It is common for people to use the words accuracy and precision interchangeably in everyday conversation. When it comes to machining, these words are not the same and have different meanings. Parts in a batch can be accurate and not precise and vice versa.
Understanding the differences between accuracy and precision makes a lot of difference as it will help in making informed decisions. It will allow one to improve the manufacturing processes and implement effective quality control measures. This article will be your guide on everything precision vs accuracy. It will explain what accuracy and precision mean, how they differ in machining, and how to improve accuracy and precision in manufacturing.
What is Precision in Manufacturing?
Precision is one of the driving forces in modern manufacturing. It describes how consistent two or more measurements are provided that all variables remain the same. It does not necessarily mean that the results must tally with the true value. Precision means getting repeatable measurements and results using the same method.
Furthermore, precision continues to gain relevance as micromachining becomes more popular. These parts are usually small, often with tiny features that are important for functionality and performance. In micromachining, even the slightest error can lead to significant problems.
What is Accuracy in Manufacturing?
Accuracy is another measure of observational error. It refers to how close a measurement is to the specified value. To determine how accurate a part is, one has to compare the difference between the calculated value to that provided in the blueprint. The smaller the value, the higher the accuracy, and vice versa.
Accuracy is important when manufacturing parts that need to be further assembled. Accurate parts ensure proper fit and alignment. This is important in many industries such as electrical and piping. Poor fit and finish can lead to improper connections and leakages respectively.
The Interplay Among Precision, Accuracy, and Tolerance
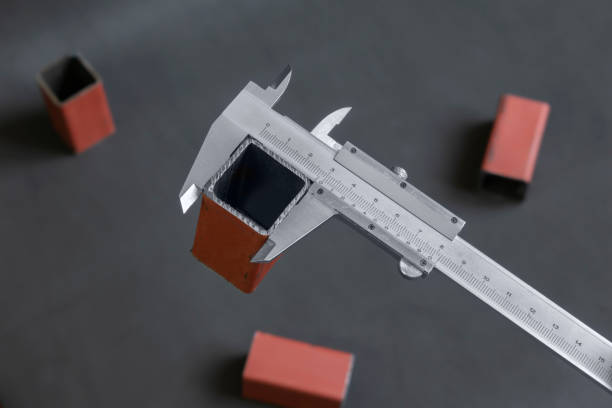
Tolerance, precision, and accuracy are interrelated and they help determine the quality of measurement. Tolerance refers to the permissible variation in the final part dimension in relation to the ideal values. The process of CNC machining cannot be perfect and tolerance specifies how much the results are allowed to deviate from the standard. When a system is accurate and yields a value close to the true one, there is a high probability that it will be within the acceptable tolerance limit. However, a system can give precise results and still fall outside the allowable tolerance range.
When the tolerance limit is not clearly stated, most machinists stick with +/- 0.005 and +/- 0.01 inches for metal and plastic parts respectively. If a dimension of 20.000 inches is stated with a tolerance of +/- 0.005, all metal parts must fall within 19.995 and 20.005 inches. Note that machinists do not always aim to achieve the tightest tolerance possible. When the features on a part are not critical for safety, loose tolerances can be used.
Differences Between Precision and Accuracy in Production Machining
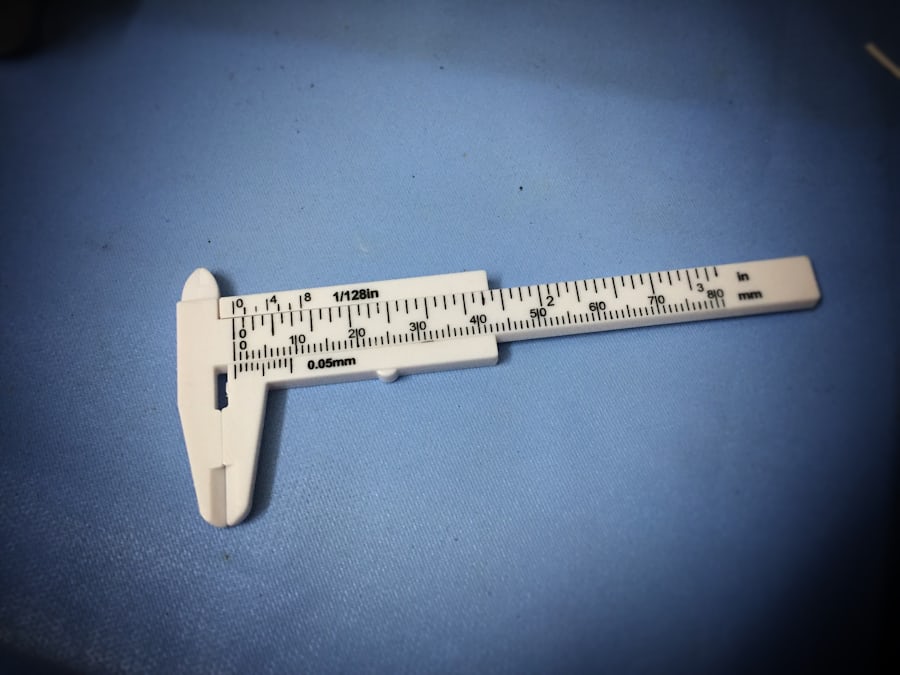
Precision and accuracy are important aspects of production machining. Though they both measure results, they are different in many ways. Understanding the differences between accuracy and precision helps to prevent misinterpretation of quality control data and easily identify areas for improvement. Let’s take a look at the common differences between precision and accuracy in manufacturing
Definition
Precision deals with consistency or repeatability in measurements without necessarily being correct. In manufacturing, it refers to how much the process can continue to produce parts that are of the same dimension each time. However, accuracy is more of correctness. This means that the machined parts must match the CAD model or the digital blueprint. The dimensions of the final components must be close to the specified targets.
Types of Error Indicated
Low precision and low accuracy indicate distinct types of errors. Low precision is a description of random errors as a result of unpredictable events during the machining operation. It can be because of environmental or human factors. Low precision shows that there is a problem with the manufactured products themselves. On the other hand, low accuracy is more involved with systematic errors such as instrument calibration and the metal fabrication process.
Number of Measurements
To determine the level of accuracy and precision, the total number of measurements differs. Precision needs multiple results under the same condition. Experts recommend 3 readings for a more reliable assessment. However, just one measurement is enough to determine how accurate the part is. But, getting more readings will help reduce bias.
Parameters | Precision | Accuracy |
Description | Consistency and repeatability of measurements. | It refers to how correct a reading is. |
Type of Error | Low precision is a result of random errors. | Low accuracy is more involved with systematic errors. |
Problems Indicated | Reflects problems with the manufactured products. | Indicates issues with the process and/or equipment used. |
Number of Measurements | Minimum of 3 readings. | Machining accuracy requires a single measurement for comparison. |
Basis for Improvement | Precision can be improved by carrying out the operation in a controlled environment and reducing human errors. | Accuracy can be improved by using the right machining technology and calibrating the equipment. |
Examples | Five pistons with diameters of 20.00mm, with a true value of 20.00mm. | Five pistons with diameters of 20.01mm, 20.00mm, 19.99mm, 20.00mm, and 20.01mm. |
Table 1: Comparison table showing the differences between accuracy and precision in engineering manufacturing at a glance.
Typical Accuracy Vs Precision Outcomes
Accuracy and precision are the cornerstone of any machining process. They determine how well customers perceive a product and the functionality of a part. Though CNC machining is automated and controls the movement of the tools in predetermined directions, it can still result in varying outcomes such as
- Accurate and precise
- Not precise but accurate
- Not accurate but precise
- Not accurate and not precise
This section will explain these parameters and differentiate between them for better understanding
Accurate and Precise
This is the goal of every manufacturing operation. A product that is accurate and precise functions as expected for end users. For instance, when manufacturing a part that is 1.5 inches high with a tolerance limit of +/- 0.005 inches. If the final parts are 1.500, 1.501, 1.499, and 1.500 inches, then the manufacturing process is both accurate and precise. The dimensions of all the manufactured parts to fall closely between 1.495 and 1.505 inches.
Not Precise but Accurate
Sometimes, parts may be produced accurately and may not be precise. Following the analogy described above, let’s say the dimensions of the final parts are 1.495, 1.504, 1.500, and 1.498 inches. They all fall within the permissible limit but the measurements are inconsistent and vary widely. Quality inspection will indicate that the manufacturing technique used is accurate but not precise.
Not Accurate and Precise
Another scenario one can encounter in manufacturing is having precise but inaccurate products. Still on the previous analogy, if the manufactured parts’ dimensions are 1.508, 1.509, 1.507, and 1.509 inches. All measurements are out of place and not within the tolerance limit. However, they are consistent and very close to one another. In this instance, the machining process is said to be precise but not accurate.
Not Accurate and Not Precise
There can also be both human and process errors which can result in parts that are neither accurate nor precise. For instance, when machining 1.2-inch plastic parts with a tolerance level of 0.01 inches. When the operations go wrong, the machinist can get varying dimensions such as 1.1 inches, 0.9 inches, 1.2 inches, and 1.5 inches. These results show that the parts fall out of the limit and the dimensions are not consistent.
Importance of Accuracy and Precision in Manufacturing
Accuracy and precision play a huge role in many manufacturing industries including medical, oil and gas, automotive, and aerospace. Most components must be fabricated exactly to specifications for them to function well. Accurate parts benefit not only the customers but the company as well. Below are some of the advantages of accuracy and precision in part manufacturing.
Less Waste and Costs
Accuracy and precision reduce variation and ensure that machinists produce products that are exact replicas of the intended design. Inaccurate parts increase the incidence of recalls and reworks which can be costly and can lead to waste if one is not careful. Accurate machining ensures proper use of resources and reduces the number of defective products.
Safety Concerns
Parts in certain industries such as medical and automotive must be accurate to ensure end users’ safety. Accurate and precise medical devices and implants impact patient care and overall health outcomes. Furthermore, auto parts should be designed to meet industries’ standards to ensure passengers’ safety and prevent sudden breakdowns.
Regulatory Compliance
Accurate and precision machining demonstrates compliance with regulatory requirements. The final parts serve as evidence that the quality management system of a company is up to date and standard. Additionally, some regulatory bodies request that certain critical components be inspected and verified before sales and distribution begin.
Customer Satisfaction and Trust
The way customers perceive a product and their experience of using it is important. When a product is manufactured accurately, it tends to perform as intended which increases customer satisfaction. It is also important for the product to deliver the same quality every time a user makes a purchase. This enhances trust and gives room for referrals.
Hitch-free Testing and Prototyping
Precision and accurate machining ensures stress-free testing during the prototyping stage of product development. Accurate prototypes allow for reliable testing of product performance before production begins in full. Inaccuracies can lead to flaws which can be costly and time-consuming to correct.
How To Improve Machining Precision and Accuracy

Getting accurate and precise results when machining is not automatic. One has to put in conscious effort and improve all aspects of the operation. The following are some ways one can improve machining precision and accuracy.
Optimize Machining Parameters
The different machining parameters including cutting speed, feed rate, and spindle speed influence the quality of the final part. The machinist must adequately adjust these parameters based on the material properties and thickness to prevent errors. Using the wrong speed and feed rate will result in incomplete cuts or excessive heat input which impact precision and accuracy.
Proper Calibration and Maintenance
It is important to regularly calibrate and maintain the cutting tools to ensure optimal performance. One must clean the tools routinely, inspect them for damage, and replace them if needed. During routine maintenance, the team must properly lubricate movable parts using appropriate lubrication systems to reduce wear. All these are important to maintain precision during a machining operation.
Workpiece Fixturing
Use appropriate workholding fixtures during machining to improve accuracy and precision. Fixtures are responsible for clamping the workpiece as the cutting tools move over them. Unnecessary vibrations and movements during machining can lead to errors at the cutting edge. Furthermore, fixtures also help to position parts accurately relative to the cutting tool. This feature ensures that the tools are cut at the right location.
Measurement and Inspection
The inspection team must use proper hand metrology tools and coordinate measuring machines to conduct in-process inspections during product development. Hand metrology tools include calipers and micrometers. They are affordable and simple to use. However, many use them for only linear dimensions. On the other hand, coordinate measuring machines are more sophisticated. They provide accurate measurements that can be easily compared with the model.
Improve Environment Control
Though underrated, the condition of the machining environment determines the accuracy and consistency of the final parts. Unstable and changing temperatures may cause unwanted expansion and contraction of the workpiece. This can lead to dimensional inaccuracies. To prevent this, the operator must work in a temperature-controlled environment for a smooth operation.
Consider Advanced Machining Techniques
The use of advanced machining techniques such as 5-axis machining has made it easier to create accurate and repeatable parts. 5-axis CNC machining allows movement along five different directions to fabricate the workpiece on all sides. This helps to reduce frequent adjustment and repositioning of the workpiece. Minimizing manual setup eliminates the possibility of errors during machining.
Zintilon: Your One-stop Shop for Accurate and Precise Products
The level of accuracy and precision you get from an operation depends on the third-party manufacturer you use. Zintilon is a leading one-stop machining service provider worldwide. We provide a comprehensive range of capabilities from DFM analysis and rapid prototyping to product inspection and shipping. By providing access to many services under one roof, you can be sure of reduced errors and improved quality control.
At Zintilon, we use cutting-edge technologies like CNC machining and 3D printing to ensure that parts meet tight tolerances and industry specifications. Our inspection team scrutinizes and inspects parts before shipping them out. Zintilon is ISO certified which shows that we have taken time to prove that our quality management system is up to standard. We continuously improve our manufacturing procedures to reduce variability and ensure consistency in production. Most importantly, our services are affordable and we offer competitive prices. With us, you can get your products to market on time and stay ahead of your competitors.
Conclusion
Precision and accuracy are two distinct words with different meanings. Precision is all about consistency and repeatability. It tells how close two or more parts are. However, accuracy refers to how correct the dimensions of a part are to the blueprint. Both accuracy and precision are important in manufacturing for quality assurance and to improve customer satisfaction. What is accuracy? What is precision? We hope this article has answered all your questions. Feel free to contact us for further questions and inquiries.
FAQs
What is the relationship between accuracy and precision?
Accuracy and precision are related concepts. Parts in a batch may be accurate and not precise and vice versa. Both terms are important in production engineering for safety concerns and to demonstrate compliance with regulatory requirements.
How does in-process quality control impact accuracy and precision?
In-process quality control affects accuracy and precision in many ways. Regular calibration and maintenance of equipment, proper sourcing of raw materials, and inspection and testing affect the accuracy and precision level of parts and components.
How does operator training and skill affect precision and accuracy?
The experience and expertise of the operator affect the outcome of product development. A well-trained operator can properly optimize machining parameters to get the best results. The operator identifies and resolves issues early to prevent downtime and errors.
Great, Together