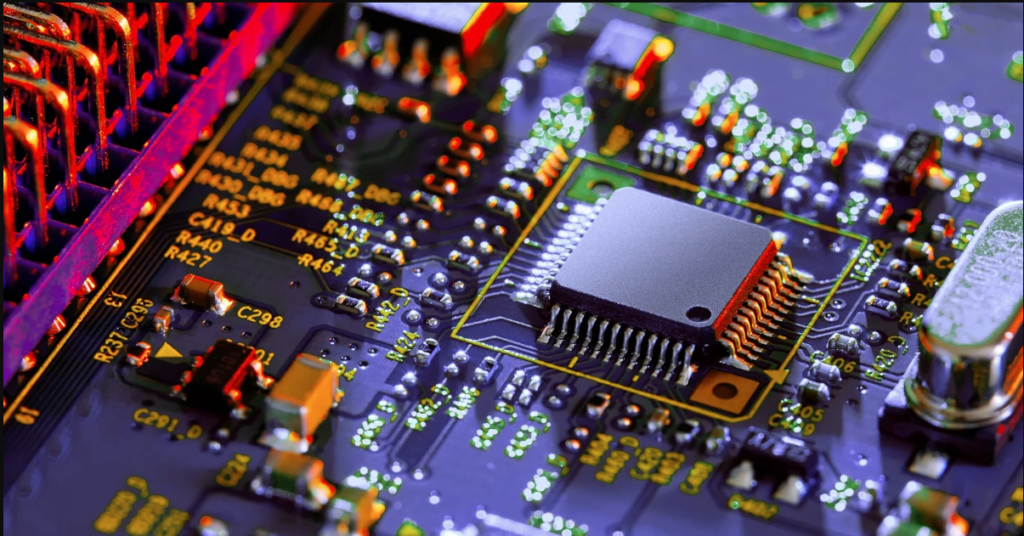
When comparing wet and dry etching, it’s important to note that “stronger” doesn’t necessarily mean better. Each method has its strengths and is better suited for different applications.
The “strength” of each method depends on the specific requirements of the etching process, including the materials involved, the desired feature size, and the level of precision needed.
Let’s explore them in detail to better understand their capabilities and limitations.
Wet Etching
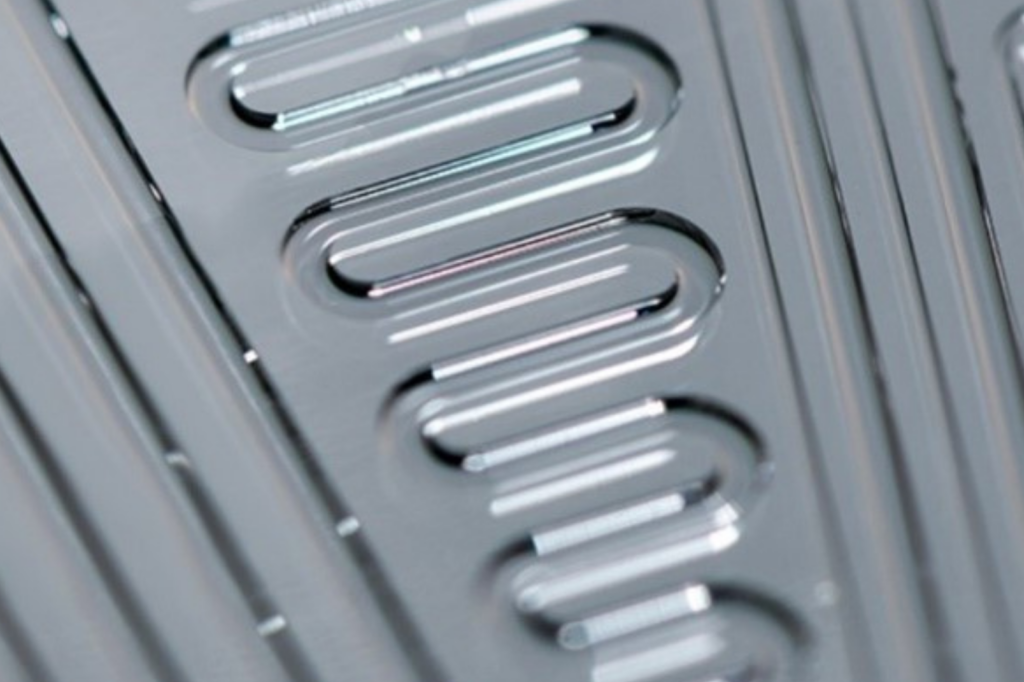
Wet etching is a material removal technique that uses chemical solutions, or etchants, to selectively remove layers of material from a substrate. It’s a common process in various industries, particularly microfabrication and semiconductor manufacturing.
Wet etching generally offers higher etch rates and better selectivity, meaning it can remove material faster and with greater precision between different layers. This makes it particularly effective for large-scale etching and when working with materials that have high etch selectivity.
Types of Wet Etching
- Isotropic Etching: This type etches uniformly in all directions, resulting in a rounded profile.
- Anisotropic Etching: This type of etches preferentially in one direction, creating a more vertical profile.
How to do it?
Wet etching is a chemical process that uses liquid etchants to remove material from a substrate. The basic steps of wet etching are as follows:
- Substrate Preparation: The first step in wet etching is to prepare the substrate for the etching process. This typically involves cleaning the substrate to remove any contaminants that could interfere with the etching process. Common cleaning methods include solvent cleaning, alkaline cleaning, and acid cleaning.
- Masking: A protective layer, often called a photoresist, is applied to the substrate to define the areas that should not be etched. The photoresist is patterned using a lithographic process, exposing the desired areas for etching.
- Etchant Selection: The choice of etchant depends on the material to be etched and the desired etch rate and selectivity. Common etchants include hydrofluoric acid (HF), potassium hydroxide (KOH), and nitric acid (HNO3).
- Etching Process: The substrate is immersed in or sprayed with the etchant solution. The exposed areas react with the etchant, causing them to dissolve. The etch rate can be controlled by adjusting factors such as temperature, concentration of the etchant, and agitation.
- Rinse and Dry: Once the desired etch depth has been achieved, the substrate is rinsed with deionized water to remove any residual etchant. It is then dried, often using a spin dryer.
- Mask Removal: The protective mask is removed after the etching process is complete, leaving behind the desired etched pattern on the substrate. The mask can be removed using a stripping solution or by plasma ashing.
Common etchants used in wet etching include:
- Hydrofluoric acid (HF) for silicon dioxide (SiO2)
- Phosphoric acid (H3PO4) for aluminum
- Nitric acid (HNO3) for copper
- Potassium hydroxide (KOH) for silicon
The choice of etchant depends on the material being etched and the desired etch characteristics.
Features
Wet etching is characterized by several key features:
- Isotropic Etching
Wet etching typically proceeds equally in all directions, resulting in rounded or undercut profiles. This characteristic is often referred to as isotropic etching. While this can be beneficial in certain applications, it can also limit the ability to create high-aspect-ratio structures with vertical sidewalls.
- High Selectivity
Wet etchants can be carefully selected to etch one material much faster than another, allowing for high selectivity between different layers. This selectivity is crucial in applications where it is necessary to remove one material while preserving others.
- High Etch Rates
Wet etching generally offers faster material removal rates compared to dry etching techniques. This can be advantageous in applications where rapid etching is required.
- Chemical Reaction-Based
The etching process in wet etching relies on chemical reactions between the etchant solution and the target material. The choice of etchant and the conditions under which the etching is performed determine the rate and selectivity of the process.
- Temperature-Dependent
The etch rate and selectivity of wet etching can be controlled by adjusting the temperature of the etchant solution. Higher temperatures often lead to increased etch rates, while lower temperatures can improve selectivity.
- Batch Processing
Wet etching is well-suited for batch processing, where multiple wafers can be etched simultaneously in a single bath. This allows for high throughput and can be cost-effective for large-scale production.
Pros
- The chemical nature of wet etching typically results in less surface damage and fewer defects compared to dry etching.
- Wet etchants can be chosen to etch specific materials while leaving others untouched, allowing for precise layer-by-layer etching.
- Wet etching can remove material quickly, making it suitable for thick film removal and large-area etching.
- The method works well with materials like GaAs and InP, which are important in optoelectronics.
- Etch rates can be controlled by adjusting etchant concentration, temperature, and agitation.
Cons
- Etch rates can vary depending on the density of features being etched, leading to non-uniform etching across a wafer.
- Wet etching processes can be challenging to fully automate due to the need for manual handling of chemicals and substrates.
Dry Etching
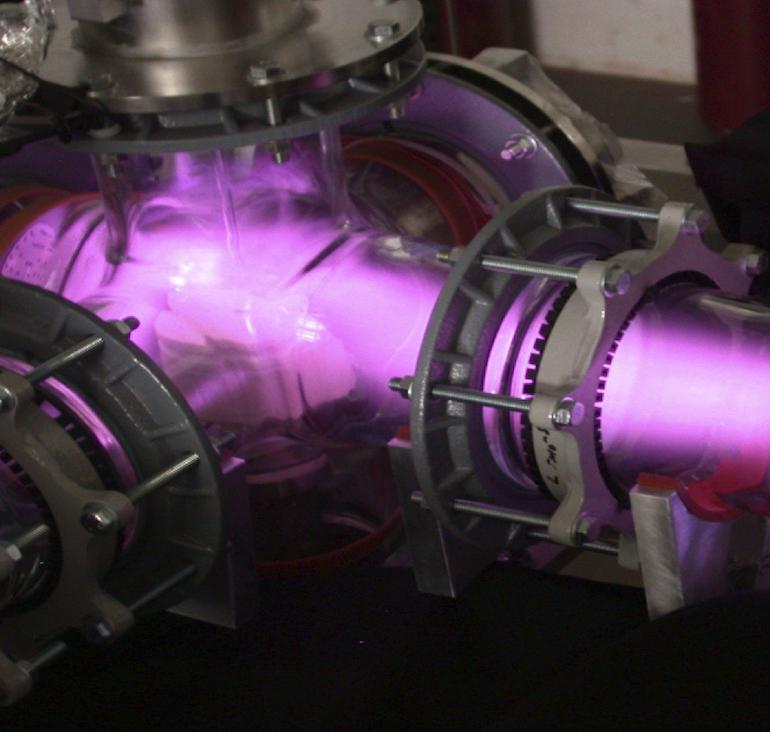
Dry etching is a material removal technique that uses a plasma or a chemically reactive gas to selectively remove layers of material from a substrate. Unlike wet etching, which uses chemical solutions, dry etching is a gas-phase process.
Dry etching provides better anisotropy (directional etching) and finer control over feature sizes. This makes it more suitable for creating smaller, more precise structures, which is crucial in the production of advanced microelectronics.
Types of Dry Etching
- Plasma Etching: Uses a plasma to etch the substrate. This can be further classified into, Reactive Ion Etching which combines plasma etching with ion bombardment, and inductive coupled Plasma Etching which uses a high-density plasma generated by an inductive coil.
- Sputter Etching: Uses a physical bombardment process where ions are accelerated towards the substrate, causing the material to be ejected.
How to do it?
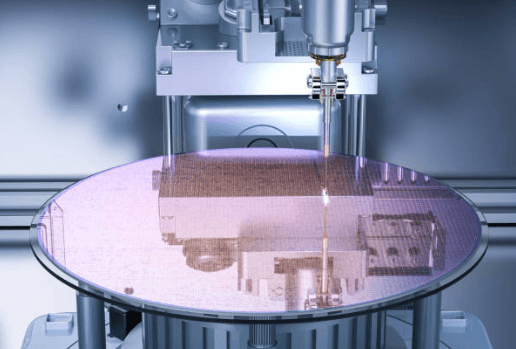
Dry etching is a physical-chemical process that uses gases or plasmas to remove material from a substrate. The basic steps of dry etching are as follows:
- Substrate Preparation: Similar to wet etching, the substrate is cleaned and prepared to ensure a clean surface for the etching process. This may involve solvent cleaning, alkaline cleaning, or other appropriate methods.
- Masking: A protective layer, often a photoresist, is applied to the substrate to define the areas that should not be etched. The photoresist is patterned using a lithographic process.
- Chamber Loading: The substrate is loaded into a vacuum chamber, creating a low-pressure environment.
- Gas Introduction: Etching gases are introduced into the chamber. The choice of gas depends on the material to be etched and the desired etch characteristics. Common gases include CF4, SF6, Cl2, and O2.
- Plasma Generation: In plasma-based dry etching techniques, an electric field is applied to the gases, ionizing them and creating a plasma. The plasma consists of a collection of charged particles (ions and electrons).
- Etching Process: The reactive species in the plasma (ions and radicals) interact with the exposed substrate surface, causing the material to be removed. This can occur through chemical reactions or physical bombardment.
- Byproduct Removal: Volatile byproducts of the etching process, such as etching gases and reaction products, are continuously pumped out of the chamber to maintain a clean etching environment.
- Process Termination: The etching process is stopped when the desired etch depth is reached. This can be determined using endpoint detection systems, which monitor the etching process and signal when the desired depth has been achieved.
- Chamber Purge and Substrate Unloading: After the etching process is complete, the chamber is purged with an inert gas to remove any residual reactive species. The substrate is then unloaded from the chamber.
- Mask Removal: The protective mask is typically removed using a separate process, such as plasma ashing or a chemical stripping solution. This step is necessary to reveal the etched pattern on the substrate.
Features
Dry etching is characterized by several key features:
- Anisotropic Etching
Dry etching is particularly adept at producing highly directional etching profiles, often resulting in vertical sidewalls and deep trenches. This capability is crucial in the fabrication of high-aspect-ratio structures, such as those found in microelectronics and MEMS devices.
- Plasma-Based
The majority of dry etching techniques rely on the use of plasma, a highly energetic state of matter consisting of a collection of charged particles. The plasma is generated by applying an electrical discharge to a gas, creating a reactive environment that can etch various materials.
- Low-pressure
Dry etching processes typically operate under vacuum conditions, with pressures ranging from a few millitorrs to hundreds of millitorrs. This low-pressure environment helps to maintain a clean etching environment and control the reactivity of the plasma.
- Wide Range of Materials
Dry etching is a versatile technique that can be used on a variety of materials, including those that are difficult to etch using wet chemical methods. This versatility is due to the ability to select appropriate etching gases and plasma conditions for different materials.
- In-Situ Monitoring
Many dry etching systems incorporate in-situ monitoring capabilities, allowing for real-time observation of the etching process. Techniques such as optical emission spectroscopy can be used to monitor the plasma conditions and the etch rate.
- Precise Control
Dry etching offers precise control over the etching process through the adjustment of various parameters. Gas flow rates, chamber pressure, RF power, and other factors can be finely tuned to achieve desired etch characteristics, such as etch rate, selectivity, and uniformity.
- Clean Process
Compared to wet etching, dry etching generally produces fewer chemical waste products. This is because the etching process occurs in a gas phase, reducing the generation of liquid waste. As a result, dry etching is often considered a cleaner and more environmentally friendly process.
Pros
- The ability to finely tune process parameters allows for precise control over etch rates, selectivity, and profile.
- Many dry etching systems allow for real-time monitoring of the etch process, enabling precise control of etch depth.
- Dry etching can be easily integrated with other vacuum-based fabrication steps in semiconductor manufacturing.
- The anisotropic nature of dry etching minimizes undercutting of the mask, allowing for more accurate pattern transfer.
- Dry etching often provides better uniformity across the wafer compared to wet etching, especially for small features.
Cons
- Dry etching systems are generally more expensive and complex than wet etching setups.
- Compared to wet etching, dry etching often has lower selectivity between different materials.
Contrast Table
If don’t have much time on your hands, then here’s a quick comparison of the two etching techniques to give you an overview of the differences.
Aspect | Wet Etching | Dry Etching |
Etch mechanism | Chemical reaction | Physical bombardment and/or chemical reaction |
Directionality | Mostly isotropic | Can be highly anisotropic |
Feature size limit | Generally >1 μm | Down to nm scale |
Etch rate | High | Moderate to low |
Selectivity | High | Moderate to low |
Material compatibility | Limited | Wide range |
Equipment cost | Low | High |
Process control | Moderate | High |
Uniformity | Can be non-uniform | Generally uniform |
Damage to substrate | Low | Can be significant |
Waste products | Liquid chemical waste | Gaseous byproducts |
Throughput | High (batch processing) | Lower (often single-wafer) |
Conclusion
Both wet and dry etching play crucial roles in modern semiconductor manufacturing and microelectronics fabrication. Wet etching excels in high-selectivity applications and large-area material removal, while dry etching is indispensable for creating fine features and high aspect ratio structures.
The choice between these techniques depends on the specific requirements of the application, including feature size, materials involved, and desired etch profile. Consider the factors, and you will know which method is best suited for you.
Great, Together