La fundición a presión de alta presión (HPDC) ha surgido como un proceso de fabricación líder para producir piezas metálicas de paredes delgadas con alta precisión dimensional y un acabado superficial excepcional.
Este método se utiliza ampliamente en industrias como la automotriz, la aeroespacial y la electrónica, donde la reducción de peso, la integridad estructural y la estética son factores críticos. El proceso HPDC es especialmente adecuado para producir componentes con espesores de pared que van desde 1 mm hasta 5 mm.
En este artículo, exploraremos por qué la fundición a presión de alta presión es una solución ideal para la producción de piezas de paredes delgadas, los beneficios clave que ofrece y por qué se prefiere a otras técnicas de fabricación.
Descripción general de la fundición a presión a alta presión
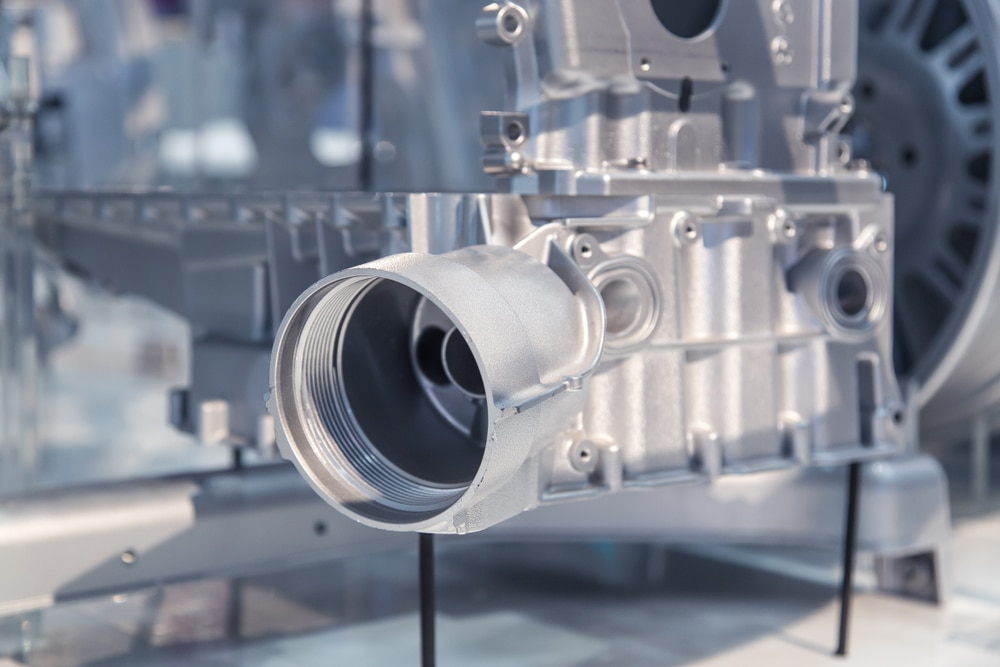
La fundición a presión a alta presión (HPDC) es un proceso de fabricación de precisión en el que se inyecta metal fundido en un molde metálico a alta presión. Este método se destaca en la producción de componentes complejos y de alta calidad con excelentes propiedades mecánicas y acabados superficiales.
El HPDC es ideal para la producción de gran volumen debido a su velocidad, repetibilidad y moldes de acero reutilizables. Permite la creación de formas complejas que serían difíciles o costosas con otros métodos.
El proceso admite diversas aleaciones no ferrosas, lo que ofrece flexibilidad para requisitos específicos de las piezas. Los componentes HPDC son densos, dimensionalmente precisos y duraderos, lo que minimiza las necesidades de posprocesamiento. Su eficiencia y calidad lo hacen esencial para industrias como la automotriz, la aeroespacial, la electrónica y los dispositivos médicos.
¿Cómo funciona?
La fundición a presión a alta presión (HPDC) es un proceso de fabricación popular que se utiliza para producir piezas metálicas complejas con gran precisión. El proceso implica inyectar metal fundido en un molde o matriz a alta presión, lo que da como resultado componentes con un acabado superficial suave y una excelente precisión dimensional. A continuación, se ofrece una descripción general paso a paso de cómo funciona la HPDC:
- Selección y preparación de materia prima: El proceso comienza con la selección de una materia prima adecuada, normalmente aleaciones de aluminio, magnesio o zinc, en función de las propiedades deseadas para la pieza final. El metal elegido se funde en un horno hasta alcanzar la temperatura de fundición adecuada, asegurando la consistencia y evitando la contaminación.
- Fusión y transferencia: Una vez que el metal alcanza la temperatura correcta, se transfiere cuidadosamente a la máquina de fundición, donde está listo para ser inyectado en la matriz.
- Inyección de alta presión: El metal fundido se inyecta en el molde a presiones que van desde los 700 a los 2000 bares mediante un pistón hidráulico. La alta presión garantiza que el metal llene cada cavidad y detalle, evitando defectos como bolsas de aire o porosidad.
- Enfriamiento y solidificación rápidos: Debido al efecto de enfriamiento del molde de metal, el metal fundido se solidifica rápidamente, formando un componente denso y fuerte.
- Apertura y expulsión de moldes; Después de la solidificación, se abre el molde y se expulsa la pieza fundida mediante pasadores eyectores, completando el ciclo en segundos o minutos.
Aplicaciones
La fundición a presión de alta presión (HPDC) se utiliza ampliamente en diversas industrias por su precisión, eficiencia y capacidad para producir piezas complejas.
- Industria automotriz: HPDC es ideal para crear componentes livianos y resistentes como bloques de motor y carcasas de transmisión, que ayudan a mejorar la eficiencia del combustible y el rendimiento del vehículo.
- Industria electrónica: El proceso se utiliza para producir carcasas y conectores precisos, lo que garantiza un rendimiento confiable y un ajuste perfecto para conjuntos electrónicos complejos.
- Disipadores de calor: El HPDC también se utiliza ampliamente para la fabricación de disipadores de calor, donde la naturaleza densa de las piezas fundidas garantiza una disipación de calor efectiva.
- Sector Aeroespacial: En el sector aeroespacial, el HPDC se utiliza para crear piezas de alta resistencia que pueden soportar condiciones extremas, cumpliendo estrictos estándares de seguridad y rendimiento.
- Productos de consumo: El HPDC se prefiere para bienes de consumo como electrodomésticos y hardware debido a su capacidad de producir componentes estéticamente atractivos y duraderos con acabados de superficie suaves.
Materiales
La fundición a presión a alta presión (HPDC) admite una variedad de metales y aleaciones no ferrosos, cada uno adecuado para aplicaciones específicas:
- Aleaciones de aluminio: Ligero, resistente a la corrosión y conductor térmico y eléctrico. Ideal para componentes electrónicos y automotrices.
- Aleaciones de magnesio:Más ligero que el aluminio con alta rigidez, perfecto para la industria aeroespacial y piezas automotrices ligeras.
- Aleaciones de Zinc:Mecanización superior, resistencia al impacto y precisión. Común para piezas pequeñas e intrincadas como engranajes y conectores.
- Cobre y Latón:Menos común debido a sus puntos de fusión más altos y al costo, pero se utiliza para aplicaciones específicas que requieren sus propiedades.
La versatilidad del material aumenta el atractivo del HPDC en todas las industrias.
Acabados Superficiales
HPDC ofrece piezas con una excelente calidad de superficie, lo que a menudo elimina la necesidad de un acabado adicional. Las altas presiones garantizan superficies lisas con imperfecciones mínimas. Cuando es necesario, los procesos secundarios como el pulido, la pintura, el recubrimiento en polvo o el anodizado pueden mejorar la apariencia y la durabilidad. Estos acabados hacen que las piezas HPDC sean adecuadas tanto para usos funcionales como decorativos.
¿Cuáles son los desafíos de la fabricación de piezas de paredes delgadas?
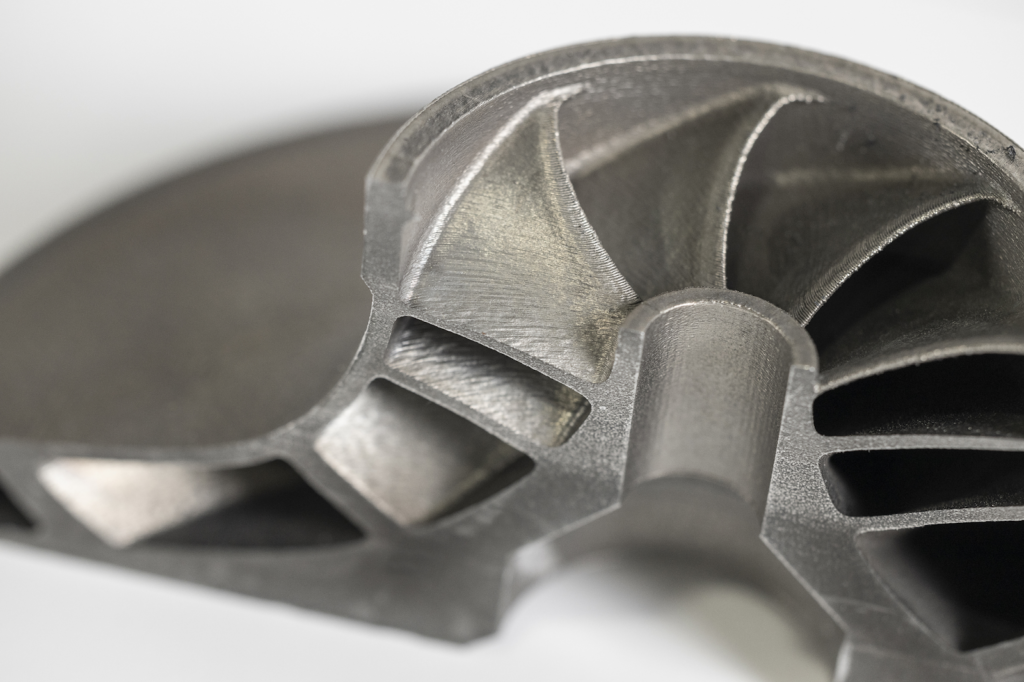
La fabricación de piezas de pared delgada presenta desafíos únicos que requieren una consideración cuidadosa y técnicas avanzadas para abordarlos. Estos desafíos surgen principalmente de la necesidad de un control preciso sobre el flujo de material, las velocidades de enfriamiento y la precisión dimensional, que son fundamentales para producir componentes de alta calidad. A continuación, se presentan los desafíos clave asociados con la producción de piezas de pared delgada:
Problemas de llenado y flujo de materiales
En la fabricación de paredes delgadas, el metal fundido debe fluir hacia secciones estrechas e intrincadas del molde sin solidificarse prematuramente. Lograr un llenado completo y uniforme es un desafío porque las secciones delgadas se enfrían rápidamente, lo que aumenta el riesgo de defectos como llenado incompleto, cierres en frío o porosidad. Garantizar la presión, la velocidad y la temperatura de inyección correctas es crucial para superar estos problemas.
Estabilidad dimensional y deformación
Las paredes delgadas son más susceptibles a deformarse o deformarse durante la solidificación y el enfriamiento. El enfriamiento rápido en estas secciones puede provocar tensiones internas, lo que genera imprecisiones dimensionales. Controlar la velocidad de enfriamiento y garantizar una distribución térmica uniforme dentro del molde es esencial para minimizar la distorsión.
Complejidad del diseño de matrices
La creación de matrices para piezas de paredes delgadas es inherentemente más complicada debido a la necesidad de tolerancias precisas y características intrincadas. Un diseño adecuado debe tener en cuenta la contracción del material, las tensiones térmicas y la ventilación para evitar defectos y garantizar una alta repetibilidad.
Mayor riesgo de defectos
Los defectos como porosidad, grietas o imperfecciones superficiales son más comunes en piezas de paredes delgadas debido al volumen limitado de material y a las altas velocidades de enfriamiento. Se necesitan técnicas avanzadas de control e inspección de procesos para detectar y mitigar estos problemas.
Mayores demandas de equipamiento
La producción de piezas de paredes delgadas requiere sistemas de inyección de alta presión, herramientas avanzadas y controles de temperatura precisos. Este equipo es costoso y requiere operadores capacitados, lo que aumenta la complejidad y los gastos de producción.
A pesar de estos desafíos, la fundición a alta presión (HPDC) resuelve eficazmente muchos de estos problemas, lo que la convierte en el método preferido para fabricar piezas de paredes delgadas. ¡Aprendamos más sobre esto más adelante!
¿Es la fundición a presión a alta presión una buena opción para piezas de paredes delgadas?
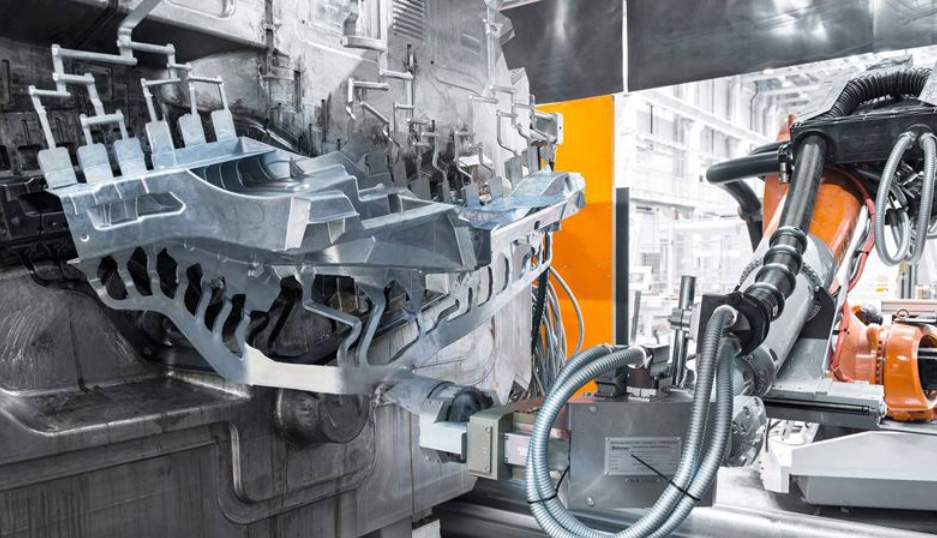
Sí, la fundición a presión a alta presión (HPDC) es un proceso de fabricación excepcional para producir piezas de paredes delgadas, que suelen tener un espesor de entre 1 mm y 5 mm. Utiliza inyección a alta presión para garantizar que el metal fundido fluya sin problemas incluso en las secciones más delgadas del molde, creando piezas con un espesor de pared uniforme y propiedades mecánicas consistentes. A continuación, se explica por qué la HPDC se destaca en esta aplicación:
Precisión y exactitud dimensional
El HPDC ofrece una precisión inigualable, lo que lo hace ideal para piezas que exigen tolerancias estrictas y una calidad constante. Esta precisión soluciona problemas comunes en la fabricación de paredes delgadas, como el llenado incompleto, los cierres en frío y la porosidad, lo que garantiza componentes sin defectos. Con el control adecuado de la presión, la temperatura y la velocidad, el HPDC elimina las variaciones dimensionales y produce piezas que cumplen con los requisitos estrictos.
Capacidad para manejar geometrías complejas
Las piezas de paredes delgadas suelen requerir diseños detallados con nervaduras finas, socavados o esquinas agudas. El HPDC es capaz de manejar estas geometrías complejas y, al mismo tiempo, mantener la integridad estructural de la pieza. Esto lo convierte en una opción confiable para aplicaciones como componentes automotrices, piezas aeroespaciales y carcasas electrónicas, donde los diseños livianos pero altamente funcionales son esenciales.
Alta eficiencia de producción
El HPDC ofrece tiempos de ciclo rápidos, lo que permite la producción rápida de grandes volúmenes de piezas de pared delgada con una calidad constante. Su repetibilidad garantiza que cada pieza sea idéntica, lo que reduce el desperdicio y mejora la eficiencia. El proceso también minimiza la necesidad de mecanizado o acabado adicional, lo que ayuda a reducir los costos de producción.
Desperdicio de material reducido
A diferencia de las técnicas de fundición tradicionales, la HPDC utiliza de manera eficiente el metal fundido inyectándolo directamente en el molde. Esto minimiza los desechos y, a menudo, cualquier exceso de material se puede reciclar. La reducción de desechos no solo ahorra costos, sino que también respalda las prácticas de fabricación sustentables.
Al abordar desafíos como el flujo de material, la deformación y los defectos, la HPDC es una solución confiable y eficiente para producir piezas livianas, duraderas y complejas de paredes delgadas en todas las industrias. Ya sea para la industria automotriz, electrónica o aeroespacial, la HPDC ofrece resultados consistentes y de alta calidad.
Beneficios de la fundición a presión de alta presión para piezas de paredes delgadas
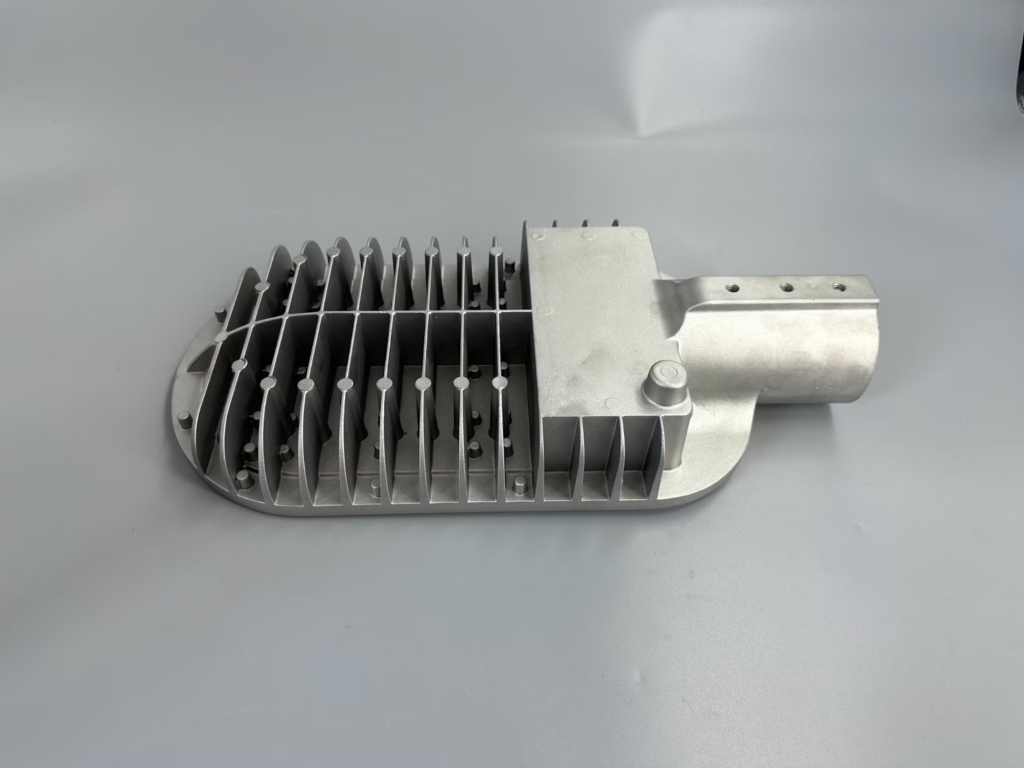
La fundición a alta presión (HPDC) se destaca como uno de los métodos de fabricación más efectivos para producir piezas de paredes delgadas, ofreciendo numerosas ventajas que lo convierten en la opción preferida para una amplia gama de industrias.
Su capacidad para producir componentes con propiedades mecánicas excepcionales, dimensiones precisas y alta calidad de superficie es particularmente beneficiosa para aplicaciones donde la reducción de peso y el rendimiento son consideraciones críticas. Las siguientes secciones destacan las razones clave por las que la HPDC es una excelente opción para fabricar piezas de paredes delgadas y lo que la hace superior a otras técnicas de fundición y mecanizado.
Relación superior fuerza-peso
Una de las mayores ventajas del HPDC reside en su capacidad para producir componentes con una excelente relación resistencia-peso. Cuando se inyecta metal fundido en la matriz a altas presiones, se solidifica rápidamente, creando una estructura de grano fino que mejora las propiedades mecánicas. Esto da como resultado piezas ligeras pero robustas capaces de soportar altas tensiones. Industrias como la automotriz y la aeroespacial valoran esta característica para aplicaciones que requieren reducción de peso sin comprometer la integridad estructural.
Precisión dimensional y tolerancias excepcionales
El HPDC es reconocido por su precisión. Los moldes de acero rígidos utilizados en este proceso garantizan tolerancias estrictas y variaciones dimensionales mínimas, incluso para componentes con paredes delgadas. La precisión del HPDC reduce la necesidad de operaciones de mecanizado o acabado secundarias, lo que permite ahorrar tiempo y costos de producción. Industrias como la de dispositivos médicos y electrónica, donde las tolerancias estrictas son fundamentales, confían en el HPDC para obtener componentes consistentes y de alta calidad.
Capacidad para geometrías complejas
La tecnología HPDC puede producir componentes con formas intrincadas, como socavados, nervaduras delgadas y características internas complejas, que son difíciles o costosas de lograr con otros métodos de fabricación. Para piezas de paredes delgadas, esta capacidad permite la creación de diseños detallados manteniendo la integridad estructural. Aplicaciones como carcasas electrónicas y soportes estructurales se benefician enormemente de la capacidad de la tecnología HPDC para producir estas geometrías sofisticadas con precisión.
Alta eficiencia de producción
El HPDC es altamente eficiente, con tiempos de ciclo rápidos y la capacidad de producir grandes cantidades de componentes rápidamente. La naturaleza automatizada del proceso garantiza una calidad constante y repetibilidad en todas las tiradas de producción. Esto lo convierte en una opción ideal para las industrias que operan con plazos ajustados, lo que permite a los fabricantes cumplir con pedidos grandes y plazos ajustados manteniendo altos estándares de calidad.
Residuos mínimos de material
En comparación con otros métodos de fundición, la HPDC es muy eficiente en el uso de materiales. El metal fundido se inyecta directamente en la matriz, lo que minimiza el desperdicio de material. El material sobrante suele reciclarse, lo que reduce los costos y respalda las prácticas de producción sostenibles. Este beneficio es especialmente valioso para las industrias que buscan minimizar el impacto ambiental y optimizar el uso de materiales.
Calidad de superficie mejorada
El HPDC ofrece piezas con superficies lisas y sin defectos. Esta alta calidad de superficie reduce la necesidad de posprocesamiento, lo que reduce aún más los costos de producción y los plazos de entrega. Además, la estructura densa de las piezas HPDC mejora su atractivo estético y las hace ideales para aplicaciones visibles, como productos electrónicos de consumo o molduras de automóviles. Las superficies lisas también facilitan una mejor adhesión de los recubrimientos o pinturas, lo que mejora la durabilidad y la apariencia.
Conductividad térmica y eléctrica mejorada
La estructura densa y uniforme de las piezas HPDC garantiza una excelente conductividad térmica y eléctrica, lo que hace que el proceso sea ideal para componentes como disipadores de calor y carcasas electrónicas. Los diseños de pared delgada se benefician especialmente de esta propiedad, ya que se pueden producir componentes livianos sin sacrificar el rendimiento. Las piezas HPDC garantizan una disipación térmica y un rendimiento eléctrico óptimos, fundamentales en aplicaciones como carcasas de LED y carcasas de motores.
Conclusión
La fundición a presión a alta presión es un método muy adecuado para producir piezas de paredes delgadas con alta precisión, excelentes acabados superficiales y propiedades mecánicas robustas. Su capacidad para crear geometrías complejas y mantener tolerancias estrictas lo convierte en una opción ideal para industrias como la automotriz, la aeroespacial y la electrónica.
Las empresas que buscan servicios de HPDC confiables pueden recurrir a Zintilon, una empresa conocida por su experiencia en fundición de precisión y su compromiso con la entrega de componentes de alta calidad. Con un equipo de profesionales capacitados e instalaciones avanzadas, Zintilon ofrece soluciones integrales de HPDC personalizadas según los requisitos únicos de cada cliente, lo que garantiza los mejores resultados posibles para la producción de piezas de pared delgada.
Genial, juntos