Welding sheet metal is a critical component of metal fabrication. The welding technique is used to join metal components. There are a significant number of distinct types of welding, which is one of the most prevalent techniques for joining metal objects. Do you know which of the various sheet metal welding techniques is most suitable for your applications?
Sheet metal welding is a multifaceted craft that requires applying numerous techniques. Acquiring the requisite knowledge and skills is imperative to perform welding with optimal outcomes.
This article examines the diverse techniques employed in welding sheet metal materials, including their merits and practical uses. Additionally, it explains the crucial guidelines to remember when welding thin metal sheets for optimal results.
What Is Sheet Metal Welding?
The welding process involves fusing two or more components by applying heat, pressure, or both. As the components chill, they subsequently join. Although welding is most commonly associated with thermoplastics and metals, it can also be applied to wood.

The connected components are referred to as the “parent” material. A ‘filler’ is any substance incorporated to aid in forming the joint; examples include a plate, conduit, filler wire, and electrode. The composition of these fillers frequently resembles that of the primary material. They join in the formation of a uniform weld. Conversely, there are situations where an alternative filler is necessary, such as when working with fragile cast irons.
Common Types of Sheet Metal Welding Process
“How to weld sheet metal” is the most common question that follows. There are a variety of techniques and strategies for welding sheet metal, and each has its own set of applications in specific situations. Let’s have a look at the various sheet metal welding techniques.
MIG Welding
MIG welding (Gas Metal Arc welding) is a widely recognized technique. This method generates a pool of molten wire by employing a solid wire electrode in a welding instrument. This wire is the filler material that facilitates the connection of the metal components. A shielding gas layer is also incorporated into the MIG welding instrument to prevent the molten stream from becoming contaminated by the surrounding atmosphere.
MIG welding is routinely employed in numerous industries, including the automotive and home improvement sectors. The primary reason for this is the combination of cost-effectiveness and efficiency. This technique applies to most common sheet metals (including stainless steel and aluminum). It produces high-quality welds, is relatively inexpensive, and does not require complex equipment.
TIG Welding
This welding technique operates on the principle of arc welding but employs current to conduct the welding operation via a non-consumable tungsten electrode. It employs an inert shielding gas to shield the electrode and prevent atmospheric contamination of the weld. Helium and argon are the most commonly used variations of shielding gas.
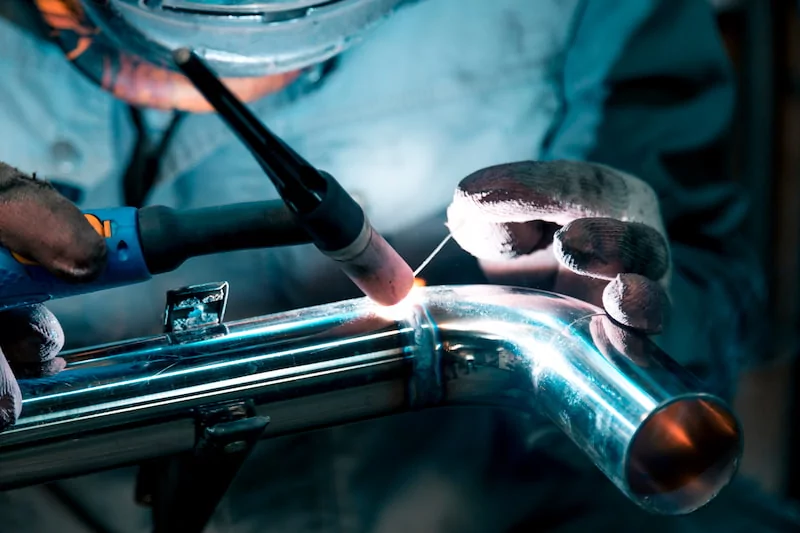
TIG welding is most efficient when working with non-ferrous metals, such as titanium, nickel, magnesium, and aluminum. It is among the most frequently used methods for fabricating frames in feeders, motorcycles, and doors. TIG’s capability to manipulate non-ferrous metals renders it an optimal selection for sectors associated with flight, including aerospace and aviation.
TIG welding affords greater control over the process and produces a more robust weld compared to alternative techniques. However, it also necessitates a higher level of welder proficiency and can occasionally consume more time.
Laser/Electron Beam Welding
Laser and electron beam welding may be the most expensive processes, and their applications are quite limited. A laser or an electron beam is initially employed to generate the necessary heat for the welding process. However, the primary distinction between the two is that their operation necessitates the use of specialized, complex apparatus.
These methods are highly precise, particularly in regard to laser welding. This makes them ideal for fabricating metal components that demand great intricacy. Additionally, they can process more durable metal varieties, including carbon steel, stainless steel, and titanium, without compromising the overall aesthetic appeal of the weld.
Electron beams and lasers can also be applied to more prevalent substances, including thermoplastics and aluminum. However, this may not be the most economical approach.
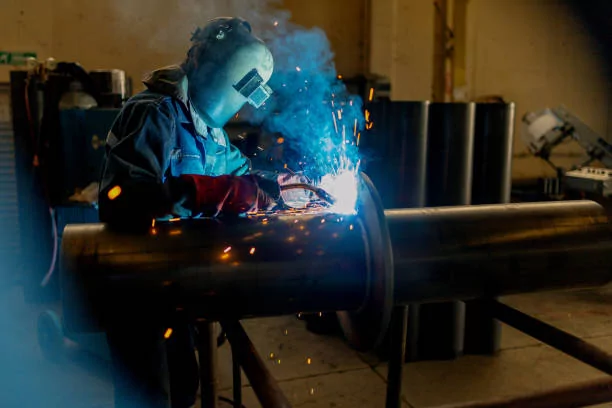
Stick Welding
Stick welding uses a flux-coated stick as the electrode. A significant distinction is that stick welding does not involve the application of any shielding gas. Nevertheless, this does not imply that no alternative method exists to safeguard the weld outcomes against atmospheric contamination. The electrode stick is coated with flux for this purpose.
By disintegrating in response to the heat produced by the welding process, this flux can coat the weld with a layer that safeguards it against unintended disruptions. This technique is essentially a direct substitute for laser welding. It is not as precise and does not produce a particularly attractive weld, but it is efficient and reasonably priced. Industries such as shipbuilding, construction, and general steel fabrication can also benefit from its portability.
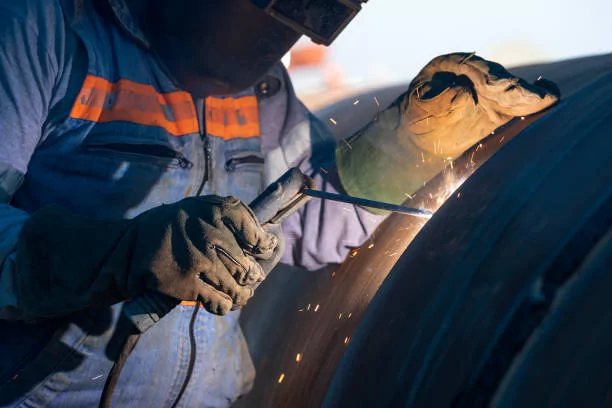
Plasma Arc Welding
This welding process is comparable to the TIG mentioned above welding in that the welding instrument also incorporates a tungsten electrode. However, plasma arc welding employs a reduced arc size and permits the electrode to contact the welding tool’s body. Various metal components can be melted together by generating plasma from pressurized gas.
Plasma arc welding does not necessitate infill materials and produces high-quality welds with minimal post-weld cleanup. Additionally, it is a comparatively quick method that lacks considerable strength and possesses remarkable precision. Thus, it is prevalent in the aerospace and marine industries.
Gas Welding
Another approachable method for joining sections of sheet metal that are molten is by using a gaseous fuel, oxygen, or oxyacetylene to ignite the metal and weld them together. This is one of the more established procedures on the list and a fairly common one in the industry.
It remains one of the most widely used methods in the metalworking industry because of its adaptability and efficacy. Metalworkers use this method for ventilation shafts, pipelines, tubes, air conditioning systems, and more. Gas welding applies to both ferrous and non-ferrous metals, operates without electricity, is portable, reasonably priced, and requires little expertise to operate.
The table below summarizes the advantages and disadvantages of each process:
Welding Technique | Description | Advantages | Disadvantages |
MIG Welding | It uses a solid wire electrode to produce a pool of molten metal. | Efficient, cost-effective, produce high-quality welds | Requires shielding gas, not suitable for thick metals |
TIG Welding | It uses a non-consumable tungsten electrode and an inert shielding gas to produce a precise, high-quality weld. | Excellent control, suitable for non-ferrous metals | Requires more skill than other techniques, slower |
Laser/Electron Beam Welding | It uses a laser or electron beam to generate heat for welding. | Very precise, can weld thick metals | Very expensive, requires specialized equipment |
Stick Welding | It uses a flux-coated stick electrode to produce a weld. | Simple, portable, inexpensive | Not as precise as other techniques, produces a less attractive weld |
Plasma Arc Welding | It uses a small arc and plasma to melt metal together. | Fast, produces high-quality welds | Requires specialized equipment |
Gas Welding | It uses a gaseous fuel to melt metal together. | Versatile, can be used without electricity | Not as precise as other techniques |
What Metals Are Suitable for Sheet Metal Welding?
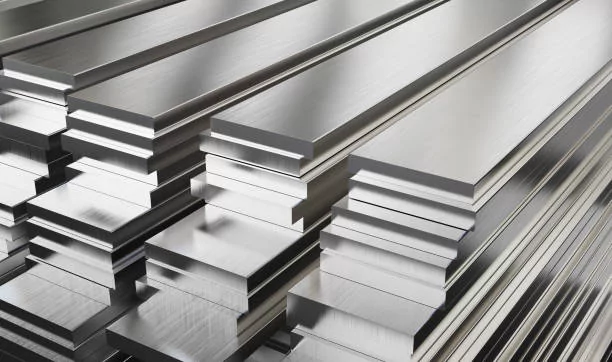
As previously stated, welding is a viable technique for various materials. The most common metals used in the fabrication of sheet metal are the following:
Carbon Steels
Carbon steel is amenable to various welding processes and can be welded using machinery with short or long wavelengths. Due to the minimal material accumulation during laser welding, steel components can be affixed directly to the paint line with minimal to no subsequent cleansing.
Stainless Steels
Additionally, stainless steel is compatible with different forms of welds and machines. A post-weld procedure might be necessary to eliminate thermal tint, depending on the product’s intended use. Regraining and blending are unnecessary when welding stainless steel with a brushed finish.
Aluminum
To weld aluminum efficiently, it is necessary to employ a short wavelength machine due to the reduced amount of light reflected away. Aluminum welding is suitable for both aesthetic and functional purposes.
Copper and Iron
Copper and iron are slightly more difficult to weld due to using distinct classifications for each metal. Success is achieved in copper laser welding by modulating both power and speed. Commonly, both MIG and TIG welding techniques are applied to copper and its alloys. The various grades of cast iron produce welds with different results.
How to Control Distortion in Sheet Metal Welding
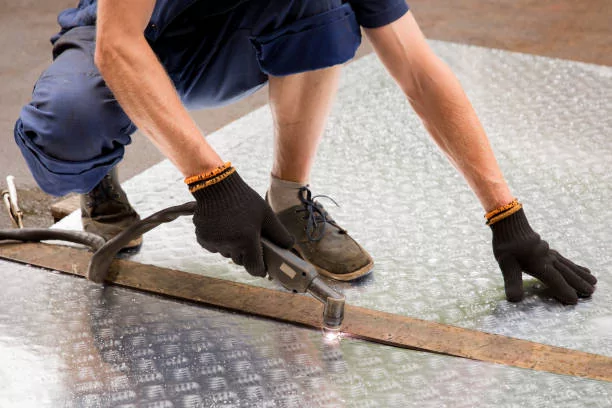
Sheet metal welding may occasionally suffer from distortion. It is possible to decrease weld distortion by adjusting the parameters of the welding procedure and the design. Consequently, the following are some recommended strategies for mitigating weld distortion:
- Weld Sizing: In addition to minimizing distortion, you will save labor and weld material by appropriately sizing a weld.
- Periodic Welding: Opt for intervals over a single lengthy weld.
- Reduced Number of Weld Passes: An attempt should be made to reduce the number of weld passes, as this increases the likelihood of material shrinkage.
- Welding Position: The weld should be made near the sheet metal’s neutral axis or center. The welding setup should be from left to right when welding sheet metal.
- Use Clamps: This is a prevalent method for regulating weld distortion in assemblies and small components. Jigs, clamps, and fixtures assist in securing the components in the desired position.
- Reduce Weld Duration: The likelihood of distortion increases proportionately to the time required to weld a sheet metal panel. Attempt to reduce the duration of the weld, if possible.
How to Prevent Burn Through in Sheet Metal Welding
Burn-through occurs when the welding electrode penetrates deeply enough to reach the weld root. In essence, you may inadvertently melt the entire thickness of the base metal. As a result, the burn-through affects the ultimate weld joint in the form of a hole. This defect occurs frequently on or close to the weld joint.
The following are sheet metal welding strategies and recommendations for preventing burn-through:
- Employ a reduced current level
- Weld more rapidly
- Avoid excessive honing of the base metal margins
- Ensure surface cleaning prior to welding
- Maintain a moderate arc length
- Sustain the correct inclination throughout the entire weld connection
- Prevent superfluous patterns
- If feasible, use low-intensity techniques such as MIG or TIG
- Verify the configuration of the pre-welding equipment configuration verification
Practical Tips for Welding Sheet Metal Materials
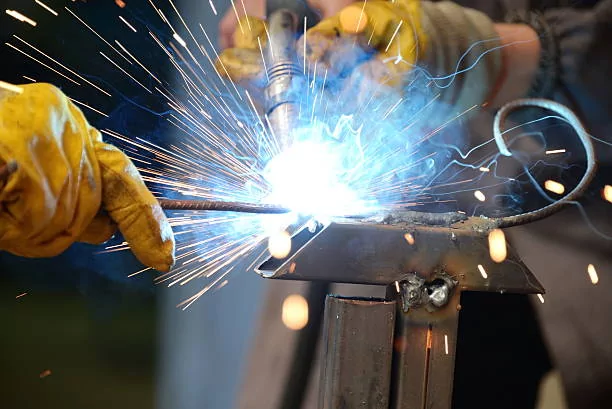
The objective of welding metal sheets is to guarantee that the resulting components retain sufficient mechanical properties to suit their intended use. Consider the following practical tips as you perform welding.
Choose the Right Technique
But each metal requires a different process, and we must choose the proper one. We must decide how to do the work. Metal sheet welding surfaces and best practices are listed below.
- Flat Surfaces: A successful weld on a flat surface requires the welder to fix the tip angle at 45 degrees to the surface of the metal and precisely point the flame at the connecting spot. TIG and MIG welding work best on flat surfaces. Flat setups work well for wire feed and gas flows.
- Horizontal Surfaces: In the horizontal arrangement, metal sheets seem horizontal to welders. In fillet welding, the top end of a horizontal surface is welded to a vertical surface. The joint looks like two metal pieces perpendicular to each other in a ‘L’ shape. Stick welding suits horizontal surfaces where TIG and MIG welding are hard to balance.
- Vertical Surfaces: Welding causes molten metal to flow down and pile up. The welder must control metal flow. This requires holding the electrode between the weld pool and flame and pointing the welding gun 45 degrees to the plate. The optimum technique for these surfaces is stick welding. Welders often aim to flatten or horizontalize the weld axis for convenience.
- Overhead Surfaces: Overhead welding is the hardest. The name implies welding a workpiece above your head. Molten metal falls off when welding. Reduce the weld puddle to make overhead welding easier. Use enough filler for a good weld. Stick welding is best for this setup. Custom sheet metal fabrication shops rarely weld overhanging surfaces.
Carry Out a Test Run
Conducting a pilot run on the metal prior to commencing welding is advisable. Many variables can influence the quality of a weld. Therefore, process optimization is essential for achieving the best results. This includes ensuring that your instruments are clean and dry and using the appropriate amperage and voltage. By doing so, you will acquire a prototype of your product, irrespective of its current stage of development.
Select the Correct Filler Metals
It is critical to use an infill metal whose mechanical properties correspond to those of the sheet metal fabrication. For the sheet metal to be thinner, the infill must be thinner. For instance, when welding a 1mm thin metal, the optimal infill diameter is 0.6 mm.
A thinner wire can be melted with a reduced amount of heat. Thus, there is a reduced likelihood of excessive heat accumulation and an increased probability of achieving optimal results from the weld. Additionally, selecting the proper filler metal will decrease the likelihood of rusting, splitting, and other potential flaws.
Use a Shielding Gas
A protective gas is of the utmost importance in determining the weld’s appearance. Choose shielding gases containing a greater concentration of argon for use in welding parameters. The optimal composition is 75% argon gas and 25% carbon dioxide. The welding spatter will be reduced because argon conducts significantly less heat than carbon dioxide.
Use Small Electrode and Wire Diameter
Employ an electrode measuring no more than one-eighth of an inch. One can generate a more constricted arc by using a smaller electrode, thereby diminishing burn-through and enabling a more compact dimension.
When welding, the material being used must be taken into account. For instance, when welding aluminum, a distinct gauge of wire is required compared to when welding steel. Additionally, your expertise level should be considered when selecting the proper wire size. Consider using a small wire when beginning to weld, as this may assist you in mastering the process. With experienced practice, one will develop a greater ease in handling larger diameters.
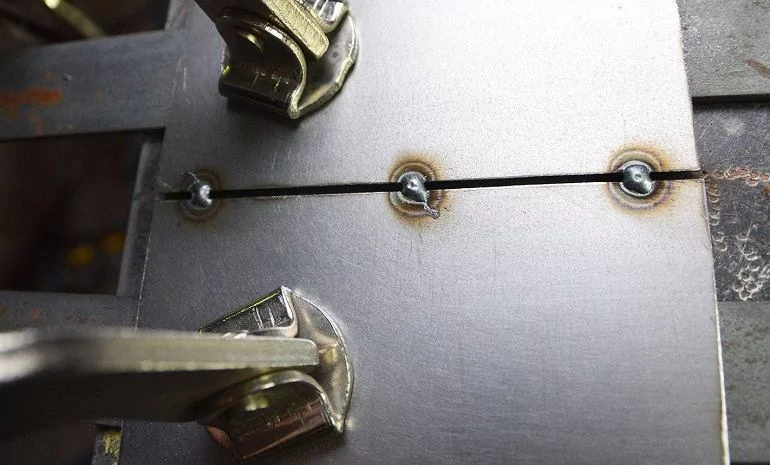
Use Tack Welding for Thin Metal Sheets
Tack welding is an exceptional technique for connecting thin steel sheets. Tacks are extremely minute welds that do not result in any surface harm to the material. When joining two metal sections, a 1mm gap must be maintained between them. A tack is then positioned precisely in the center of the opening. After placing the tack, apply substantial pressure to both surfaces of the tack until it completely dissolves. The molten solder will adhere to the metal and create a robust bond.
Try the Skip Welding Technique
The method referred to as “skip welding” involves strategically placing a number of short welds or stitches to secure the position of the thin metal sheet. By employing skip welding, metal distortion and deformation can be reduced.
Adjust Heat Used Appropriately
In the context of sheet metal welding, heat is the most influential variable. An excessive amount of heat will dissolve the metal, failing the joint. To prevent this from occurring, various forms of heating are employed according to the metal type.
To produce a weld of superior quality, gas tungsten arc welding (GTAW) is employed when working with denser materials such as steel. When welding thinner materials such as aluminum, stick welding is used because it permits the weld to be positioned at any angle. In addition, it’s best to use a torch that directs heat to the electrode wire’s point rather than its base. This concentrates the heat precisely where the weld must occur.
Zintilon Sheet Metal Fabrication Capabilities
Welding sheet metal is an essential procedure for creating a wide range of products. Due to the vast number of welding practices and techniques, it is essential to understand every aspect of the procedure. Nonetheless, you can entrust the task to experts.
Do you require superior welding services for custom sheet metal fabrication? Zintilon is here to meet your precise needs. We excel in various services, including laser cutting, welding, and other related technologies. Zintilon delivers professional and outstanding sheet metal services. Additionally, we ensure prompt lead times and competitive pricing without compromising quality. Simply submit your design files and receive a quote.
Great, Together