La pressofusione ad alta pressione (HPDC) si è affermata come il processo di produzione leader per la produzione di parti metalliche con pareti sottili, elevata precisione dimensionale e finitura superficiale eccezionale.
Questo metodo è ampiamente utilizzato in settori quali automotive, aerospaziale ed elettronica, dove la riduzione del peso, l'integrità strutturale e l'estetica sono fattori critici. Il processo HPDC è particolarmente adatto per produrre componenti con spessori di parete che vanno da 1 mm a 5 mm.
In questo articolo esploreremo perché la pressofusione ad alta pressione è la soluzione ideale per la produzione di componenti con pareti sottili, i principali vantaggi che offre e perché è preferita rispetto ad altre tecniche di produzione.
Panoramica della pressofusione ad alta pressione
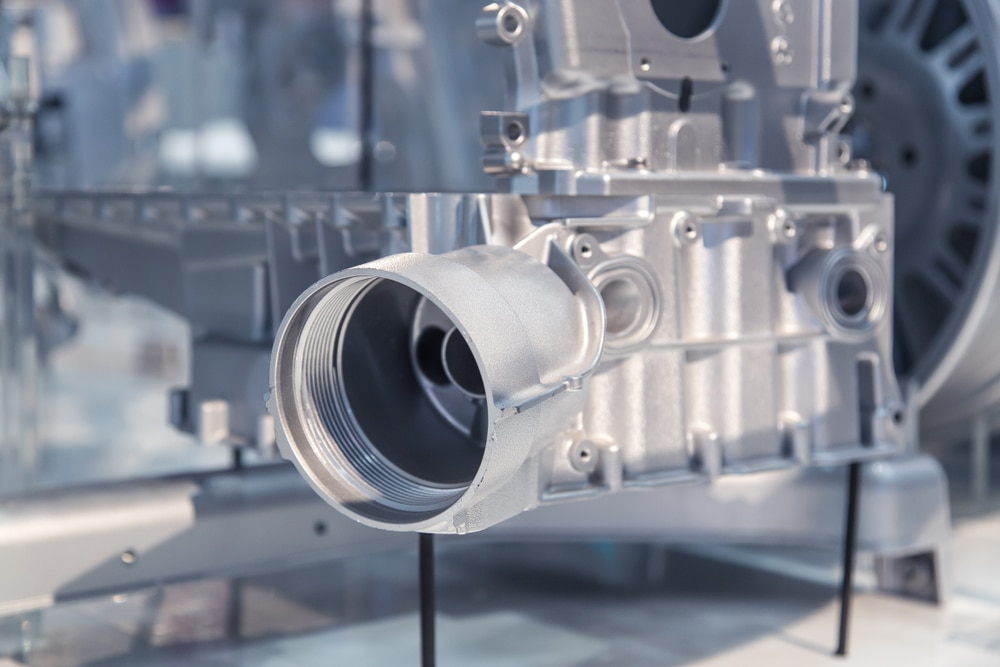
La pressofusione ad alta pressione (HPDC) è un processo di produzione di precisione in cui il metallo fuso viene iniettato in uno stampo metallico ad alta pressione. Questo metodo eccelle nella produzione di componenti complessi e di alta qualità con eccellenti proprietà meccaniche e finiture superficiali.
HPDC è ideale per la produzione ad alto volume grazie alla sua velocità, ripetibilità e stampi in acciaio per utensili riutilizzabili. Consente la creazione di forme complesse che sarebbero difficili o costose con altri metodi.
Il processo supporta varie leghe non ferrose, offrendo flessibilità per requisiti di parti specifiche. I componenti HPDC sono densi, dimensionalmente precisi e durevoli, riducendo al minimo le esigenze di post-elaborazione. La sua efficienza e qualità lo rendono essenziale per settori come automotive, aerospaziale, elettronica e dispositivi medici
Come funziona?
La pressofusione ad alta pressione (HPDC) è un processo di produzione popolare utilizzato per produrre parti metalliche complesse con elevata precisione. Il processo prevede l'iniezione di metallo fuso in uno stampo, o matrice, ad alta pressione, ottenendo componenti con una finitura superficiale liscia e un'eccellente precisione dimensionale. Ecco una panoramica passo dopo passo di come funziona l'HPDC:
- Selezione e preparazione delle materie prime: Il processo inizia selezionando una materia prima adatta, in genere leghe di alluminio, magnesio o zinco, a seconda delle proprietà desiderate della parte finale. Il metallo scelto viene fuso in una fornace fino a raggiungere la temperatura di fusione appropriata, assicurando la coerenza ed evitando la contaminazione.
- Fusione e Trasferimento: Una volta che il metallo raggiunge la temperatura corretta, viene trasferito con cura alla macchina di fusione, dove è pronto per essere iniettato nello stampo.
- Iniezione ad alta pressione: Il metallo fuso viene iniettato nello stampo a pressioni che vanno da 700 a 2000 bar utilizzando un pistone idraulico. L'alta pressione assicura che il metallo riempia ogni cavità e dettaglio, prevenendo difetti come sacche d'aria o porosità.
- Raffreddamento e solidificazione rapidi: Grazie all'effetto di raffreddamento dello stampo metallico, il metallo fuso si solidifica rapidamente, formando un componente denso e resistente.
- Apertura ed espulsione dello stampo; Dopo la solidificazione, lo stampo viene aperto e il getto viene espulso mediante perni di espulsione, completando il ciclo in pochi secondi o minuti.
Applicazioni
La pressofusione ad alta pressione (HPDC) è ampiamente utilizzata in vari settori per la sua precisione, efficienza e capacità di produrre parti complesse.
- Industria automobilistica: L'HPDC è ideale per creare componenti leggeri e resistenti, come blocchi motore e scatole di trasmissione, che contribuiscono a migliorare l'efficienza del carburante e le prestazioni del veicolo.
- Industria elettronica: Il processo viene utilizzato per produrre alloggiamenti e connettori precisi, garantendo prestazioni affidabili e adattamento a complessi assemblaggi elettronici.
- Dissipatori di calore: La tecnologia HPDC è ampiamente utilizzata anche per la produzione di dissipatori di calore, in cui la natura densa delle fusioni garantisce un'efficace dissipazione del calore.
- Settore Aerospaziale: Nel settore aerospaziale, l'HPDC viene utilizzato per creare componenti ad alta resistenza in grado di sopportare condizioni estreme, soddisfacendo rigorosi standard di sicurezza e prestazioni.
- Prodotti di consumo: L'HPDC è preferito per beni di consumo come elettrodomestici e ferramenta, perché consente di produrre componenti esteticamente gradevoli e durevoli, con finiture superficiali lisce.
Materiali
La pressofusione ad alta pressione (HPDC) supporta una gamma di metalli non ferrosi e leghe, ciascuno adatto per applicazioni specifiche:
- Leghe di alluminio: Leggero, resistente alla corrosione e termicamente/elettricamente conduttivo. Ideale per componenti automobilistici ed elettronici.
- Leghe di magnesio: Più leggero dell'alluminio e con elevata rigidità, perfetto per l'industria aerospaziale e per componenti automobilistici leggeri.
- ZnNi, ZnFe, Geomet, Dacromet: Lavorabilità superiore, resistenza all'impatto e precisione. Comune per parti piccole e complesse come ingranaggi e connettori.
- Rame e ottone: Meno comuni a causa dei punti di fusione più elevati e del costo, ma utilizzati per applicazioni specifiche che richiedono le loro proprietà.
La versatilità del materiale accresce l'attrattiva dell'HPDC in tutti i settori industriali.
Finiture superficiali
HPDC fornisce parti con un'eccellente qualità superficiale, eliminando spesso la necessità di ulteriori finiture. Le alte pressioni assicurano superfici lisce con imperfezioni minime. Quando necessario, processi secondari come lucidatura, verniciatura, verniciatura a polvere o anodizzazione possono migliorare l'aspetto e la durata. Queste finiture rendono le parti HPDC adatte sia per usi funzionali che decorativi.
Quali sono le sfide nella produzione di componenti con pareti sottili?
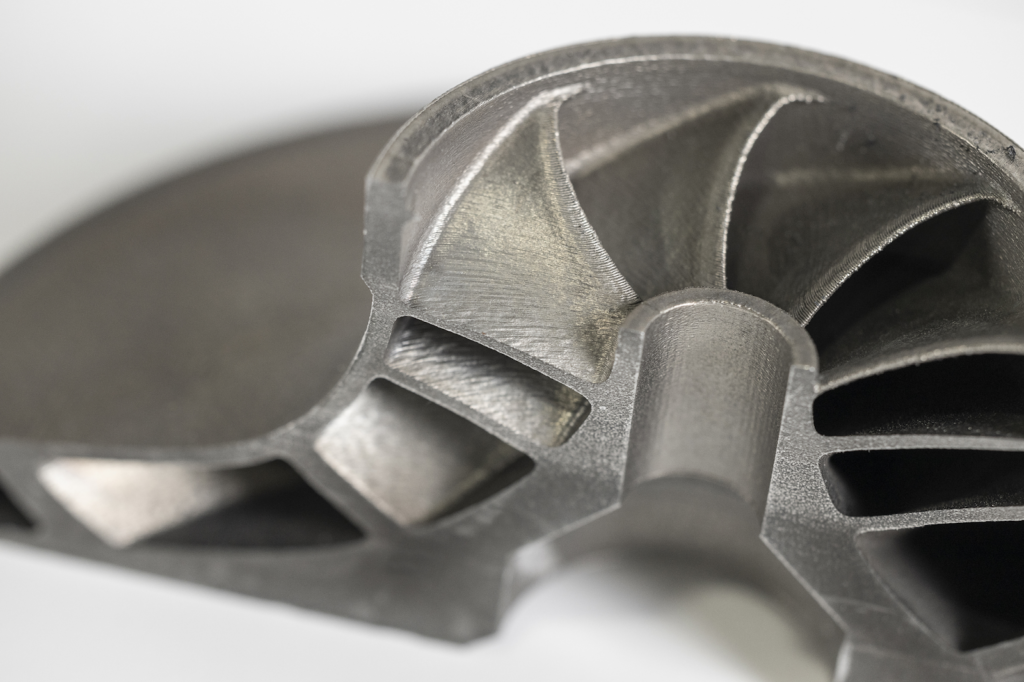
La produzione di parti a parete sottile comporta sfide uniche che richiedono un'attenta considerazione e tecniche avanzate per essere affrontate. Queste sfide derivano principalmente dalla necessità di un controllo preciso sul flusso dei materiali, sulle velocità di raffreddamento e sulla precisione dimensionale, che sono fondamentali per produrre componenti di alta qualità. Di seguito sono riportate le principali sfide associate alla produzione di parti a parete sottile:
Problemi di flusso e riempimento dei materiali
Nella produzione a parete sottile, il metallo fuso deve fluire in sezioni strette e intricate dello stampo senza solidificarsi prematuramente. Ottenere un riempimento completo e uniforme è difficile perché le sezioni sottili si raffreddano rapidamente, aumentando il rischio di difetti come riempimento incompleto, cold shut o porosità. Garantire la giusta pressione di iniezione, velocità e temperatura è fondamentale per superare questi problemi.
Stabilità dimensionale e deformazione
Le pareti sottili sono più suscettibili a deformazioni o deformazioni durante la solidificazione e il raffreddamento. Il rapido raffreddamento in queste sezioni può causare sollecitazioni interne, con conseguenti imprecisioni dimensionali. Il controllo della velocità di raffreddamento e la garanzia di una distribuzione termica uniforme all'interno dello stampo sono essenziali per ridurre al minimo la distorsione.
Complessità della progettazione dello stampo
La creazione di stampi per parti a parete sottile è intrinsecamente più impegnativa a causa della necessità di tolleranze precise e caratteristiche complesse. Una progettazione corretta deve tenere conto del restringimento del materiale, delle sollecitazioni termiche e dello sfiato per evitare difetti e garantire un'elevata ripetibilità.
Aumento del rischio di difetti
Difetti come porosità, crepe o imperfezioni superficiali sono più comuni nelle parti a parete sottile a causa del volume limitato del materiale e delle elevate velocità di raffreddamento. Sono necessarie tecniche avanzate di controllo e ispezione dei processi per rilevare e mitigare tali problemi.
Maggiori richieste di attrezzature
La produzione di parti a parete sottile richiede sistemi di iniezione ad alta pressione, utensili avanzati e controlli di temperatura precisi. Questa attrezzatura è costosa e richiede operatori qualificati, aumentando la complessità e le spese di produzione.
Nonostante queste sfide, la pressofusione ad alta pressione (HPDC) affronta efficacemente molti di questi problemi, rendendola un metodo preferito per la produzione di parti a parete sottile. Scopriamo di più su questo più avanti!
La pressofusione ad alta pressione è adatta per i componenti con pareti sottili?
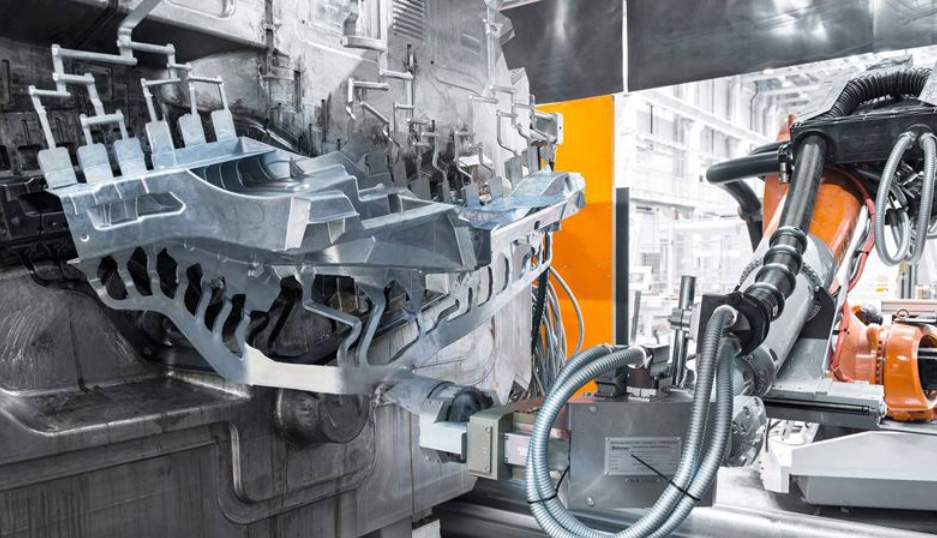
Sì, la pressofusione ad alta pressione (HPDC) è un processo di produzione eccezionale per la produzione di parti a parete sottile, in genere con uno spessore compreso tra 1 mm e 5 mm. Utilizza l'iniezione ad alta pressione per garantire che il metallo fuso scorra senza problemi anche nelle sezioni più sottili dello stampo, creando parti con spessore di parete uniforme e proprietà meccaniche costanti. Ecco perché l'HPDC eccelle in questa applicazione:
Precisione e accuratezza dimensionale
HPDC offre una precisione senza pari, rendendolo ideale per parti che richiedono tolleranze strette e qualità costante. Questa precisione risolve i comuni problemi di produzione di pareti sottili come riempimento incompleto, chiusure a freddo e porosità, garantendo componenti privi di difetti. Con il controllo appropriato di pressione, temperatura e velocità, HPDC elimina le variazioni dimensionali, producendo parti che soddisfano requisiti rigorosi.
Capacità di gestire geometrie complesse
Le parti a parete sottile spesso richiedono design dettagliati con nervature sottili, sottosquadri o angoli acuti. L'HPDC è in grado di gestire queste geometrie complesse mantenendo l'integrità strutturale della parte. Ciò lo rende una scelta affidabile per applicazioni come componenti automobilistici, parti aerospaziali e alloggiamenti elettronici, dove sono essenziali design leggeri ma altamente funzionali.
Alta efficienza produttiva
HPDC offre tempi di ciclo rapidi, consentendo la produzione rapida di grandi volumi di parti a parete sottile con qualità costante. La sua ripetibilità assicura che ogni parte sia identica, riducendo gli sprechi e migliorando l'efficienza. Il processo riduce inoltre al minimo la necessità di lavorazioni o finiture aggiuntive, il che aiuta ad abbassare i costi di produzione.
Spreco di materiale ridotto
A differenza delle tecniche di fusione tradizionali, l'HPDC utilizza in modo efficiente il metallo fuso iniettandolo direttamente nello stampo. Ciò riduce al minimo gli sprechi e qualsiasi materiale in eccesso può spesso essere riciclato. La riduzione degli sprechi non solo fa risparmiare sui costi, ma supporta anche pratiche di produzione sostenibili.
Affrontando sfide come flusso di materiale, deformazioni e difetti, HPDC è una soluzione affidabile ed efficiente per produrre parti sottili leggere, durevoli e complesse in tutti i settori. Che si tratti di automotive, elettronica o aerospaziale, HPDC fornisce risultati costanti e di alta qualità.
Vantaggi della pressofusione ad alta pressione per parti a parete sottile
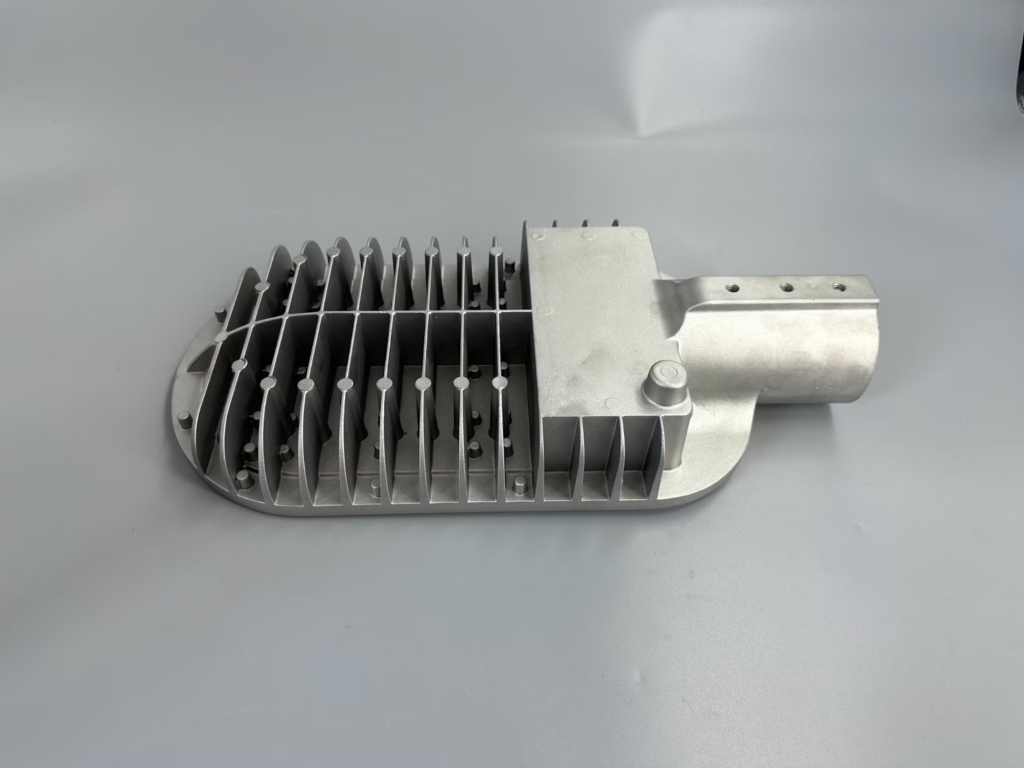
La pressofusione ad alta pressione (HPDC) si distingue come uno dei metodi di produzione più efficaci per la produzione di componenti con pareti sottili, offrendo numerosi vantaggi che la rendono la scelta preferita per un'ampia gamma di settori.
La sua capacità di fornire componenti con eccezionali proprietà meccaniche, dimensioni precise e alta qualità superficiale è particolarmente vantaggiosa per applicazioni in cui la riduzione del peso e le prestazioni sono considerazioni critiche. Le sezioni seguenti evidenziano i motivi principali per cui l'HPDC è una soluzione ideale per la produzione di parti a parete sottile e cosa lo rende superiore ad altre tecniche di fusione e lavorazione.
Rapporto resistenza/peso superiore
Uno dei maggiori punti di forza dell'HPDC risiede nella sua capacità di produrre componenti con un eccellente rapporto resistenza/peso. Quando il metallo fuso viene iniettato nello stampo ad alte pressioni, si solidifica rapidamente, creando una struttura a grana fine che migliora le proprietà meccaniche. Ciò si traduce in parti leggere ma robuste, in grado di sopportare elevate sollecitazioni. Settori come quello automobilistico e aerospaziale apprezzano questa caratteristica per applicazioni che richiedono una riduzione del peso senza compromettere l'integrità strutturale.
Precisione dimensionale e tolleranze eccezionali
L'HPDC è rinomato per la sua precisione. Gli stampi rigidi in acciaio utilizzati in questo processo garantiscono tolleranze strette e variazioni dimensionali minime, anche per componenti con pareti sottili. La precisione dell'HPDC riduce la necessità di lavorazioni secondarie o operazioni di finitura, risparmiando sia tempo che costi di produzione. Settori come i dispositivi medici e l'elettronica, in cui le tolleranze strette sono fondamentali, si affidano all'HPDC per componenti coerenti e di alta qualità.
Capacità per geometrie complesse
HPDC può produrre componenti con forme complesse, come sottosquadri, nervature sottili e caratteristiche interne complesse, difficili o costose da ottenere con altri metodi di produzione. Per le parti a parete sottile, questa capacità consente la creazione di progetti dettagliati mantenendo l'integrità strutturale. Applicazioni come alloggiamenti elettronici e staffe strutturali traggono grandi vantaggi dalla capacità di HPDC di produrre queste geometrie sofisticate con precisione.
Alta efficienza produttiva
HPDC è altamente efficiente, con tempi di ciclo rapidi e la capacità di produrre grandi quantità di componenti rapidamente. La natura automatizzata del processo assicura qualità e ripetibilità costanti in tutte le serie di produzione. Ciò lo rende una scelta ideale per le industrie che operano con tempistiche serrate, consentendo ai produttori di soddisfare grandi ordini e scadenze ravvicinate mantenendo elevati standard di qualità.
Minimo spreco di materiale
Rispetto ad altri metodi di fusione, l'HPDC è altamente efficiente nell'uso dei materiali. Il metallo fuso viene iniettato direttamente nello stampo, riducendo al minimo lo spreco di materiale. Qualsiasi materiale in eccesso può spesso essere riciclato, riducendo i costi e supportando pratiche di produzione sostenibili. Questo vantaggio è particolarmente prezioso per le industrie che mirano a ridurre al minimo l'impatto ambientale ottimizzando al contempo l'uso dei materiali.
Migliore qualità della superficie
HPDC fornisce parti con superfici lisce e prive di difetti. Questa elevata qualità superficiale riduce la necessità di post-elaborazione, riducendo ulteriormente i costi di produzione e i tempi di consegna. Inoltre, la struttura densa delle parti HPDC ne migliora l'aspetto estetico e le rende ideali per applicazioni visibili, come elettronica di consumo o finiture per auto. Le superfici lisce facilitano anche una migliore adesione per rivestimenti o vernici, migliorando la durata e l'aspetto.
Conduttività termica ed elettrica migliorata
La struttura densa e uniforme delle parti HPDC assicura un'eccellente conduttività termica ed elettrica, rendendo il processo ideale per componenti come dissipatori di calore e alloggiamenti elettronici. I design a parete sottile traggono particolare vantaggio da questa proprietà, poiché è possibile produrre componenti leggeri senza sacrificare le prestazioni. Le parti HPDC assicurano una dissipazione termica e prestazioni elettriche ottimali, fondamentali in applicazioni come alloggiamenti LED e involucri motore.
Conclusione
La pressofusione ad alta pressione è un metodo altamente adatto per produrre parti a parete sottile con elevata precisione, eccellenti finiture superficiali e robuste proprietà meccaniche. La sua capacità di creare geometrie complesse e mantenere tolleranze strette lo rende una scelta ideale per settori come quello automobilistico, aerospaziale ed elettronico.
Le aziende che cercano servizi HPDC affidabili possono rivolgersi a Zintilon, un'azienda nota per la sua competenza nella fusione di precisione e per l'impegno nel fornire componenti di alta qualità. Con un team di professionisti qualificati e strutture avanzate, Zintilon fornisce soluzioni HPDC complete personalizzate in base alle esigenze specifiche di ogni cliente, garantendo i migliori risultati possibili per la produzione di parti a parete sottile.
Ottimo, insieme