Just like any other welding technique, you have to deal with a fair share of problems and defects with spot welding as well. However, the good part is that you can easily solve and avoid these defects with the right strategies and approaches.
To help you out with that, we have prepared this detailed guide. Here we will tell you what are the common defects in spot welding and how to avoid them. Once you are done with this guide, you can confidently get flawless spot welding results in every project. Let’s get started.
Spot Welding Defects and Their Solutions
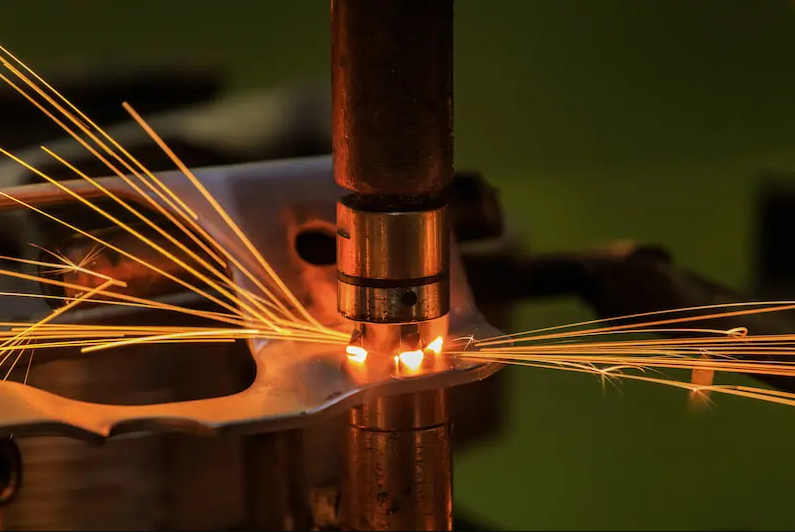
There are several different spot welding defects that you have to know about. The most common ones that you may need to deal with include –
Splattering
Metal spatter during spot welding occurs when molten metal is forcefully ejected from the weld nugget during the welding process. This issue typically results from excessive heat input, inadequate electrode force, or contaminated surfaces.
Spatter not only affects the appearance of your finished product but can also compromise the structural integrity of the weld and damage surrounding components.
How to prevent it?
To prevent splattering, you need to optimize your welding parameters carefully.
- Start by ensuring proper electrode force is maintained throughout the weld cycle.
- Adjust your weld current and time settings to achieve adequate heat without exceeding the material’s thermal limits.
- Clean your workpieces thoroughly before welding to remove any oils, oxides, or contaminants that could interfere with the process.
- Consider using anti-spatter coatings on your electrodes and implementing proper cooling systems.
Indentations or Cracks in the Metal
Indentations and cracks typically appear when excessive force is applied during the welding process or when the material experiences rapid cooling rates.
These defects can manifest as surface depressions, visible cracks around the weld nugget, or internal fractures that may not be immediately visible. Such imperfections can significantly reduce the joint’s strength and durability.
How to prevent it?
To address these issues, you should carefully balance your electrode force and welding parameters.
- If deep indentations are present, start by reducing the electrode force while ensuring it remains sufficient to maintain proper contact.
- Proper pre-heating procedures should be implemented for materials prone to cracking, and stepped or pulsed current profiles should be considered to control heat input and cooling rates.
- Regularly inspecting and maintaining electrode tips will also help maintain consistent pressure distribution.
Asymmetrical Spot Weld Marks
Asymmetrical weld marks occur when the heat distribution during welding is uneven, resulting in irregular or off-center weld nuggets.
This defect often stems from misaligned electrodes, uneven electrode wear, or inconsistent material thickness between the workpieces. Asymmetrical welds can reduce joint strength and cause poor aesthetic appearance.
How to prevent it?
The solution lies in maintaining proper electrode alignment and condition in your spot welder.
- Implement regular electrode maintenance schedules, including dressing or replacing worn tips.
- Ensure your welding equipment is properly calibrated and aligned, and verify that your workpiece positioning system maintains consistent alignment throughout the welding process.
- Consider using electrode positioning guides or automated alignment systems for critical applications.
False Welds
False welds appear normal on the surface but lack proper fusion between the metal sheets. This dangerous defect occurs when insufficient heat or pressure is applied during welding, resulting in weak or non-existent bonding. Surface adhesion might be present, giving the appearance of a good weld, but the joint lacks structural integrity.
How to solve it?
Proper quality control measures should be implemented to prevent false welds, including regular destructive and non-destructive testing of sample welds.
- Optimize your welding parameters through systematic testing, ensuring adequate current flow and electrode force.
- Monitor your equipment’s performance regularly, checking for signs of power fluctuations or pressure system issues.
- Consider implementing real-time monitoring systems that can detect false welds during production.
Liquid Metal Embrittlement
Liquid metal embrittlement (LME) occurs when liquid metal penetrates the grain boundaries of the base material, causing severe cracking and brittleness.
This phenomenon is particularly common when welding galvanized steels, where the zinc coating can interact with the base metal at high temperatures. LME can significantly compromise the structural integrity of your welded joints.
How to prevent it?
To combat LME, focus on controlling your welding parameters to minimize zinc vaporization.
- Implement proper ventilation systems to remove zinc vapors from the welding area.
- Consider using specialized electrode materials and coatings designed for welding galvanized materials.
- Adjust your welding schedule to include pre-pulse heating cycles to help manage zinc coating behavior during welding.
Electrode Degradation
Electrode degradation manifests as progressive deterioration of the electrode tips, leading to inconsistent weld quality and increased defect rates.
This wear occurs naturally during welding but can be accelerated by improper cooling, excessive current, or contaminated workpieces. Degraded electrodes often result in larger weld spots, reduced current density, and inconsistent heat distribution.
How to prevent it?
Address electrode degradation through comprehensive maintenance programs.
- Implement regular electrode dressing schedules based on your production volume and material types.
- Use proper cooling systems to maintain optimal electrode temperature during operation.
- Consider implementing automated electrode wear monitoring systems and establish clear criteria for electrode replacement based on wear patterns and weld quality metrics.
Identifying Poor Weld Strength and Its Causes
Poor weld strength remains one of the most critical concerns in spot welding operations as it directly impacts product safety and reliability. When you’re evaluating weld strength, you need to consider multiple factors that could contribute to weakness in your joints.
How to identify poor weld strength?
The primary indicators of poor weld strength include undersized nuggets, which fail to provide adequate fusion between materials, and irregular nugget formation, resulting in inconsistent joint properties. You might notice these issues through visual inspection, but more often, they require systematic identification testing.
To effectively identify and address poor weld strength, implement these key practices:
- Conduct regular destructive testing through peel or chisel tests
- Perform metallurgical analysis of weld cross-sections to evaluate nugget formation
- Monitor and record key welding parameters, including current, force, and time
- Use ultrasonic testing for non-destructive evaluation of weld quality
- Maintain detailed records of weld quality metrics to identify trends and potential issues
Causes of poor weld strength
Now, let’s get a look at the causes of poor weld strength.
- Improper Current Settings: When your welding current is too low, it fails to generate sufficient heat for proper fusion. Conversely, excessive current can lead to material expulsion and weakened joints. You should regularly verify your current settings against material specifications.
- Inadequate Electrode Force: Without proper force, your electrodes can’t maintain consistent contact resistance, leading to variable heat generation and inconsistent nugget formation. Monitor your pressure systems and verify force settings regularly.
- Poor Material Fit-up: Gaps between your workpieces can create paths for current bypass, resulting in weak or incomplete fusion. Ensure proper fixture design and material preparation to maintain consistent contact.
- Material Surface Conditions: Contaminated surfaces, excessive oxidation, or coating variations can interfere with current flow and heat generation. Implement proper cleaning procedures and maintain consistent material specifications.
Preventing Surface Damage During Spot Welding
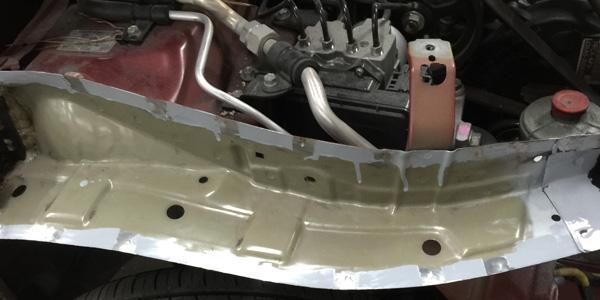
Surface damage during spot welding can significantly impact your product’s aesthetic appeal and corrosion resistance. Understanding and implementing proper preventive measures is crucial for maintaining high-quality finished products.
To effectively prevent surface damage, you need to focus on several key areas. These include
Surface Preparation
- Thoroughly clean all workpieces to remove oils, oxides, and contaminants
- Use appropriate cleaning methods based on material type and surface condition
- Implement proper storage and handling procedures to maintain surface cleanliness
- Consider using protective films or coatings where appropriate
Electrode Management
- Select appropriate electrode materials and geometries for your application
- Maintain regular electrode dressing schedules
- Monitor electrode wear patterns and replace tips before they cause surface damage.
- Use proper cooling techniques to prevent electrode overheating
Process Parameters
- Optimize your welding schedule to minimize heat input while maintaining adequate fusion.
- Implement stepped or pulsed current profiles to control heat distribution
- Monitor and adjust electrode force to prevent excessive indentation
- Use appropriate hold times to allow proper cooling before electrode release
Additional Preventive Measures
- Install proper ventilation systems to remove metal vapors that could contaminate surfaces.
- Use shielding techniques for sensitive materials
- Implement regular inspection procedures to catch surface damage early
- Document and analyze surface damage patterns to identify systemic issues
Addressing Misalignment Issues in Workpieces
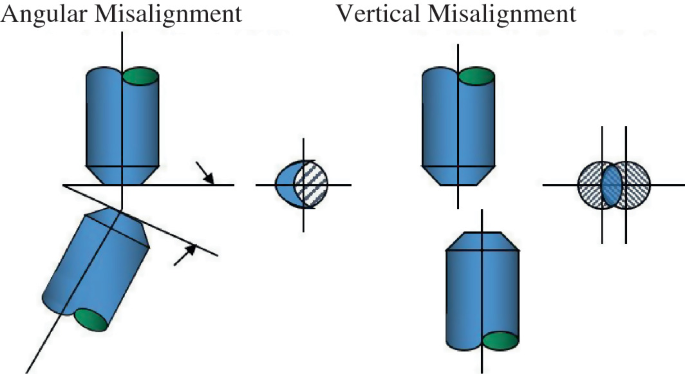
Misalignment during spot welding can lead to numerous quality issues and reduced production efficiency.
Fixture Design and Optimization
Proper fixture design is the foundation for achieving consistent alignment and high-quality welds in spot welding operations. You must focus on creating fixtures with strategically placed locating points and robust clamping mechanisms that securely hold your workpieces in position throughout the welding process.
When designing your fixtures, incorporate adjustment features that can accommodate material thickness and geometry variations, ensuring flexibility without compromising alignment precision.
Equipment Maintenance
Maintaining your welding equipment in optimal condition is essential for preventing misalignment issues. You should establish a comprehensive inspection schedule for electrode holders and positioning systems, ensuring they remain properly calibrated and aligned.
Pay close attention to wear patterns in guide bushings and alignment components, as these can gradually lead to positioning inaccuracies if left unaddressed. Regularly verifying pneumatic or hydraulic positioning systems helps ensure smooth and precise movement during welding operations.
Material Handling Procedures
Effective material handling procedures are critical for maintaining proper alignment throughout welding operations. Develop and implement standardized loading procedures that ensure consistent workpiece positioning, reducing the risk of misalignment during welding.
Invest in comprehensive operator training programs that cover proper material handling techniques and emphasize the importance of precise positioning. Support these procedures with clear visual alignment aids and positioning guides that help operators maintain consistent workpiece placement.
Quality Control Measures
A robust quality control system is essential for identifying and addressing alignment issues before they impact product quality. Establish clear procedures for verifying alignment at various stages of your welding process, using appropriate measurement tools to confirm proper workpiece positioning.
Maintain detailed documentation of any alignment issues encountered and the steps taken to resolve them, creating a valuable reference for future troubleshooting. Regularly analyze your alignment data to identify patterns or trends that might indicate systemic problems.
Best Practices for Ensuring Consistent Weld Quality
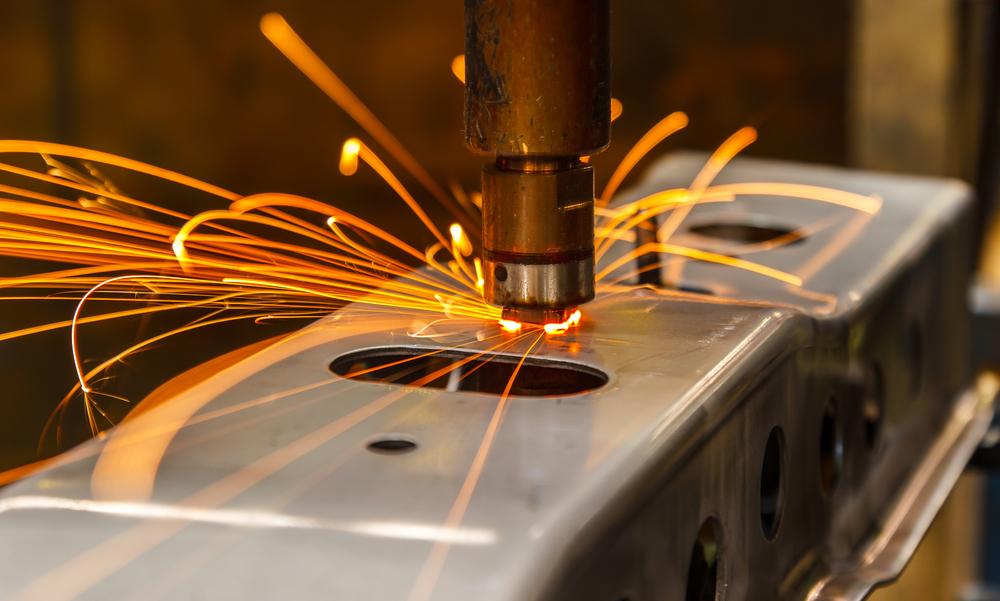
Maintaining consistent weld quality requires a systematic approach to process control and quality assurance. Here are some best practices to ensure consistent weld quality in your projects.
Parameter Documentation and Control
You must maintain detailed documentation of all welding parameters, including current settings, electrode force, and weld timing. Establish a robust system for parameter verification and adjustment.
Equipment Maintenance Protocol
Develop and follow a comprehensive maintenance schedule for all welding equipment. This includes regularly inspecting mechanical components, electrical systems, and cooling circuits.
Material Verification and Handling
Implement strict material verification procedures to ensure consistency in your welding operations. This includes checking material specifications, surface conditions, and coating properties before welding.
Operator Training and Certification
Invest in comprehensive operator training programs covering theoretical and practical knowledge. Develop certification requirements for welding operators and implement regular skill assessments.
Quality Control and Testing
Establish robust quality control procedures, including both destructive and non-destructive testing methods. Implement regular testing schedules and maintain detailed records of test results.
Process Monitoring and Documentation
Implement real-time monitoring systems to track critical welding parameters and detect deviations. Establish procedures for documenting and analyzing process data to identify trends and potential problems.
Environmental Control
Maintain proper control of environmental conditions in your welding area, including temperature, humidity, and air quality. Implement appropriate ventilation systems to remove welding fumes and maintain air quality.
Continuous Improvement Program
Develop a systematic approach to continuous improvement in your welding operations. This includes regularly reviewing quality metrics, process efficiency, and operator feedback.
Conclusion
Summing it up, if you want to achieve the perfect spot welding results, you need to be prepared to deal with the most common defects. Our guide here not only addressed the defects but also provided you with solutions to deal with them.
Now, all you have to do is, follow the tips and strategies, then enjoy flawless spot welding in every project.
Great, Together