In recent times many people have moved towards semi-solid casting for producing aerospace parts. They consider it to be one of the best techniques to use for the aerospace industry. But why is semi-solid casting a good fit for the aerospace industry? And what makes it so good for the aerospace parts?
To find that out, we explored the semi-solid casting technique for the aerospace industry. Here we will share our findings and tell you the reasons that make semi-solid casting a great option for manufacturing in the aerospace industry. So, if you are interested in the technique, make sure to go through the complete guide.
Overview of Semi-solid Casting
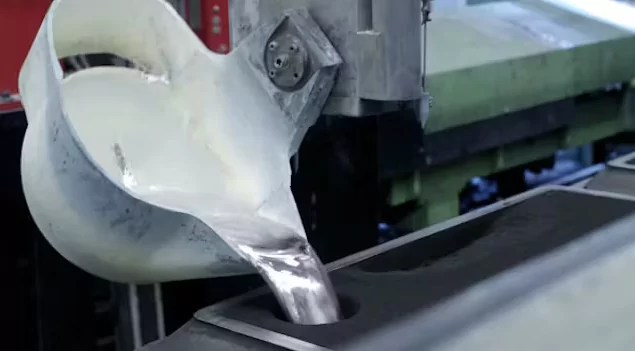
Semi-solid casting, or semi-solid metal processing or thixocasting, is an innovative metal forming technique bridging the gap between conventional casting and forging processes. The method involves working with metal alloys in a semi-solid state, where the material exhibits both solid and liquid properties.
This unique state is achieved by carefully controlling the temperature of the alloy to maintain it between its liquidus and solidus temperatures. In this “mushy” zone, the material behaves thixotropically – it flows when sheared but maintains its shape when at rest.
How it Works
Understanding the semi-solid casting process is crucial if you’re considering implementing this technology in your aerospace manufacturing operations. Here’s a step-by-step breakdown of how semi-solid casting works:
- Material Preparation: The process begins with the selection of an appropriate alloy. Common choices in aerospace applications include aluminum and magnesium alloys.
- Heating: The alloy is heated to a temperature between its solidus and liquidus points. This is typically achieved using induction heating for precise temperature control.
- Thixotropic State: As the material reaches the semi-solid state, it develops a unique microstructure consisting of solid globules suspended in a liquid matrix. This is the key to thixotropic behaviour.
- Shearing: The semi-solid material is then subjected to shearing forces. This can be done through various methods, including mechanical stirring or electromagnetic stirring.
- Injection: The sheared semi-solid material is quickly injected into a die cavity. The speed and pressure of injection are carefully controlled to maintain the desired microstructure.
- Solidification: Once in the die, the material solidifies rapidly under high pressure. This results in a near-net-shape component with minimal shrinkage and porosity.
- Ejection and Finishing: After solidification, the part is ejected from the die and undergoes any necessary finishing operations.
The entire process happens quickly, often in a matter of seconds, allowing for high-volume production of complex parts with excellent dimensional accuracy and mechanical properties.
Applications
Semi-solid casting has found its way into numerous aerospace applications, thanks to its ability to produce complex, high-performance components. Here are some key areas where you might consider implementing this technology:
- Structural Components: Semi-solid casting is ideal for producing lightweight yet strong structural elements such as wing spars, fuselage frames, and bulkheads.
- Engine Components: The process can be used to manufacture various engine parts, including turbine blades, compressor housings, and fuel system components.
- Landing Gear Parts: The high strength-to-weight ratio of semi-solid cast parts makes them suitable for landing gear components like strut housings and actuator brackets.
- Avionics Housings: The excellent surface finish and dimensional accuracy of semi-solid casting make it a good choice for avionics enclosures and heat sinks.
- Satellite Components: In the space sector, semi-solid casting is used for satellite structural components and propulsion system parts.
- Unmanned Aerial Vehicles (UAVs): The lightweight nature of semi-solid cast parts is particularly beneficial for UAV frames and components.
- Hydraulic and Pneumatic System Components: Valve bodies, pump housings, and other fluid system components can be effectively produced using this method.
Materials
When it comes to semi-solid casting for aerospace applications, material selection is crucial. The choice of alloy can significantly impact the properties of your final component and its suitability for specific aerospace applications. Here are some of the most commonly used materials in semi-solid casting for aerospace:
Aluminum Alloys
These are by far the most widely used materials in semi-solid casting for aerospace. Key advantages include:
- Low density, making them ideal for weight-sensitive applications
- Good corrosion resistance
- Excellent thermal and electrical conductivity
- High strength-to-weight ratio
Common aluminum alloys used in semi-solid casting include:
- A356 and A357: Known for their excellent castability and good mechanical properties
- 7075: Offers high strength and is often used in structural applications
- 2024: Provides a good balance of strength and fatigue resistance
Magnesium Alloys
These are gaining popularity due to their extremely low density. Benefits include:
- The lowest density of all structural metals
- High specific strength
- Good damping characteristics
Commonly used magnesium alloys in semi-solid casting include:
- AZ91: Offers a good balance of castability, strength, and ductility
- AM60: Known for its excellent ductility and impact strength
Titanium Alloys
While less common due to their high melting point, titanium alloys are sometimes used in semi-solid casting for high-performance aerospace applications. Advantages include:
- Exceptional strength-to-weight ratio
- Excellent corrosion resistance
- High-temperature capability
Ti-6Al-4V is the most commonly used titanium alloy in aerospace semi-solid casting.
Copper Alloys
You won’t notice the use of copper alloys that much. These are occasionally used for specific applications due to their unique qualities such as –
- Excellent thermal and electrical conductivity
- Good corrosion resistance
- Antimicrobial properties
Surface Finishes
When it comes to semi-solid casting for aerospace applications, the quality and variety of available surface finishes are key advantages of this manufacturing process.
As an aerospace manufacturer, you’ll find that semi-solid casting offers a range of surface finish options that can meet the stringent requirements of the industry. Let’s explore the types of surface finishes available and their characteristics:
As-Cast Finish
The as-cast finish in semi-solid casting is superior to traditional die casting due to the lower turbulence during mould filling and the thixotropic nature of the material. You’ll find that many components can be used directly with this finish, reducing the need for post-processing.
- Roughness (Ra): Typically 0.8 to 3.2 μm
- Characteristics: Smooth, with minimal porosity
- Applications: Suitable for many non-critical surfaces or as a base for further finishing
Polished Finish
Polishing can significantly enhance the smoothness of semi-solid cast parts. The dense, low-porosity surface resulting from the semi-solid process responds well to polishing techniques, allowing you to achieve mirror-like finishes when required.
- Roughness (Ra): Can achieve 0.1 to 0.4 μm
- Process: Mechanical polishing or electropolishing
- Applications: Critical sealing surfaces, aerodynamic surfaces, optical component housings
Textured Finish
Textured finishes can be directly incorporated into the die design, allowing you to produce parts with specific surface characteristics without additional processing steps.
- Patterns: Can include fine grains, stipples, or custom designs
- Process: Achieved through textured die surfaces or post-casting processes
- Applications: Non-slip surfaces, aesthetic purposes, light diffusion
Machined Finish
While semi-solid casting produces near-net-shape parts, some surfaces may require machining for the highest precision. The consistent microstructure of semi-solid cast parts allows for excellent machinability.
- Precision: Can achieve tolerances of ±0.025 mm or better
- Process: CNC machining of specific surfaces post-casting
- Applications: Critical mating surfaces, high-precision components
Anodized Finish
The high-quality surface of semi-solid cast aluminum parts provides an excellent base for anodizing processes, allowing you to achieve consistent and durable anodized finishes.
- Types: Type I (Chromic), Type II (Sulfuric), Type III (Hard Anodizing)
- Thickness: 5-25 μm for Type II, up to 100 μm for Type III
- Applications: Corrosion resistance, wear resistance, electrical insulation, aesthetic purposes
Chemical Conversion Coatings
These thin, protective coatings can be uniformly applied to semi-solid cast parts due to their low porosity and consistent surface quality.
- Types: Chromate conversion, phosphate conversion
- Thickness: Typically 0.5 to 5 μm
- Applications: Corrosion protection, paint adhesion promotion
Painted Finish
The smooth, low-porosity surface of semi-solid cast parts provides an excellent base for paint adhesion, allowing for high-quality, durable paint finishes.
- Types: Powder coating, wet painting
- Thickness: Varies based on application, typically 25-100 μm
- Applications: Corrosion protection, aesthetic purposes, camouflage
Plated Finish
The uniform surface and low porosity of semi-solid cast parts allow for consistent and adherent plated finishes.
- Types: Electroplating (e.g., nickel, chrome, copper), electroless plating
- Thickness: Typically 5-50 μm, but can vary widely
- Applications: Wear resistance, corrosion protection, electrical conductivity, aesthetic purposes
Is Semi-solid Casting a Good Fit for the Aerospace Industry?
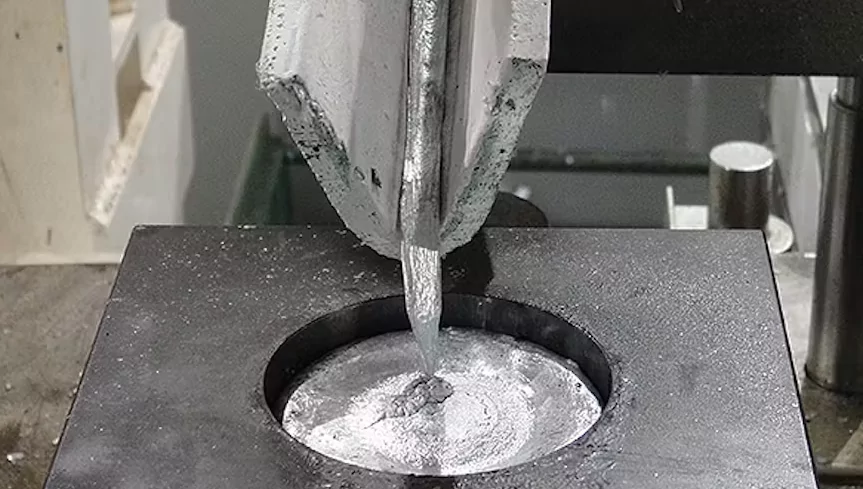
The short answer is yes, semi-solid casting is an excellent fit for the aerospace industry. This technique comes with some exceptional benefits that make it an effective choice for manufacturing aerospace industry parts. These include –
- Enhanced Mechanical Properties
The semi-solid state during casting results in components with improved strength and ductility compared to traditional casting methods.
- Weight Reduction
By allowing for thinner walls and more complex geometries, semi-solid casting helps you achieve significant weight reductions in aerospace components.
- Dimensional Accuracy
The process provides excellent dimensional control, crucial for the tight tolerances required in aerospace applications.
- Reduced Porosity
Semi-solid casting significantly reduces porosity issues, enhancing the structural integrity of the components you produce.
- Cost-Effectiveness
While initial setup costs may be higher, the process offers long-term cost savings through reduced material waste and improved production efficiency.
Why is Semi-solid Casting a Good Fit for the Aerospace Industry?
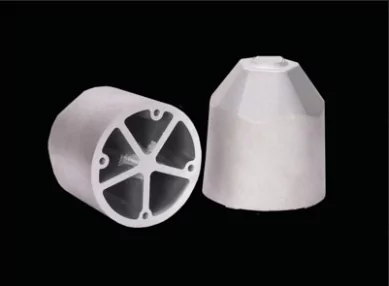
Now that you know the benefits of using semi-solid casting for the aerospace industry, let’s get a bit more technical with this. Below we will talk about the practical reasons that make semi-solid casting a perfect choice for the aerospace industry.
Meeting Stringent Safety Standards
Aerospace components must meet extremely high safety standards. The improved mechanical properties and reduced defects in semi-solid cast parts can help you consistently meet or exceed these standards.
Fuel Efficiency Improvements
By enabling the production of lighter components, semi-solid casting contributes directly to improving fuel efficiency in aircraft. This aligns with the industry’s ongoing efforts to reduce fuel consumption and environmental impact.
Performance in Extreme Conditions
Aerospace components often operate in extreme conditions of temperature, pressure, and stress. The enhanced material properties achieved through semi-solid casting can provide better performance and longevity in these challenging environments.
Design Freedom
The ability to create complex geometries allows you to optimize designs for aerodynamics, heat dissipation, or structural efficiency without the limitations imposed by traditional manufacturing methods.
Quality Consistency
The highly controlled nature of the semi-solid casting process results in more consistent part quality from batch to batch. This consistency is crucial in aerospace manufacturing, where reliability and repeatability are paramount.
Reduced Assembly Requirements
By enabling the production of more complex, integrated components, semi-solid casting can help you reduce the number of parts in an assembly. This not only saves weight but can also improve reliability by reducing the number of potential failure points.
Improved Fatigue Resistance
The fine-grained microstructure and reduced porosity of semi-solid cast parts often translate to improved fatigue resistance. This is particularly important for components subject to cyclic loading, such as engine parts or structural elements.
Corrosion Resistance
The dense, low-porosity surface of semi-solid cast parts can provide enhanced corrosion resistance, which is crucial for many aerospace applications, especially in marine environments.
Thermal Management
For components that require efficient heat dissipation, such as electronics housings or engine parts, the ability to create complex internal channels or fin structures through semi-solid casting can significantly improve thermal management.
Rapid Prototyping and Development
The near-net-shape capabilities of semi-solid casting can accelerate your prototyping and development cycles, allowing for faster iteration and time-to-market for new aerospace technologies.
Conclusion
Summing it up, now you know why semi-solid casting is a good fit for aerospace parts. While the technique in itself suits lightweight parts, there are plenty of other advantages like proper thermal management, maintaining industry standards, corrosion resistance capabilities and so on.
If you choose to go with the technique, you need to make sure you are going with the right service provider or manufacturer for these parts. One of the best options you can pick is Zintilon, as they are one of the most expert manufacturers of aerospace parts. You can never go wrong with them.
Great, Together