When you are out there trying to look for the perfect techniques to create thin wall parts, you may often come across the low-pressure die-casting technique. It’s a very effective casting technique for producing high-quality parts. But is low-pressure die casting a good fit for thin wall parts?
Well, the clear answer is no. But it’s also crucial to understand why it’s not the most suitable option for thin wall parts. That’s why we take a deep dive into the low-pressure die-casting technique and tell you everything about the technique, as well as why it’s not suitable for such parts.
Overview of Low-Pressure Die Casting
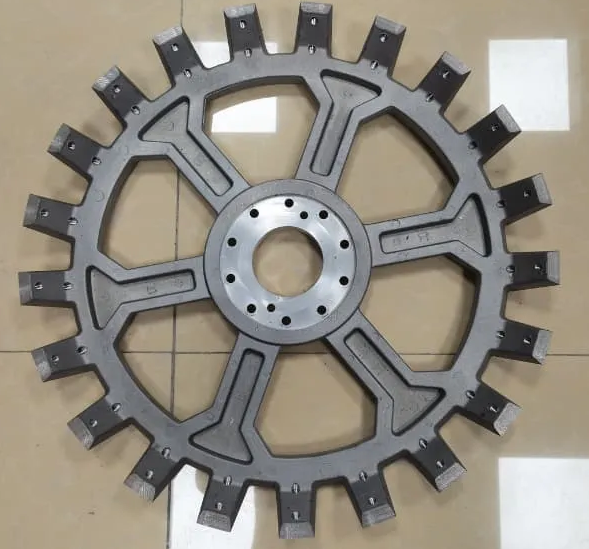
Low-pressure die casting is a metal casting process that has gained popularity in recent years due to its unique advantages. As you explore various manufacturing techniques, you’ll find that this method offers a blend of precision, efficiency, and cost-effectiveness that makes it attractive for many applications.
How it Works
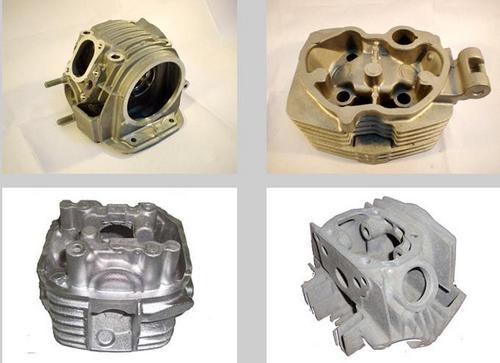
To fully understand the capabilities and limitations of low-pressure die casting, it’s essential to understand how the process works. Here’s a breakdown of the low-pressure die-casting process.
- Mold Preparation: The process begins with the preparation of a precision-machined steel die. This die is thoroughly cleaned and preheated to prevent thermal stress.
- Metal Melting & Transfer: After that, you melt the chosen metal and carefully transfer it to a holding furnace, ensuring a slag-free supply of molten metal.
- Controlled Injection: Then, gently inject the molten metal into the die cavity under low pressure, minimizing air entrapment.
- Solidification: The metal solidifies gradually within the die, with the holding furnace continuously supplying molten metal to compensate for shrinkage.
- Part Ejection: Once solidified, you eject the part from the die and allow the die to cool down before the next cycle.
- Finishing: You may need to perform minor trimming and machining to achieve the desired surface quality.
Applications
You may have already seen the use of low-pressure die-casting techniques but never realized that’s how they are made. Here are some industries where low-pressure die-casting parts are constantly used.
- Automotive: Produces engine blocks, cylinder heads, wheels, and suspension components.
- Aerospace: Used for landing gear, engine parts, and other high-precision components.
- Medical: Manufactures surgical tools, X-ray equipment, and other medical devices.
- Household Appliances: Creates parts for cooking appliances, food processors, and other household items.
- Electrical: Produces motor casings, enclosures, and other electrical components.
- Marine: Used to manufacture pumps, engines, and valves for marine applications.
Materials
Now, let’s discuss the various materials compatible with the low-die casting process. Certain materials work the best for the process, and these typically include –
Material | Advantages |
Aluminum Alloys | Most common, good balance of properties, wide range of applications |
Magnesium Alloys | Highest strength-to-weight ratio, ideal for weight-critical applications |
Zinc Alloys | High dimensional accuracy, excellent surface finish, low melting point |
Copper Alloys | Higher strength and temperature resistance |
Surface Finishes
When you’re considering die casting for your project, understanding the various surface finishes available is crucial. Here are some surface finishes that you can try out –
As-Cast
Basic, rough finish directly from the mold. This is the most economical option, but it may not be suitable for applications requiring precise dimensions or smooth surfaces.
Texturing
Adds patterns or textures using mold modifications. This can enhance grip, improve aesthetics, or mask minor imperfections.
Polishing
Creates a smooth, shiny surface. Polishing is often used for decorative parts or applications requiring high reflectivity.
Shot Blasting
Improves appearance and mechanical properties. Shot blasting can remove surface contaminants, improve fatigue strength, and create a uniform surface texture.
Vibratory Finishing
Ideal for complex shapes and high volumes. This process can deburr parts, remove sharp edges, and improve surface finish.
Painting/Coating
Enhances corrosion resistance, adds color, and improves aesthetics. Common coatings include powder coating, wet painting, anodizing, and electroplating.
What are the challenges of Manufacturing Thin Wall Parts?
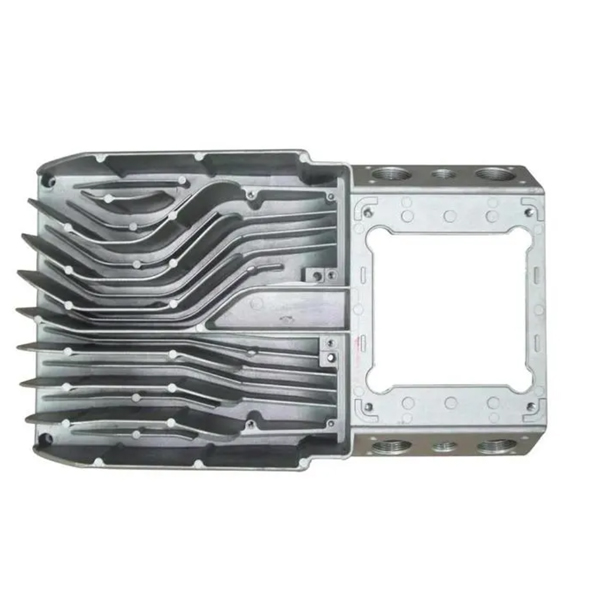
When you plan to manufacture thin wall parts, you have to prepare yourself to face the following challenges. These are common issues that occur during the thin wall parts
Material Flow Issues
Thin sections pose a significant challenge to ensure complete and even filling with molten material. The high surface-to-volume ratio of thin walls leads to rapid heat loss, increasing the viscosity of the molten material and hindering its flow. This can result in incomplete filling of the mold cavity, leaving voids or thin areas in the final part.
Uneven Cooling
Due to their thinness, these parts cool down much faster than thicker sections. This rapid cooling creates uneven temperature gradients within the part, leading to differential shrinkage and the potential for warping, distortion, and the formation of sink marks. The uneven cooling can also induce internal stresses within the part, which can affect its strength and durability.
Warping and Distortion
The significant temperature gradients during cooling can cause differential shrinkage across the part. This differential shrinkage can lead to warping, where the part bends or twists out of shape. Complex geometries and varying wall thicknesses exacerbate these issues, making it more challenging to predict and control the final shape of the part.
Sink Marks
As thin sections cool rapidly, they shrink more quickly than the surrounding thicker sections. This differential shrinkage can cause the thicker sections to pull away from the thinner sections, creating depressions or “sink marks” on the surface of the part. These sink marks can be visually unappealing and may also affect the part’s functionality.
Gate Design
Proper gate design is crucial for ensuring the complete and even filling of thin-walled sections. The location, size, and shape of the gate can significantly impact material flow, pressure distribution, and the overall quality of the part. Optimizing gate design requires careful consideration of factors such as part geometry, material properties, and processing conditions.
Ejection Challenges
Ejecting thin-walled parts from the mold can be challenging due to their delicate nature. The thin walls can be easily deformed or damaged during ejection, especially if the ejection forces are not carefully controlled. Specialized ejection systems, such as low-force ejectors or pneumatic systems, may be necessary to minimize part damage.
Is Low-Pressure Die Casting a Good Fit for Thin Wall Parts?
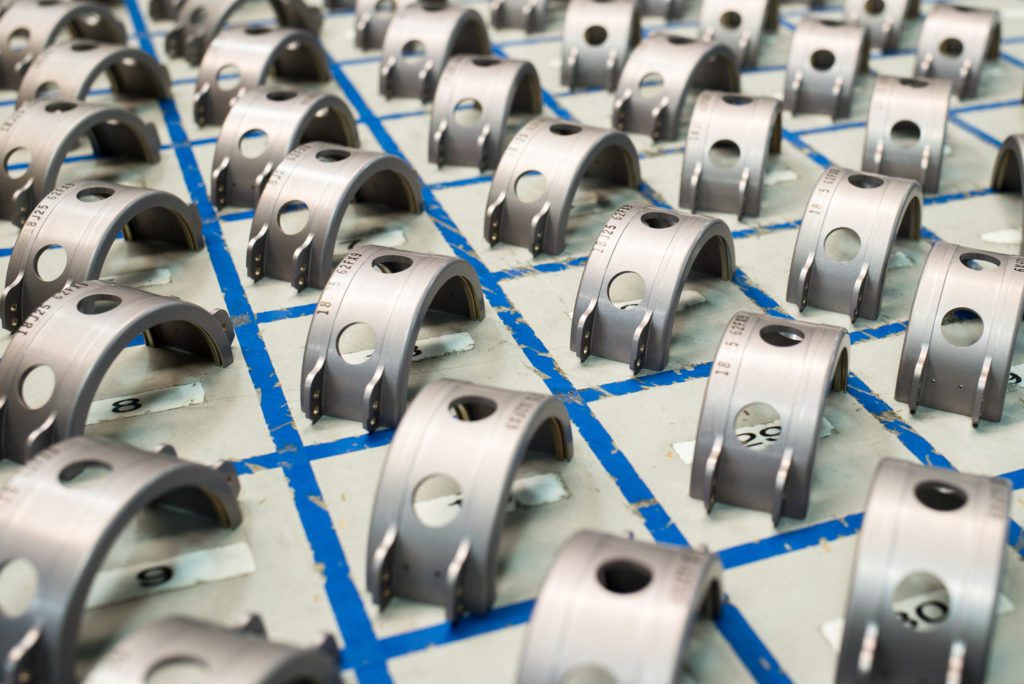
Now, let’s address the central question of this article: Is low-pressure die casting a good fit for thin wall parts? The short answer is no, low-pressure die casting is generally not well-suited for producing parts with very thin walls. There are several limitations to the technique.
Limitations of Low–pressure die casting
Because of the limitations in low-pressure die casting, you end up facing some crucial issues in the process. These include –
Limited Ability to Fill Very Thin Sections
Firstly, the relatively low pressure used in LPDC may not be sufficient to completely fill extremely thin sections, especially those within the 1-5mm range.
You will have issues with the lack of force in the molten metal. It won’t be able to overcome the surface tension and flow into the narrowest areas of the mold cavity. This eventually leads to problems like incomplete filling, voids, and potential defects.
Potential for Warping and Distortion
As we discussed above, warping and distortion are very common struggles in manufacturing thin wall parts. Although LPDC minimizes turbulence, the slower filling process can still lead to some degree of uneven cooling.
This unevenness immensely contributes to warping and distortion, particularly in parts with complex geometries or significant variations in wall thickness.
Along with that, the slower cooling can increase the risk of internal stresses developing within the part, which can lead to deformation after ejection.
Slower Production Rates
The low-pressure injection process inherently results in slower filling times compared to high-pressure die casting. This leads to longer cycle times and lower production rates. While it’s not inherently a major issue, you may still struggle to produce parts in high-volumes.
How to deal with the limitations of low-pressure die casting?
Now, if you are persistent about using low-pressure die casting for producing thin wall parts, then there are some strategies you can try out. These can help you bypass the issues to some extent and get some decent results. They are as follows –
Mold Design Optimization
Optimizing the mold design of your low-pressure die casting can be a useful strategy for low-pressure die casting thin wall parts. Here’s what you can do –
- Employ multiple, smaller gates to distribute molten metal evenly and minimize air entrapment. Carefully locate gates to avoid weld lines and ensure complete filling.
- Design cooling channels precisely to extract heat efficiently, promoting uniform cooling and minimizing thermal stresses. Consider using conformal cooling channels for more even heat dissipation.
- Ensure proper venting to allow air to escape the mold cavity, preventing air entrapment and ensuring complete and even filling of thin sections.
Material Selection
You can increase the success rate of your project even before it begins with strategic material selection. To do that, you have to –
- Select alloys with low viscosity which improves their flowability, enabling them to fill thin sections more effectively.
- Choose materials with low solidification shrinkage so that they minimize the risk of distortion and dimensional inaccuracies.
Process Optimization
During the low-pressure die-casting process, you can implement some key optimization strategies. For instance, you can –
- Slightly reduce the injection pressure to minimize turbulence and improve material flow into thin sections while maintaining sufficient pressure for complete filling.
- Implement controlled cooling techniques, such as using chillers or thermal insulation, to regulate the cooling rate and reduce the risk of uneven cooling and distortion.
Specialized Tooling
Last but not least, employing specialized tooling tactics can also help you mitigate the effects of LPDC limitations. You can –
- Utilize specialized inserts within the mold to provide additional support to thin sections, preventing deformation during ejection.
- Employ low-force ejection systems or pneumatic systems to minimize the risk of damaging thin-walled parts during ejection.
What are the benefits of low-pressure die casting for thin wall parts?
Here’s the thing: Low-pressure die casting may not be the best fit for thin wall parts, but it still comes with some key advantages. These advantages are inherent to this manufacturing technique. The benefits you get include –
Reduced Porosity
The slow and controlled filling of the mold under low pressure minimizes the risk of turbulence and air entrapment, leading to significantly reduced porosity in the final part. This is crucial for thin-wall parts, as porosity can weaken the structure and compromise its integrity.
Improved Material Flow
The gentle and steady flow of molten metal under low pressure allows for better filling of intricate and thin-walled sections. This reduces the likelihood of incomplete filling, cold shuts, and misruns, ensuring consistent wall thickness and minimizing defects.
Enhanced Dimensional Accuracy
The controlled solidification process under low pressure promotes more uniform cooling and reduced shrinkage, resulting in improved dimensional accuracy and tighter tolerances. This is particularly important for thin-wall parts where even small deviations in dimensions can affect their functionality.
Improved Surface Finish
The slower filling rate and reduced turbulence in LPDC contribute to a smoother surface finish on the cast parts. This can minimize the need for extensive post-processing operations, such as machining or grinding, which can be challenging and costly for thin-wall components.
Versatility
LPDC can be used to cast a wide range of metals, including aluminum, magnesium, and copper alloys, making it suitable for various applications and material requirements.
Conclusion
In conclusion, low-pressure die casting is not the ideal choice, but it can still get the job done in some cases. With the inherent benefits of the technique, you can ensure decent quality thin wall parts using the strategies we discussed. That way you won’t have to look for other methods to produce thin wall parts.
However, if you want the most value out of your thin wall parts, then high-pressure die casting can be a great solution for you. Check out why high-pressure die casting is a good fit for thin wall parts in this detailed discussion.
Great, Together