Hogedrukgieten (HPDC) is uitgegroeid tot een toonaangevend productieproces voor de productie van dunwandige metalen onderdelen met een hoge maatnauwkeurigheid en een uitzonderlijke oppervlakteafwerking.
Deze methode wordt veel gebruikt in industrieën zoals automotive, aerospace en elektronica, waar gewichtsvermindering, structurele integriteit en esthetiek kritische factoren zijn. Het HPDC-proces is met name geschikt voor het produceren van componenten met wanddiktes variërend van 1 mm tot 5 mm.
In dit artikel bespreken we waarom spuitgieten onder hoge druk een ideale oplossing is voor de productie van dunwandige onderdelen, de belangrijkste voordelen die het biedt en waarom het de voorkeur geniet boven andere productietechnieken.
Overzicht van hogedrukspuitgieten
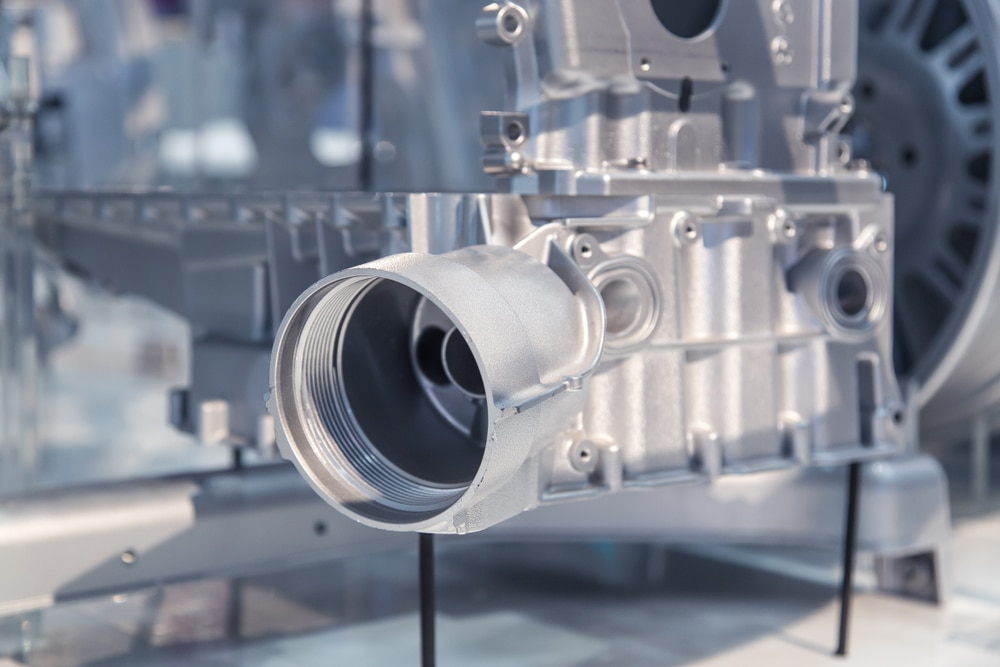
High-pressure die Casting (HPDC) is een precisieproductieproces waarbij gesmolten metaal onder hoge druk in een metalen mal wordt gespoten. Deze methode blinkt uit in het produceren van complexe, hoogwaardige componenten met uitstekende mechanische eigenschappen en oppervlakteafwerkingen.
HPDC is ideaal voor grootschalige productie vanwege de snelheid, herhaalbaarheid en herbruikbare gereedschapsstalen mallen. Het maakt het mogelijk om ingewikkelde vormen te creëren die met andere methoden moeilijk of duur zouden zijn.
Het proces ondersteunt verschillende non-ferro legeringen, wat flexibiliteit biedt voor specifieke onderdeelvereisten. HPDC-componenten zijn dicht, dimensionaal nauwkeurig en duurzaam, wat de nabewerkingsbehoeften minimaliseert. De efficiëntie en kwaliteit maken het essentieel voor industrieën zoals automotive, lucht- en ruimtevaart, elektronica en medische apparaten.
Hoe werkt het?
High-Pressure Die Casting (HPDC) is een populair productieproces dat wordt gebruikt om ingewikkelde metalen onderdelen met hoge precisie te produceren. Het proces omvat het injecteren van gesmolten metaal in een mal, of matrijs, onder hoge druk, wat resulteert in componenten met een gladde oppervlakteafwerking en uitstekende maatnauwkeurigheid. Hier is een stapsgewijs overzicht van hoe HPDC werkt:
- Selectie en voorbereiding van grondstoffen: Het proces begint met het selecteren van een geschikt ruw materiaal, meestal aluminium, magnesium of zinklegeringen, afhankelijk van de gewenste eigenschappen van het uiteindelijke onderdeel. Het gekozen metaal wordt gesmolten in een oven totdat het de juiste giettemperatuur bereikt, waardoor consistentie wordt gegarandeerd en verontreiniging wordt vermeden.
- Smelten en overbrengen: Zodra het metaal de juiste temperatuur heeft bereikt, wordt het voorzichtig overgebracht naar de gietmachine, waar het klaar is om in de matrijs te worden gespoten.
- Hogedrukinjectie: Het gesmolten metaal wordt met een hydraulische zuiger in de matrijs gespoten met een druk variërend van 700 tot 2000 bar. De hoge druk zorgt ervoor dat het metaal elke holte en elk detail vult, waardoor defecten zoals luchtzakken of porositeit worden voorkomen.
- Snelle afkoeling en stolling: Door het koelende effect van de metalen mal stolt het gesmolten metaal snel en ontstaat er een dicht en sterk onderdeel.
- Vorm openen en uitwerpen; Na het stollen wordt de mal geopend en wordt het gietstuk met behulp van uitwerppennen uitgeworpen. De cyclus duurt enkele seconden tot minuten.
Toepassingen
Hogedrukgieten (HPDC) wordt op grote schaal gebruikt in verschillende industrieën vanwege de precisie, efficiëntie en de mogelijkheid om complexe onderdelen te produceren.
- Automobielindustrie: HPDC is ideaal voor het maken van lichte, sterke componenten zoals motorblokken en transmissiebehuizingen, die het brandstofverbruik en de voertuigprestaties helpen verbeteren.
- Elektronische industrie: Het proces wordt gebruikt voor de productie van nauwkeurige behuizingen en connectoren, waardoor betrouwbare prestaties en pasvorm voor complexe elektronische assemblages worden gegarandeerd.
- Koellichamen: HPDC wordt ook veel gebruikt voor de productie van koellichamen, waarbij de dichte aard van de gietstukken zorgt voor een effectieve warmteafvoer.
- Luchtvaartsector: In de lucht- en ruimtevaartsector wordt HPDC gebruikt om zeer sterke onderdelen te maken die bestand zijn tegen extreme omstandigheden en voldoen aan strenge veiligheids- en prestatie-eisen.
- Consumentenproducten: HPDC wordt bij voorkeur gebruikt voor consumptiegoederen zoals apparaten en hardware, omdat het esthetisch aantrekkelijke, duurzame componenten met een glad oppervlak kan produceren.
Materialen
Hogedrukspuitgieten (HPDC) ondersteunt een reeks non-ferrometalen en legeringen, die elk geschikt zijn voor specifieke toepassingen:
- Aluminiumlegeringen: Lichtgewicht, corrosiebestendig en thermisch/elektrisch geleidend. Ideaal voor auto- en elektronische componenten.
- Magnesium legeringen: Lichter dan aluminium met een hoge stijfheid, perfect voor de lucht- en ruimtevaart en lichtgewicht auto-onderdelen.
- Zinklegeringen: Superieure bewerkbaarheid, slagvastheid en precisie. Veelvoorkomend voor kleine, ingewikkelde onderdelen zoals tandwielen en connectoren.
- Messing: Minder gebruikelijk vanwege hogere smeltpunten en kosten, maar gebruikt voor specifieke toepassingen waar deze eigenschappen vereist zijn.
De veelzijdigheid van het materiaal vergroot de aantrekkelijkheid van HPDC voor verschillende sectoren.
Oppervlakteafwerkingen
HPDC levert onderdelen met een uitstekende oppervlaktekwaliteit, waardoor vaak geen extra afwerking nodig is. De hoge druk zorgt voor gladde oppervlakken met minimale onvolkomenheden. Indien nodig kunnen secundaire processen zoals polijsten, verven, poedercoaten of anodiseren het uiterlijk en de duurzaamheid verbeteren. Deze afwerkingen maken HPDC-onderdelen geschikt voor zowel functioneel als decoratief gebruik.
Wat zijn de uitdagingen bij de productie van dunwandige onderdelen?
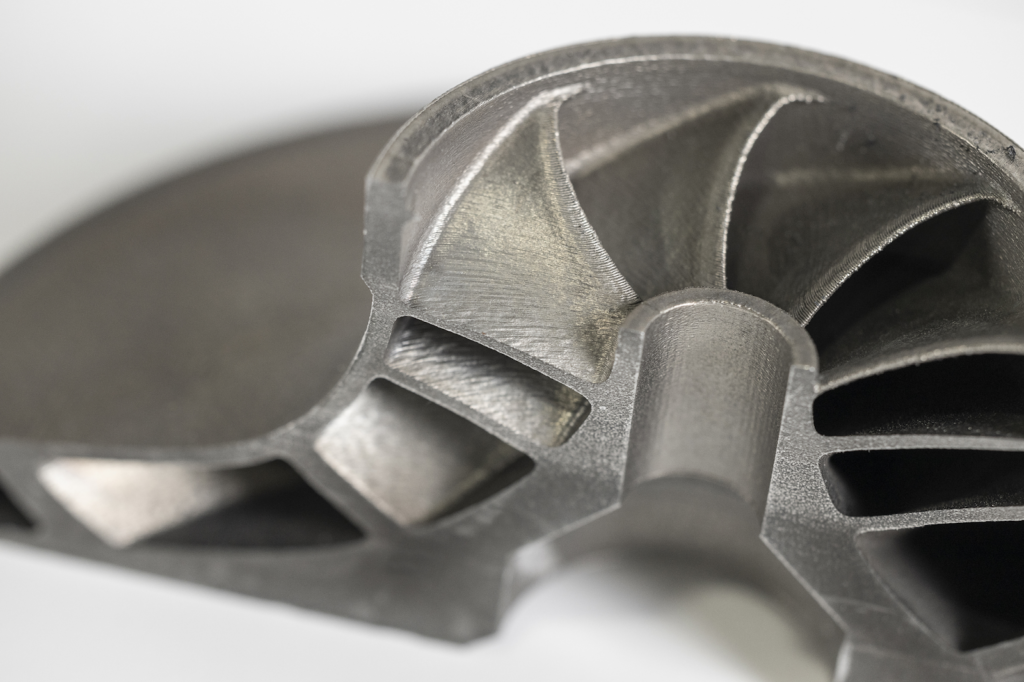
Het produceren van dunwandige onderdelen brengt unieke uitdagingen met zich mee die zorgvuldige overweging en geavanceerde technieken vereisen om aan te pakken. Deze uitdagingen komen voornamelijk voort uit de behoefte aan nauwkeurige controle over de materiaalstroom, koelsnelheden en dimensionale nauwkeurigheid, die cruciaal zijn voor het produceren van hoogwaardige componenten. Hieronder staan de belangrijkste uitdagingen die verband houden met de productie van dunwandige onderdelen:
Problemen met materiaalstroom en vulling
Bij dunwandige productie moet het gesmolten metaal in smalle en ingewikkelde delen van de mal stromen zonder voortijdig te stollen. Het bereiken van volledige en uniforme vulling is een uitdaging, omdat dunne delen snel afkoelen, waardoor het risico op defecten zoals onvolledige vulling, koude afsluitingen of porositeit toeneemt. Het garanderen van de juiste injectiedruk, snelheid en temperatuur is cruciaal om deze problemen te overwinnen.
Dimensionale stabiliteit en kromtrekken
Dunne wanden zijn gevoeliger voor vervorming of kromtrekken tijdens het stollen en afkoelen. De snelle afkoeling in deze secties kan interne spanningen veroorzaken, wat leidt tot dimensionale onnauwkeurigheden. Het beheersen van de afkoelsnelheid en het verzekeren van een uniforme thermische verdeling binnen de mal is essentieel om vervorming te minimaliseren.
Complexiteit van het matrijsontwerp
Het maken van matrijzen voor dunwandige onderdelen is inherent uitdagender vanwege de noodzaak van nauwkeurige toleranties en ingewikkelde kenmerken. Een goed ontwerp moet rekening houden met krimp van het materiaal, thermische spanningen en ontluchting om defecten te voorkomen en een hoge herhaalbaarheid te garanderen.
Verhoogd risico op defecten
Defecten zoals porositeit, scheuren of oppervlakte-imperfecties komen vaker voor bij dunwandige onderdelen vanwege het beperkte materiaalvolume en de hoge koelsnelheden. Geavanceerde procescontrole- en inspectietechnieken zijn nodig om dergelijke problemen te detecteren en te beperken.
Hogere eisen aan apparatuur
Voor het produceren van dunwandige onderdelen zijn hogedrukinjectiesystemen, geavanceerde gereedschappen en nauwkeurige temperatuurregelingen nodig. Deze apparatuur is kostbaar en vereist bekwame operators, wat de complexiteit en kosten van de productie verhoogt.
Ondanks deze uitdagingen pakt High Pressure Die Casting (HPDC) veel van deze problemen effectief aan, waardoor het een voorkeursmethode is voor het vervaardigen van dunwandige onderdelen. Laten we hier verderop meer over leren!
Is spuitgieten onder hoge druk geschikt voor dunwandige onderdelen?
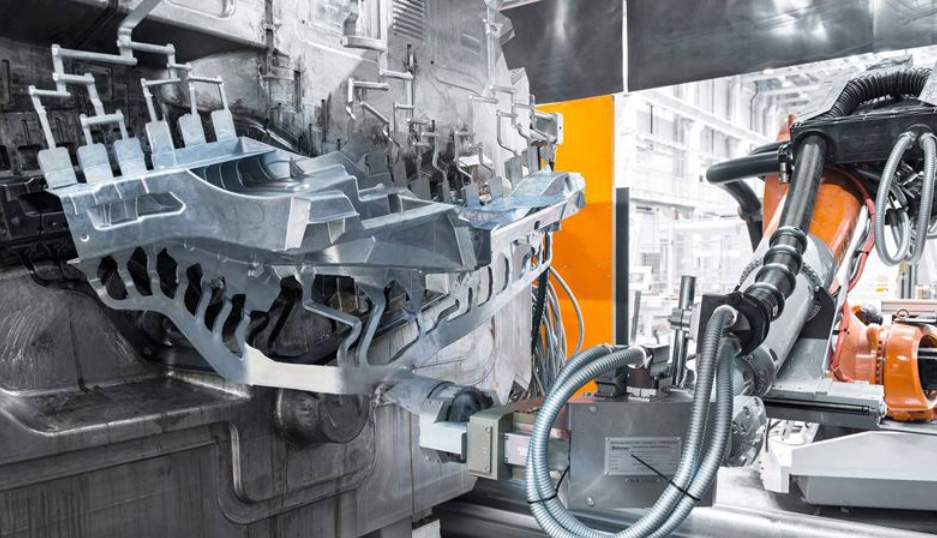
Ja, High Pressure Die Casting (HPDC) is een uitzonderlijk productieproces voor het produceren van dunwandige onderdelen, meestal variërend van 1 mm tot 5 mm dik. Het maakt gebruik van hogedrukinjectie om ervoor te zorgen dat gesmolten metaal soepel door zelfs de dunste delen van de mal stroomt, waardoor onderdelen met een uniforme wanddikte en consistente mechanische eigenschappen ontstaan. Dit is waarom HPDC uitblinkt in deze toepassing:
Precisie en maatnauwkeurigheid
HPDC levert ongeëvenaarde precisie, waardoor het ideaal is voor onderdelen die nauwe toleranties en consistente kwaliteit vereisen. Deze nauwkeurigheid pakt veelvoorkomende problemen met dunne wandproductie aan, zoals onvolledige vulling, koude sluitingen en porositeit, en zorgt voor defectvrije componenten. Met de juiste controle van druk, temperatuur en snelheid elimineert HPDC dimensionale variaties en produceert onderdelen die voldoen aan strenge eisen.
Vermogen om met complexe geometrieën om te gaan
Dunwandige onderdelen vereisen vaak gedetailleerde ontwerpen met dunne ribben, ondersnijdingen of scherpe hoeken. HPDC kan deze complexe geometrieën verwerken en tegelijkertijd de structurele integriteit van het onderdeel behouden. Dit maakt het een betrouwbare keuze voor toepassingen zoals auto-onderdelen, lucht- en ruimtevaartonderdelen en elektronische behuizingen, waar lichtgewicht maar zeer functionele ontwerpen essentieel zijn.
Hoge productie-efficiëntie
HPDC biedt snelle cyclustijden, wat de snelle productie van grote volumes dunwandige onderdelen met consistente kwaliteit mogelijk maakt. De herhaalbaarheid zorgt ervoor dat elk onderdeel identiek is, waardoor afval wordt verminderd en de efficiëntie wordt verbeterd. Het proces minimaliseert ook de behoefte aan extra bewerking of afwerking, wat helpt de productiekosten te verlagen.
Minder materiaalverspilling
In tegenstelling tot traditionele giettechnieken, maakt HPDC efficiënt gebruik van gesmolten metaal door het direct in de mal te injecteren. Dit minimaliseert afval en overtollig materiaal kan vaak worden gerecycled. Het verminderde afval bespaart niet alleen kosten, maar ondersteunt ook duurzame productiepraktijken.
Door uitdagingen zoals materiaalstroom, kromtrekken en defecten aan te pakken, is HPDC een betrouwbare en efficiënte oplossing voor het produceren van lichtgewicht, duurzame en complexe dunwandige onderdelen in alle sectoren. Of het nu gaat om automotive, elektronica of lucht- en ruimtevaart, HPDC levert consistente, hoogwaardige resultaten.
Voordelen van hogedrukspuitgieten voor dunwandige onderdelen
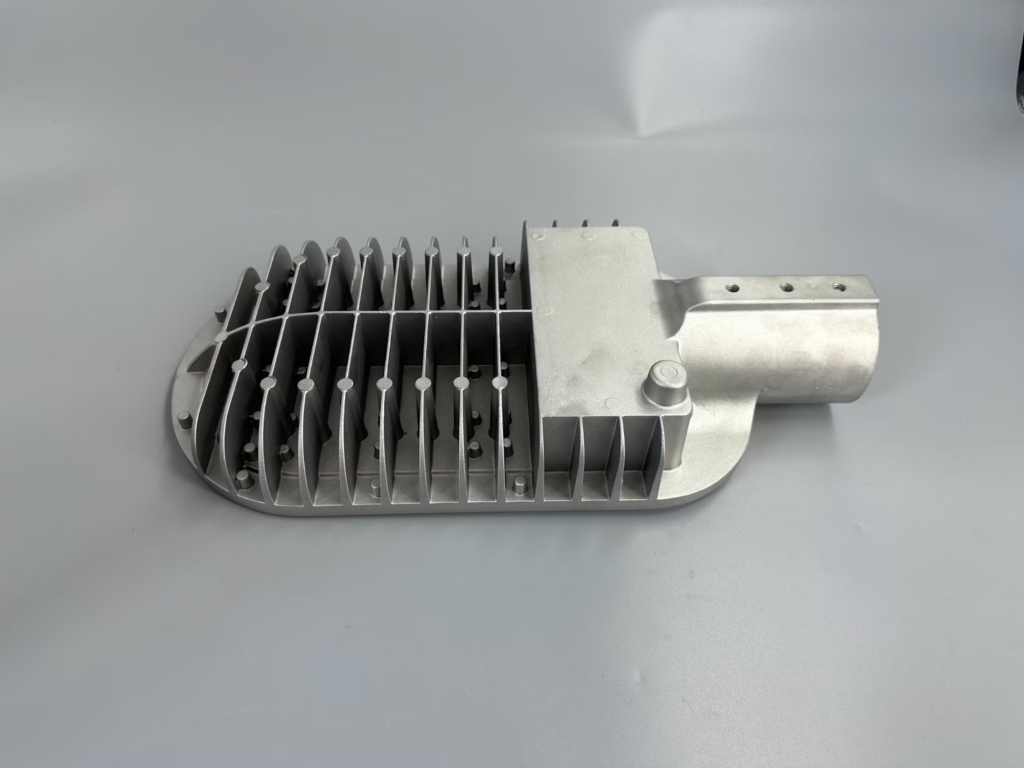
Hogedrukgieten (HPDC) is een van de meest effectieve productiemethoden voor het produceren van dunwandige onderdelen. Het biedt talloze voordelen waardoor het een populaire keuze is voor een breed scala aan industrieën.
Het vermogen om componenten te leveren met uitzonderlijke mechanische eigenschappen, nauwkeurige afmetingen en een hoge oppervlaktekwaliteit is met name gunstig voor toepassingen waarbij gewichtsvermindering en prestaties van cruciaal belang zijn. De volgende secties benadrukken de belangrijkste redenen waarom HPDC een geweldige keuze is voor het produceren van dunwandige onderdelen en wat het superieur maakt aan andere giet- en bewerkingstechnieken.
Superieure sterkte-gewichtsverhouding
Een van de grootste sterktes van HPDC ligt in het vermogen om componenten te produceren met een uitstekende sterkte-gewichtsverhouding. Wanneer gesmolten metaal onder hoge druk in de matrijs wordt geïnjecteerd, stolt het snel, waardoor een fijnkorrelige structuur ontstaat die de mechanische eigenschappen verbetert. Dit resulteert in lichtgewicht maar robuuste onderdelen die bestand zijn tegen hoge spanningen. Industrieën zoals de automobiel- en lucht- en ruimtevaart waarderen deze eigenschap voor toepassingen waarbij gewichtsvermindering vereist is zonder de structurele integriteit in gevaar te brengen.
Uitzonderlijke maatnauwkeurigheid en toleranties
HPDC staat bekend om zijn precisie. De stijve stalen mallen die in dit proces worden gebruikt, zorgen voor nauwe toleranties en minimale dimensionale variaties, zelfs voor componenten met dunne wanden. De nauwkeurigheid van HPDC vermindert de behoefte aan secundaire bewerkingen of nabewerkingen, wat zowel tijd als productiekosten bespaart. Industrieën zoals medische apparatuur en elektronica, waar nauwe toleranties cruciaal zijn, vertrouwen op HPDC voor consistente, hoogwaardige componenten.
Vermogen voor complexe geometrieën
HPDC kan componenten produceren met ingewikkelde vormen, zoals ondersnijdingen, dunne ribben en complexe interne kenmerken, die moeilijk of kostbaar zijn om te bereiken met andere productiemethoden. Voor dunwandige onderdelen maakt deze mogelijkheid het mogelijk om gedetailleerde ontwerpen te maken terwijl de structurele integriteit behouden blijft. Toepassingen zoals elektronische behuizingen en structurele beugels profiteren enorm van HPDC's vermogen om deze geavanceerde geometrieën met precisie te produceren.
Hoge productie-efficiëntie
HPDC is zeer efficiënt, met snelle cyclustijden en de mogelijkheid om snel grote hoeveelheden componenten te produceren. De geautomatiseerde aard van het proces zorgt voor consistente kwaliteit en herhaalbaarheid in productieruns. Dit maakt het een ideale keuze voor industrieën die werken met strakke schema's, waardoor fabrikanten grote orders en strakke deadlines kunnen halen en tegelijkertijd hoge kwaliteitsnormen kunnen handhaven.
Minimale materiaalverspilling
Vergeleken met andere gietmethoden is HPDC zeer efficiënt in het gebruik van materialen. Het gesmolten metaal wordt direct in de matrijs gespoten, waardoor materiaalverspilling wordt geminimaliseerd. Overtollig materiaal kan vaak worden gerecycled, wat kosten verlaagt en duurzame productiepraktijken ondersteunt. Dit voordeel is vooral waardevol voor industrieën die streven naar het minimaliseren van de impact op het milieu en tegelijkertijd het materiaalgebruik optimaliseren.
Verbeterde oppervlaktekwaliteit
HPDC levert onderdelen met gladde, defectvrije oppervlakken. Deze hoge oppervlaktekwaliteit vermindert de noodzaak voor nabewerking, wat de productiekosten en doorlooptijden verder verlaagt. Bovendien verbetert de dichte structuur van HPDC-onderdelen hun esthetische aantrekkingskracht en maakt ze ideaal voor zichtbare toepassingen, zoals consumentenelektronica of autobekleding. Gladde oppervlakken vergemakkelijken ook een betere hechting voor coatings of lakken, wat de duurzaamheid en het uiterlijk verbetert.
Verbeterde thermische en elektrische geleidbaarheid
De dichte, uniforme structuur van HPDC-onderdelen zorgt voor uitstekende thermische en elektrische geleidbaarheid, waardoor het proces ideaal is voor componenten zoals koellichamen en elektronische behuizingen. Dunwandige ontwerpen profiteren vooral van deze eigenschap, omdat lichtgewicht componenten kunnen worden geproduceerd zonder dat dit ten koste gaat van de prestaties. HPDC-onderdelen zorgen voor optimale thermische dissipatie en elektrische prestaties, cruciaal in toepassingen zoals LED-behuizingen en motorbehuizingen.
Conclusie
High Pressure Die Casting is een zeer geschikte methode voor het produceren van dunwandige onderdelen met hoge precisie, uitstekende oppervlakteafwerkingen en robuuste mechanische eigenschappen. De mogelijkheid om complexe geometrieën te creëren en nauwe toleranties te handhaven, maakt het een ideale keuze voor industrieën zoals automotive, aerospace en elektronica.
Bedrijven die op zoek zijn naar betrouwbare HPDC-services kunnen terecht bij Zintilon, een bedrijf dat bekendstaat om zijn expertise in precisiegieten en toewijding aan het leveren van hoogwaardige componenten. Met een team van bekwame professionals en geavanceerde faciliteiten biedt Zintilon uitgebreide HPDC-oplossingen die zijn afgestemd op de unieke vereisten van elke klant, waardoor de best mogelijke resultaten voor de productie van dunwandige onderdelen worden gegarandeerd.
Geweldig, Samen