Fasteners are essential mechanical devices in manufacturing and metal parts fabrication, particularly in assembling and securing various objects. This hardware helps join different parts together, creating a secure connection. They help simplify the manufacture of complex structures and assemblies by joining different parts without compromising the structural integrity, durability, and functionality of each component.
This guide explores the different types of fasteners, their applications, material options and suitable surface finishes that enhance their performance. In addition, we discussed intricate details to consider before selecting the right fastener types for your fabrication needs.
What is a Fastener?
A fastener is a hardware that joins or secures two or more objects together. Fasteners are essential in metal parts fabrication, as they play a critical role in ensuring structural integrity and efficient part assembly. This mechanical device comes in various forms and sizes, such as screws, bolts, nuts, rivets, and pins, offering specific applications to part fabrications.
However, fasteners’ primary advantage is that they aid in the easy assembly and disassembly of large and complex structures by joining various individual parts. They help create a secure mechanical connection as they join different workpieces together.
Different Types of Fasteners
Machinists and OEMs use different types of fasteners to join various workpieces. While some of these fasteners may be used interchangeably for similar purposes, others have more specific uses. This section discusses the different types of fasteners used in manufacturing and parts fabrication.
Screws
Screws are the most common fastener type for securing connections between two metal pieces. This threaded fastener appears like a nail, featuring full body threading with its head coming in different shapes. Unlike many other fastener types, screws can function alone without requiring any other hardware besides a screwdriver that is needed to drive them into the intended hole.
These mechanical fasteners are highly versatile and durable, though they may require the machinist first to tap the hole to create the thread it’ll interlock with to make the joint. However, some screws feature self-tapping or self-threading capabilities, ensuring they require little to no pre-tapping. Screws are suitable for vast applications, including automotive, metalwork, woodwork, and electronics assembly.
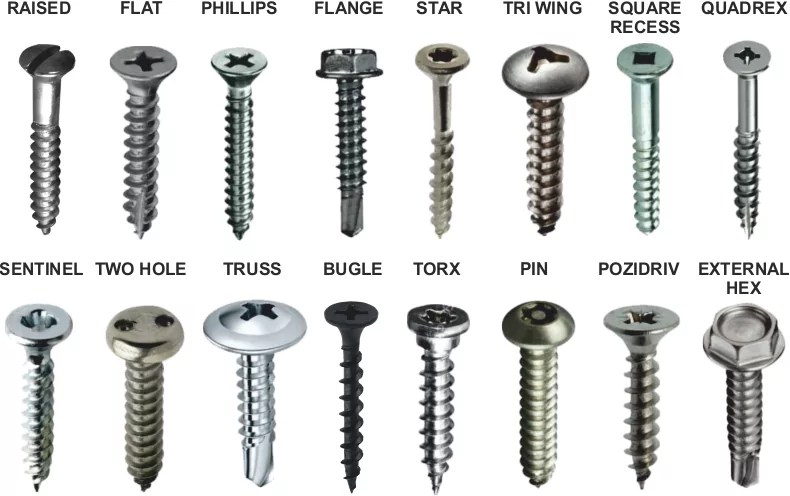
Typical types of screws used in parts fabrication include the following:
- Hex lag screws – suitable for woodworking and heavy-duty applications
- Machine Screws – for joining components of machinery
- Sheet metal screw – for sheet metal fabrications, able to easily penetrate sheet metals.
Bolts
Bolts are another common type of fasteners, similar to screws, as they both possess male external threads at the base. Non-experts may mistakenly refer to bolts as screws and vice versa. However, they are two different faster types, with the main distinction being that bolts require another fastener – nut – to create a secure connection. Also, bolts tend to have a flat or rounded head with no markings on the top, as they do not require a screwdriver.
Bolts are better suited for applications requiring higher strength and load-bearing capabilities, such as assembling large machinery and construction works. Unlike screws, bolts do not require threading of the components they’ll join, as it just interlocks into the nut, securing the part it joins together.
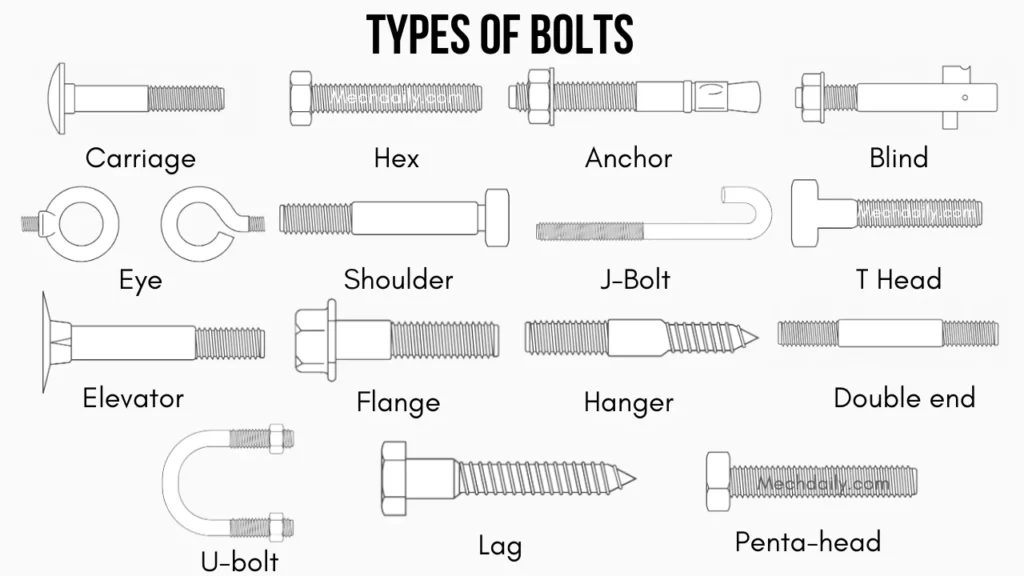
Common examples of bolts used in creating parts include the following:
- Hex-head bolts: feature a hexagonal head that provides easy grip, promoting easy fastening.
- Double-ended bolts: have double-ended threading that can interlock with suitable nuts.
- Carriage head bolts: features a convex-shaped head. They are often used for woodworking applications.
- Eye bolts: have one end with an opening resembling an eye.
Nuts
As mentioned earlier, nuts often act as a pair for a bolt of similar size, shape and thread pattern. It mates with a bolt, or sometimes a screw, as it creates a secure joint holding the parts together. Like bolts, nuts come in different shapes and designs, with the common ones being hex and weld nuts.
- While bolts and screws feature external threading, nuts possess internal threads that help increase torque and create a suitable grip, forming a secure joint with the bolt or screw. Therefore, the bolt and nut fastener system effectively connects two workpieces without any internal threading within them. The machinist just has to ensure a hole in the workpieces and that they are aligned to allow the bolt and nut to link.
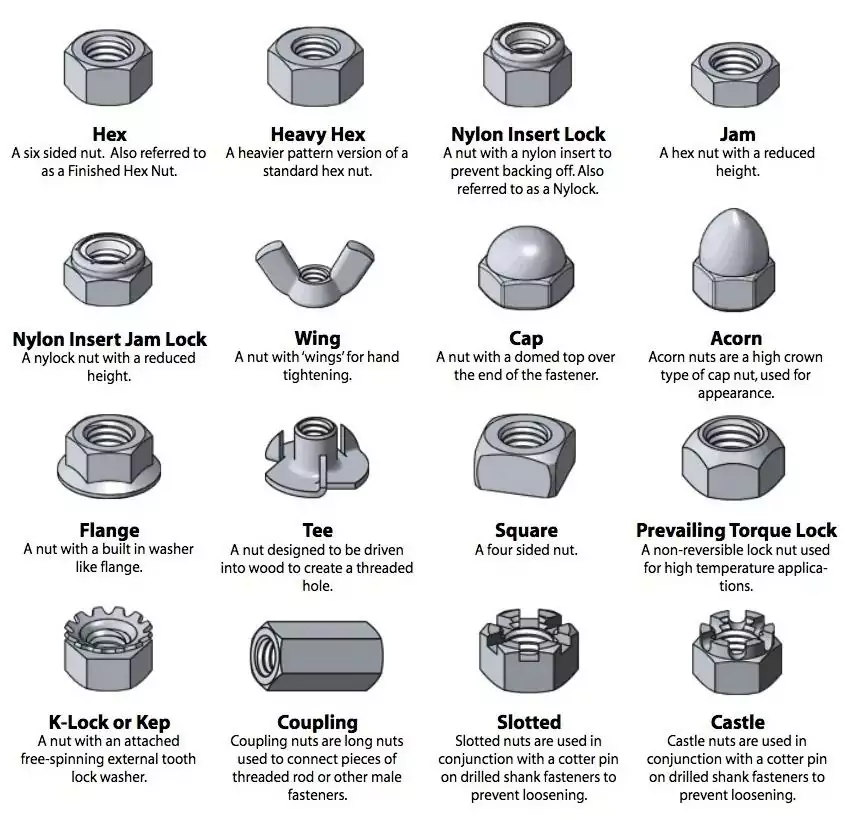
Below are some of the types of nuts used in parts fabrication:
- Hex nuts: hexagonal shaped and suitable for creating a secure connection with hex bolts
- Coupling nuts: These are for fastening areas that are typically challenging to reach.
- Weld nuts: These are used to create a secure link with long threaded bolts.
Rivets
Rivets are permanent fasteners, creating irreversible connections, unlike other fastener types we have discussed thus far. They are the go-to permanent fasteners for automotive and manufacturing purposes. They are lightweight, featuring smooth shafts with no threading. They are cylindrical, resembling bolts and screws, featuring a distinct head and a tail. However, they join materials together through the deformation of their end, creating a secure connection.
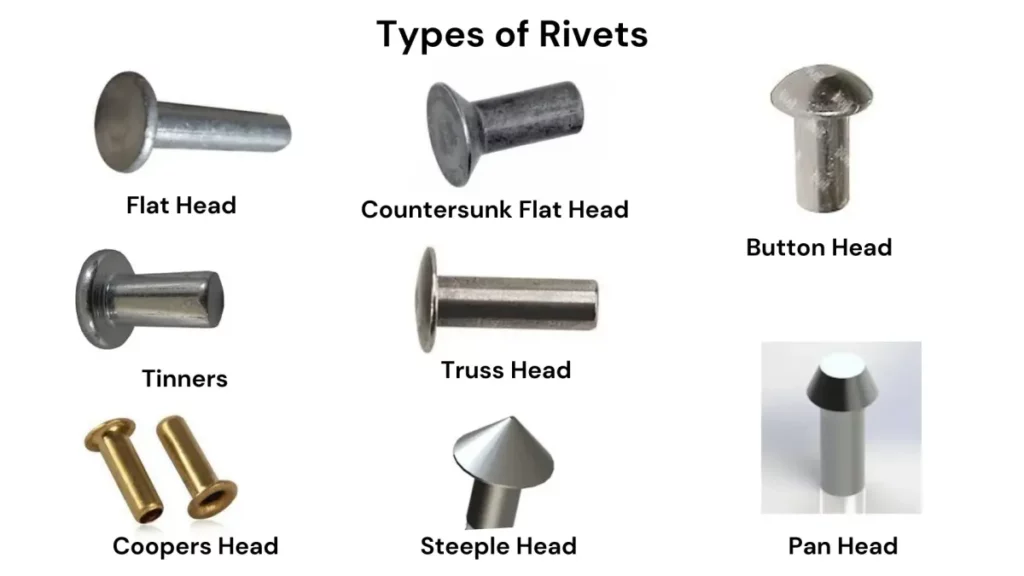
Standard rivets types include:
- Solid rivets
- Blind rivets
- Tubular rivets, etc.
Washers
Washers are another unique fastener, often used with bolts and nuts to ensure a more even load distribution, preventing damage as they provide a secure link. Washers are thin plates, having a hole in their center to ensure they resemble a disc. They serve as a spacer between the bolts and nuts, as a vibration dampener and reduce friction. In addition, they may help protect the workpieces by preventing direct contact, as other conventional fasteners.
Examples of washers
- Plain washers
- Dock washers
- Flat washers
Other Types of Fasteners
In addition to the more sophisticated fasteners described, there are other fastener types used to create a secure connection between two components.
Nails
Nails are the oldest fastening device used in manufacturing, construction, and household applications. They form the basis of the more sophisticated fasteners, little wonder why bolts and screws look like nails. However, they are easier to use without threading or sophisticated tooling. Instead, nails require shear force, often with a hammer, to drive the nails into the components you intend to join.
Pins
These are cylindrical fasteners for aligning and holding components together. Examples include clevis pins, dowel pins and taper pins. Like washers, pins are supplementary fasteners, often used in combination with other fasteners like screws, bolts, and rivets, where they help ensure proper alignment, positioning, and increased stability during part assembly.
Anchors
These fasteners indicate their name, performing similar functions as ship anchors. They are used to attach objects to weak or easy-to-break materials, such as drywall, ceiling, or concrete. They help create a secure hold, gripping tongue surrounding the environment. They can come with internal threading or external.
Materials Used to Make a Fastener
Fasteners are often manufactured using hard materials, primarily metals and alloys like steel, aluminum, brass, etc. Machinists must ensure that they select a sturdy fastener that matches the intended application of the machined part, as the choice of fastener may also influence its strength, corrosion resistance, and other mechanical properties.
Steel
Steel is the most common fastener material because of its high strength and durability. However, this alloy has different grades, depending on the carbon-to-iron content ratio, altering its physical, mechanical, and chemical properties. Moreover, these features, particularly strength and corrosion resistance, can be enhanced through various surface finishing and heat treatments, further reinforcing their attributes as metal fasteners.
Aluminum
Aluminum is the most common material for metal fabrication because of its lightweight, considerable strength, and versatility. Also, aluminum alloys have good conductive properties and aesthetic appeals, making them suit vast applications, including electronics and fabrications that need good visual appeal. The low density of aluminum makes it an excellent fit for lightweight specifications. Furthemore, OEMs may choose to reinforce the alloy by combining them with other suitable alloys like copper and magnesium to enhance its mechanical features and suitability for specific applications.
Stainless Steel
Compared to carbon steel and other steel alloys, stainless steel contains significantly less carbon and iron, with an increase in different elements like chromium and nickel. Including these materials ensures a more resistant alloy that can withstand corrosion and other harsh environments. Regardless, stainless steel possesses incredible strength, making it a good choice for creating fasters. They ensure to withhold the structural integrity of the parts it joins, ensuring they suit vast applications.
Brass
Brass fasteners are not as common as those of steel and aluminum alloys. However, they also offer excellent corrosion resistance, electrical conductivity, and aesthetic appeal. The combination of these features makes them suitable for decorative and electrical applications. Brass fasteners suit electrical and plumbing due to their malleability and attractive appearance.
Titanium
Like aluminum, titanium fasteners are lightweight, high-strength, and corrosion-resistant. They are also less common but suit challenging applications like aerospace, medical implants, and marine environments because of their unique properties. Titanium alloys offer an exceptional strength-to-weight ratio, making them ideal for lightweight specifications without compromising strength. Moreover, they are biocompatible, making titanium fasteners suitable for creating medical and surgical instruments.
Plastic
The applications of fasteners are not restricted to metals alone. Plastic fabrications require those made of plastic and other suitable polymers. Plastic fasteners are lightweight, non-conductive, and resistant to corrosion and chemicals, making them excellent for applications where metal fasteners may not be ideal. They are commonly used in electronics, where their insulating properties are vital. They also suit other applications like automotive and fabrication of consumer goods industries due to their low cost and versatility.
Standard Surface Finishes for Fasteners
Generally, most fasteners utilize materials with excellent mechanical, physical, and chemical properties. However, poor handling and exposure to harsh environments may hamper some of these features, reducing their effectiveness and durability. Therefore, we recommend that machinists apply appropriate surface finishing to enhance the overall performance of fasteners, reinforcing the connection between the parts they join.
Below, we discuss some of the standard surface finishes for fasteners.
Zinc Plating
Coating metal fasteners with a zinc layer use the process of galvanization, which significantly increases the oxidative resistance of these fasteners while enhancing their aesthetics. This surface finish suits fasteners like bolts, nuts, and screws used in automotive, aerospace, general manufacturing, and marine applications.
Nickel Coating
Nickel is one of the constituents of stainless steel that elevates its corrosion resistance more than carbon steel. Therefore, like zinc coating, nickel coating can help improve the chemical properties of the fasteners, making them more durable and enhancing their visual appearance.
Black Oxide Coating
Coating fasteners with black oxide increases their lubricity, making them more adhesive to paints. The application of paints can then further increase the fastener’s corrosion resistance. The finish gives the fastener a decorative black finish, making the entire product more aesthetic.
Anodizing
This is a chemical process that coats the surface of the fastener with an oxide of the metal, such as coating aluminum screws or bolts with aluminum oxide. The oxide coatings are usually more corrosion-resistant and durable. Also, anodizing allows different color options, allowing for beautification purposes.
How to Choose the Right Type of Fastener
As we have discussed earlier, there are different types of fasteners for manufacturing purposes. However, how can you know which is the best fit for your project? This section discusses factors that require consideration, allowing you to select the most appropriate type.
Intended Application
The first criterion before selecting a fastener is its intended application, particularly strength indication. This also includes juxtaposing the fastener’s specification with the overall application of the product to prevent choosing a fastener that may compromise the durability of the assembly.
Understanding the demands of the products will allow you to select a fastener type or subtype that best suits the specifications. For example, screws are a better fit than bolts for woodworking applications and use in drywall and electrical appliances. Alternatively, bolts are better for projects with more demanding and load-bearing applications.
Material Type
Another critical factor that requires consideration is the material type. You can’t use plastic fasteners for metal fabrication. Remember, steel-made fasteners are the most common because of their incredible mechanical features and resistance. However, when working with aluminum components, especially with lightweight specifications, it’s best to stick with aluminum fasteners. In addition, stainless steel or titanium fasteners will be better suited for applications in harsh environments, so factors like corrosion or chemical reactions won’t compromise the assembly’s integrity.
Thread Type and Installation Method
The machinist needs to evaluate the installation method and accessibility to ensure the selection of the most appropriate faster type for the intended product. For example, the presence or absence of a threaded hole in the workpiece may determine the type of screw or bolts you select. In fact, when there’s no threading, and the screw you have access to is not self-threading, you may need to stick to bolts and nuts to create a secure joint.
Also, concerning threading, coarse threads often ensure rapid parts assembly, suggesting that under fine one takes longer. However, finer threads mean more interaction with the parts or nuts, as in bolts, ensuring a more secure lock and connection.
Aesthetics
The aesthetics and visual appearance of the fastener are also essential criteria to consider, particularly for applications that require good aesthetic appeal. These include furniture, consumer electronics and architectural installations. The machinist must ensure selecting a good enough fastener that will further enhance the product’s visual appeal.
Other factors to consider when selecting fasteners include cost and availability. Machinists should ensure that they select a fastener that will not overshoot the total manufacturing cost while also choosing one that will be readily available.
Zintilon: Your Partner for Parts Machining and Fabrication Service
Are you looking for a reputable partner for your parts fabrication and machining projects? Look no further. At Zintilon, we specialize in CNC machining and related technologies, including sheet metal fabrication, rapid prototyping, etc. Whether it is a project with a simple design or parts with complex geometries, do not hesitate to contact us today!
Conclusion
Selecting a suitable fastener is essential to achieving a secure, durable, and efficient manufacturing and parts fabrication assembly. Each fastener has unique advantages and applications. Therefore, machinists and OEMs must understand the various types of fasteners to identify the one that best suits the project. Material compatibility and aesthetics must be considered to ensure optimal results and product durability.
Great, Together