The automotive chassis is responsible for the attachment and specifications of car components such as the engine, suspension, and steering mechanism. There are different types of car chassis and they determine the type of vehicle and its performance.
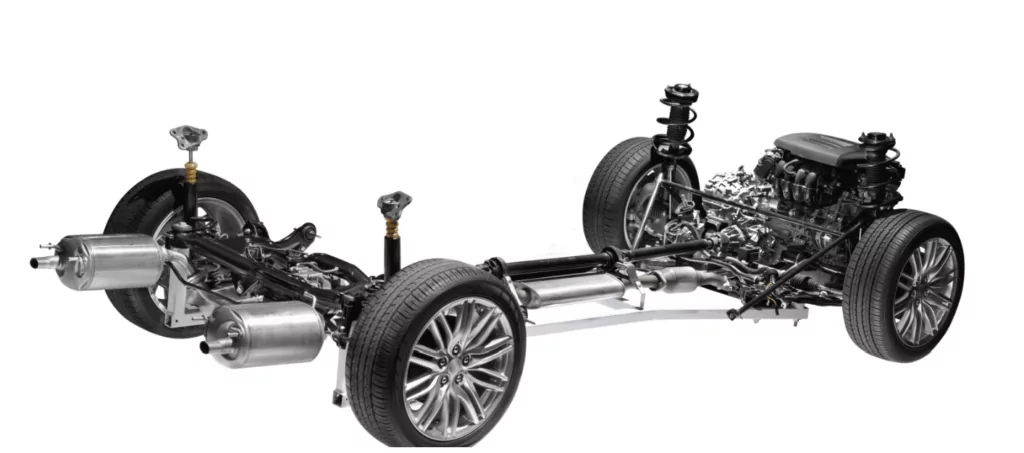
Without a chassis, a vehicle cannot support the weight. As a result of this and its other influences, businesses should be well versed in the automotive part for an efficient automotive chassis design process. This article discussed the automotive structure and its common design trends so businesses can make more informed decisions.
What is an Automotive Car Chassis?
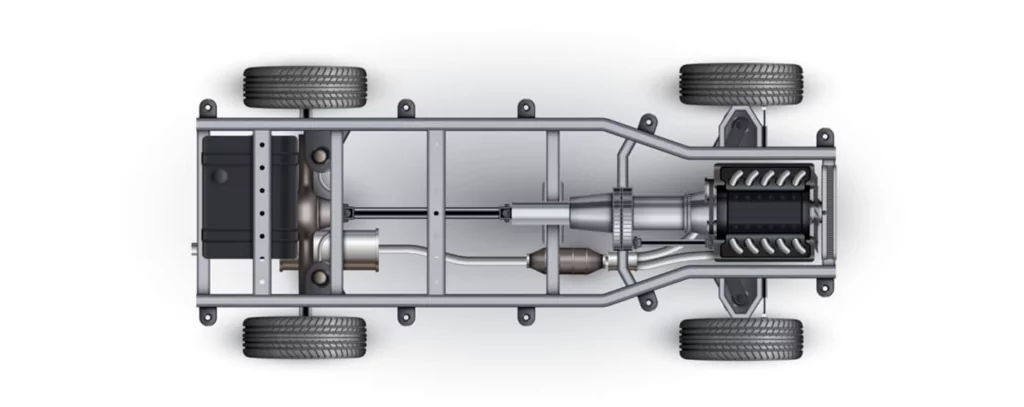
The car chassis is the car’s backbone acting as the load-bearing part of the car frame and is the minimum requirement for a vehicle to move from one point to another.
All mechanical automotive components for example the steering system, suspension system, fuel tank, radiator, brakes, wheels, engine, and transmission system are fastened to the car chassis..
Functions of an Automotive Chassis
The chassis of a car is responsible for the following:
Vehicle structural integrity
The chassis supports the vehicle, providing the structural framework that determines the collapse or deformation of the vehicle in a collision.
Point of attachment for other components
It is the attachment point for auto components like the steering system and suspension system and its rigidity ensures proper alignment and mounting.
It helps in weight distribution
The car chassis bears and distributes the vehicle’s load between the front and rear axles making the car stable or easier to handle.
Structure of Automotive Car Chassis
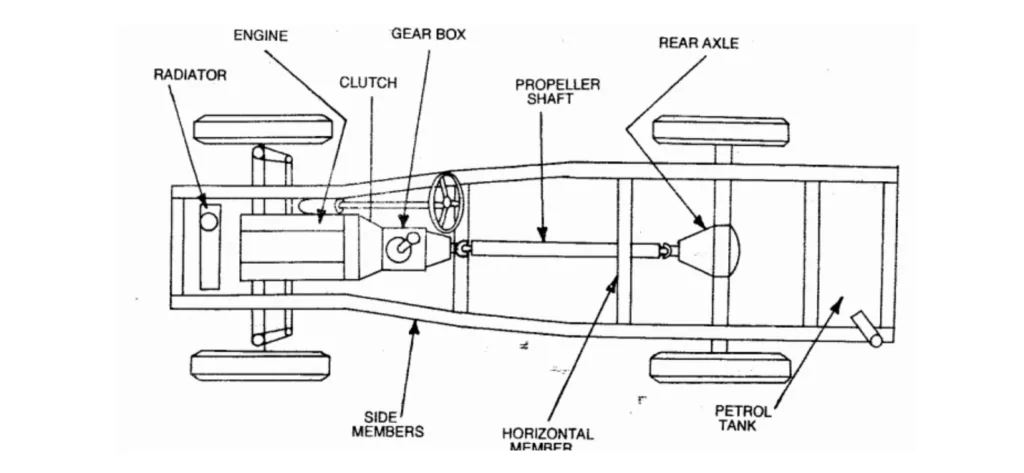
Automotive chassis come in different designs but a conventional car chassis diagram will contain the following structure, kit, and components.
Frame Rails
A frame rail is a steel or aluminum longitudinal beam responsible for the chassis load-bearing ability. There are several designs responsible for the different types of car chassis. For example, ladder car chassis have two frame rails.
Crossmember
A crossmember is a horizontal beam that connects the frame rails increasing the chassis rigidity and its functions as a load-bearing structure for other auto components.
Clutch
The clutch is a main car chassis part connected to the engine crankshaft and disconnects the speed from the car gearbox.
Transmission system/gearbox
The gearbox or transmission system is another critical chassis responsible for a vehicle’s ability to move from one point to another. It transmits the engine speed to the car wheel and controls its performance at different speeds.
Universal Joint
The universal joint is a little connector behind the transmission and front axle, connecting the torsional moments from any direction and angle. It is used in the drive shaft to transfer energy from the engine to the wheels.
Rear Axle
The rear axle is a live chassis component (it rotates) that comes in two halves (half shafts) connected by the differential that delivers power to the driving wheels.
Steering system
The steering system has two types: the hydraulic type and the electric type which controls the vehicle’s direction.
Braking system
The braking system is responsible for reducing the vehicle’s speed by using friction to convert the wheel’s rotational energy into heat energy.
Types of Automotive Car Chassis
The chassis of a car is likened to its skeleton bearing the car’s weight. It has four main types that can determine the car’s performance and abilities. The four main types of car chassis are:
Ladder Frame Chassis
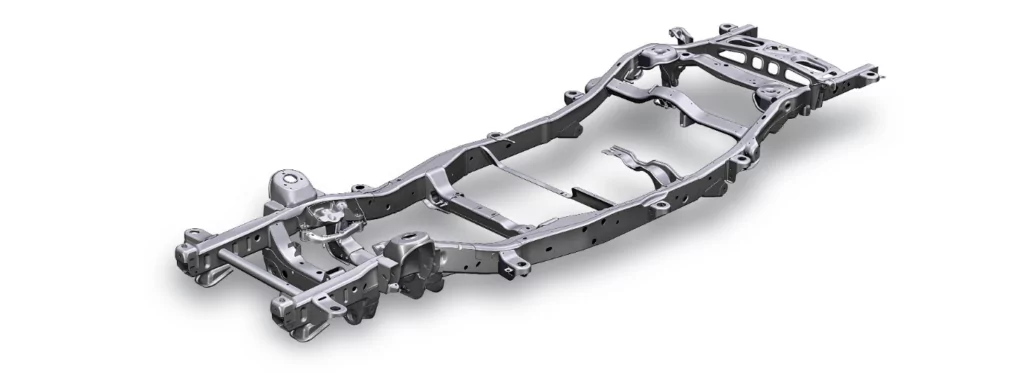
The ladder frame chassis has a unique ladder design (hence the name) and is the oldest chassis in the automobile industry. It is characterized by two long heavy beams supported by two smaller ones.
Based on the design, it is easy to construct, but it is very heavy and only suitable for large vehicles, such as trucks, trailers, etc., that carry heavy materials.
Benefits
- Easy construction and assembling process
- High structural integrity
Drawbacks
- Weak torsional rigidity
- Poor cornering ability
- Highly heavy, making it unsuitable for performance cars and hatchbacks.
Backbone Chassis
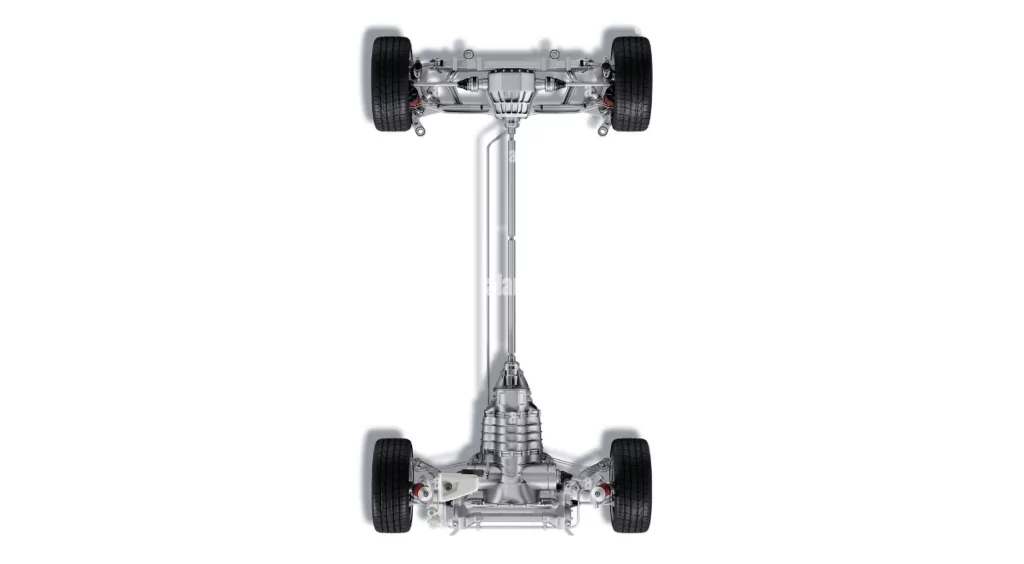
The backbone chassis is also named according to its shape, as it resembles the backbone of a human. It is a hollow cylindrical tube that connects the front and rear suspension. Also known as the single chassis, it is common in off-road cars due to its torsional toughness.
Benefits
- Preferable for off-road cars.
- High torsional toughness
Drawbacks
- If the driveshaft fails, the whole chassis will be dismantled
- High cost of manufacturing
Monocoque Chassis
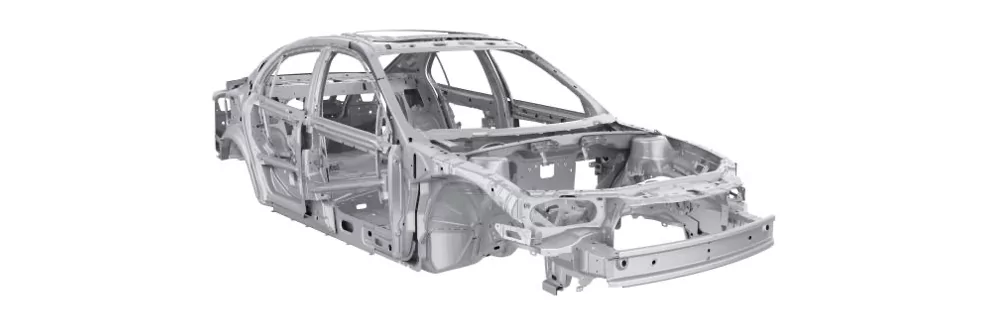
In the monocoque automobile chassis, the frame and the chassis come together to form a single shell. Also known as the unibody design, it is the most common chassis in modern normal cars such as SUVs, sedans, and cabs.
Benefits
- High torsional rigidity
- Safer due to its cage-like design
- Easy maintenance and repair
Drawbacks
- It is heavy due to the fused frame and chassis
Tubular Chassis
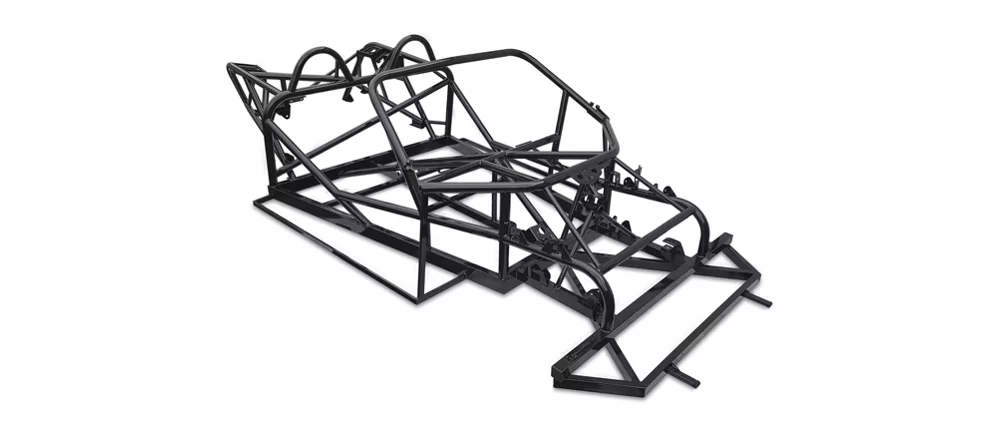
A tubular chassis is a 3D derivative of a ladder chassis made with tubular pipes (hence the name) with the vehicle component designed around the chassis. They are found in race cars because they are safer.
Benefits
- Higher rigidity than other frames with similar weight
- High strength-to-weight ratio
Drawbacks
- It has a complicated design and construction
- Unsuitable for mass production
- Used for drag and normal racing cars
- Difficulty in accessing the cabin due to elevated doors
Common Automotive Car Chassis Process
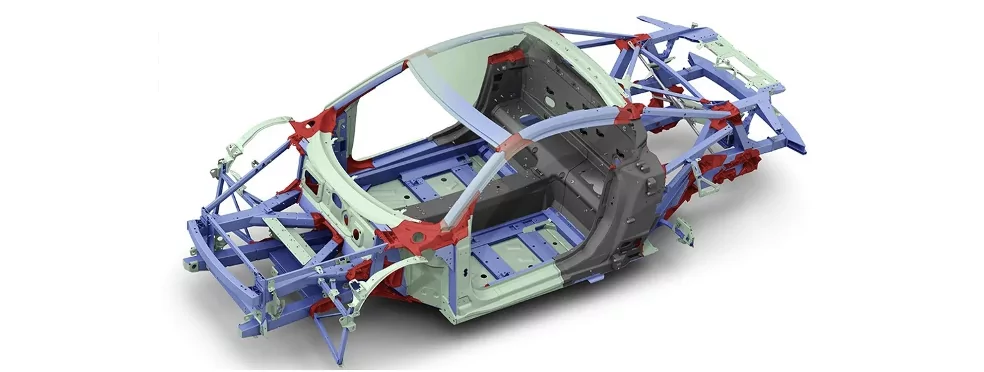
The car chassis process used in the automotive industry depends on factors such as the car chassis parts, types, make-up material, design, and production volume. Common manufacturing processes include:
Sheet Metal Fabrication
Sheet metal fabrication is a series of fabrication techniques integral to the automobile manufacturing industry and suitable for automobile chassis manufacturing. Sheet metal fabrication suitable for car chassis parts for chassis can be divided into three:
Cutting Techniques
Laser cutting, plasma cutting, and shearing are cutting techniques for making the chassis.
- Laser Cutting
The laser cutting technique uses a focused laser beam to melt and vaporize the sheet metal, leaving a precise cut. It is accurate and precise making it suitable for car chassis as it has a complex shape and requires tight tolerances
- Plasma Cutting
The plasma cutting technique uses plasma (high-velocity ionized gas) to cut sheet metal for making a car chassis. It is more suitable for thick materials but is also precise, accurate, and highly efficient.
- Shearing
The shearing technique uses a shearer to cut a sheet metal part. It is not as precise as the other two hence applicable in making chassis parts like the frame rail that do not require tight tolerance.
Forming Techniques
Cold-forming processes such as bending and stamping are used to shape the sheet metal to form chassis components:
- Bending
The bending technique uses a press brake machine to deform a sheet metal and create angles and curves to form the chassis part.
- Stamping
Stamping or pressing involves pressing a die into a sheet metal to create identical parts in high volumes.
Joining Techniques
Welding and riveting are sheet metal techniques for making and assembling the car chassis.
- Welding
The welding technique uses heat to join two parts of a chassis. Examples of welding techniques used in chassis manufacturing include TIG and MIG welding but the choice of welding technique depends on the materials.
- Riveting
Riveting involves inserting a rivet into a hole and deforming it to secure the formed joint. It is a better option for joining dissimilar metals and is used for joining the chassis and other automotive components.
CNC machining
In CNC machining, techniques like milling, turning, drilling, and lathing are used to manufacture and drill holes in parts of the chassis that need riveting.
Die Casting
In die casting, molten metal is injected into a mold, and on solidification, it takes the mold’s shape and design producing parts frame rails, and cross-members. Die casting is not popular in chassis construction because it cannot make the whole chassis.
Common Material for Car Chassis
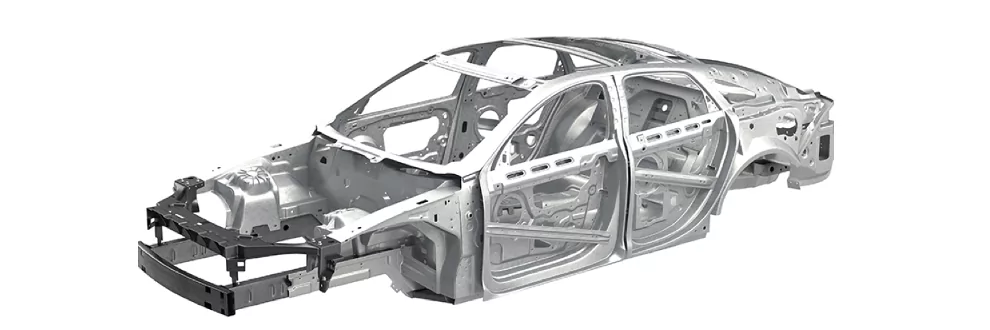
Many materials are used in making the car chassis and this section gives the common ones and their mechanical properties:
Steel
Steel has a high machinability and is the most common material for chassis construction. Several grades of steel include carbon steel which is strong, corrosion-resistant, durable, weldable, and formable, and low-carbon mild steel or plain carbon which is malleable, tough, and suitable for car chassis construction.
Aluminum
Aluminum is lightweight, strong, rigid, and suitable for making the car chassis because it is fuel-efficient and corrosion-resistant.
Composite materials
Composite materials such as carbon-fiber epoxy and glass-fiber composites are lightweight, strong, environmentally friendly, and popular but costly materials in chassis construction.
Magnesium alloys
Magnesium alloys such as AZ91D (an aluminum and magnesium alloy) are lightweight, strong, and corrosion-resistant, which makes them suitable for constructing the chassis of high-performance and race cars.
Common Surface Finishing for Car Chassis
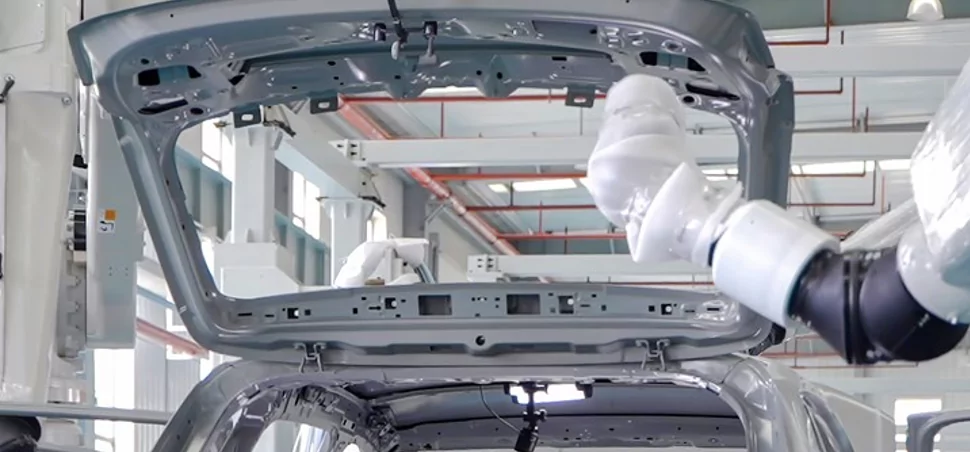
Automobile part manufacturers use surface finishing to improve the car chassis function:
Grinding
Grinding uses a flat lapping machine that removes surface defects by rubbing the workpiece surface against the lap of the machine through a layer of a mixture composed of abrasive material such as silicon carbide or diamond.
Polishing
Polishing is used in the final or later stages of the car chassis construction. It aims to improve small imperfections on the part that are not visible to the naked eye.
Galvanizing
In galvanization, you apply a zinc coating on the chassis parts to give a strong finish that is non-susceptible to corrosion and abrasion although when exposed, it can become damaged.
Anodizing
Anodizing is mostly used for aluminum chassis and it creates a thin, hard, and corrosion-resistant layer on the part so it can function in harsh environmental conditions. You can also also use the finishing option for zinc, titanium, and magnesium.
Painting
Painting involves coating parts of a chassis or the whole chassis with paint with long-term corrosion resistance properties.
Design Trend for Custom Car Chassis Parts
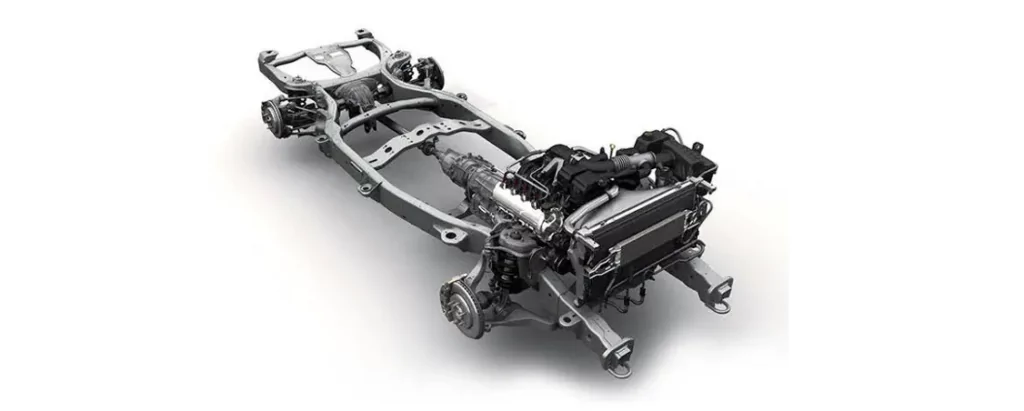
Design trends that will shape the future of automotive chassis design are:
The use of lightweight materials
Lightweight materials like aluminum, carbon fiber, and titanium for components like car chassis will reduce the vehicle’s weight without affecting the chassis’s structural integrity.
Integration of Electric Powertrains
Integrating electric powertrains into car chassis design will improve weight distribution, car handling, and fuel consumption efficiency.
Modular Chassis Platforms
With modular chassis platforms, automakers can use the same chassis for different car models causing increased flexibility and reducing production cost.
Connected Vehicle technology
Connected vehicle technology will improve the chassis design and driving experience as it enables remote diagnostic and predictive maintenance functions.
Safety Features
Safety features like collision warning and emergency braking incorporation into the automotive chassis design will lead to a better driving experience.
Conclusion
This article discusses the automotive chassis so readers can understand the structure, but choosing a reputable parts manufacturing service with automotive design experience can lead to quality chassis manufacturing. At Zintilon, we render quality-focused custom die casting and CNC machining processes for such people. Contact us today, and let us bring your project to life.
FAQs
Which types of car chassis are used for races?
The typical race car’s chassis is the tubular chassis, roll cage in off-road race cars, and the monocoque in Formula 1.
Where is the chassis number on my car?
The chassis number location depends on the model and makes of a car but common locations are on the dashboard at the bottom corner of the driver’s side, the driver’s door frame, and inside the engine bay.
Are car frames the same as car chassis?
No, both automotive components differ. The chassis of a car is the skeletal framework of the car that bears the car’s load and where components such as the steering system, braking system, rear axle, suspension, etc., are attached. In contrast, the frame is the car body where the chassis is attached. Until the 1940s, the chassis and frame were separate, and their fused form is now the monocoque frame or unibody car design.
Great, Together