Wenn Sie nach der perfekten Technik zum Herstellen dünnwandiger Teile suchen, stoßen Sie häufig auf das Niederdruckgussverfahren. Es ist ein sehr effektives Gussverfahren zur Herstellung hochwertiger Teile. Aber ist Niederdruckguss auch für dünnwandige Teile geeignet?
Die klare Antwort lautet nein. Es ist jedoch auch wichtig zu verstehen, warum dies für dünnwandige Teile nicht die beste Option ist. Deshalb gehen wir näher auf die Niederdruckgusstechnik ein und erklären Ihnen alles über diese Technik und warum sie für solche Teile nicht geeignet ist.
Übersicht zum Niederdruckguss
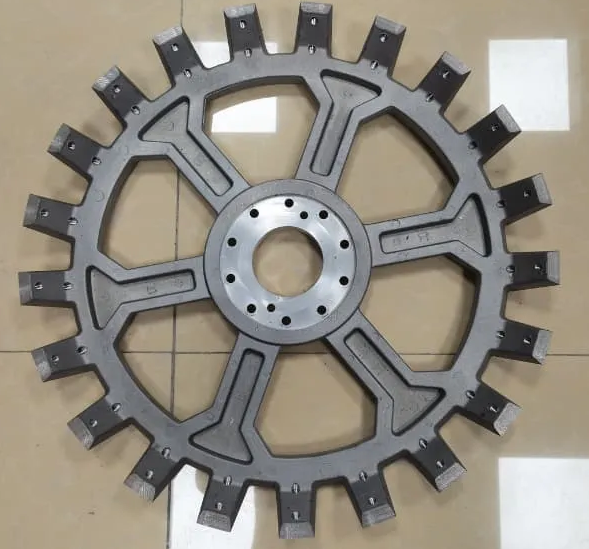
Niederdruckguss ist ein Metallgussverfahren, das in den letzten Jahren aufgrund seiner einzigartigen Vorteile an Popularität gewonnen hat. Wenn Sie verschiedene Fertigungstechniken erkunden, werden Sie feststellen, dass diese Methode eine Kombination aus Präzision, Effizienz und Kosteneffizienz bietet, die sie für viele Anwendungen attraktiv macht.
So funktioniert es
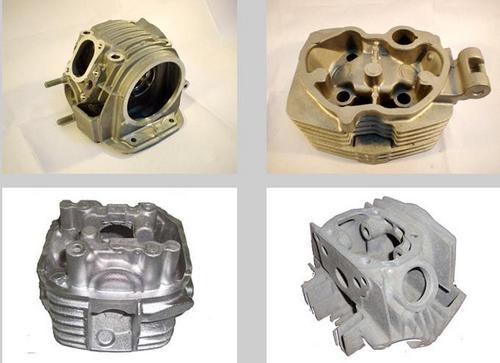
Um die Möglichkeiten und Grenzen des Niederdruckgusses vollständig zu verstehen, ist es wichtig, zu verstehen, wie der Prozess funktioniert. Hier finden Sie eine Übersicht über den Niederdruckgussprozess.
- Formvorbereitung: Der Prozess beginnt mit der Vorbereitung einer präzisionsgefertigten Stahlform. Diese Form wird gründlich gereinigt und vorgewärmt, um thermische Spannungen zu vermeiden.
- Metallschmelzen und -übertragung: Anschließend schmelzen Sie das ausgewählte Metall und füllen es vorsichtig in einen Warmhalteofen, um eine schlackenfreie Versorgung mit geschmolzenem Metall sicherzustellen.
- Kontrollierte Injektion: Anschließend wird das geschmolzene Metall vorsichtig und unter geringem Druck in die Formhöhle gespritzt, um den Lufteinschluss auf ein Minimum zu reduzieren.
- Erstarrung: Das Metall erstarrt allmählich in der Form, wobei der Warmhalteofen kontinuierlich geschmolzenes Metall nachführt, um die Schrumpfung auszugleichen.
- Teileauswurf: Sobald das Teil erstarrt ist, werfen Sie es aus der Matrize und lassen die Matrize vor dem nächsten Zyklus abkühlen.
- Finishing: Um die gewünschte Oberflächenqualität zu erreichen, müssen Sie möglicherweise geringfügige Zuschneide- und Bearbeitungsvorgänge durchführen.
Anwendungen
Sie haben vielleicht schon einmal Niederdruckgussverfahren gesehen, aber nie gewusst, dass sie auf diese Weise hergestellt werden. Hier sind einige Branchen, in denen Niederdruckgussteile ständig verwendet werden.
- Automobil: Produziert Motorblöcke, Zylinderköpfe, Räder und Aufhängungskomponenten.
- Luft- und Raumfahrt: Wird für Fahrwerke, Motorteile und andere hochpräzise Komponenten verwendet.
- Medizinisch: Stellt chirurgische Instrumente, Röntgengeräte und andere medizinische Geräte her.
- Haushaltsgeräte: Erstellt Teile für Kochgeräte, Küchenmaschinen und andere Haushaltsgegenstände.
- Elektrisch: Produziert Motorgehäuse, Abdeckungen und andere elektrische Komponenten.
- Marine: Wird zur Herstellung von Pumpen, Motoren und Ventilen für Schiffsanwendungen verwendet.
Materialien
Lassen Sie uns nun die verschiedenen Materialien besprechen, die mit dem Druckgussverfahren kompatibel sind. Bestimmte Materialien eignen sich am besten für das Verfahren, und dazu gehören in der Regel:
Werkstoff | Vorteile |
Aluminiumlegierungen | Am häufigsten, ausgewogenes Eigenschaftsverhältnis, breites Anwendungsspektrum |
Magnesiumlegierungen | Höchstes Verhältnis von Festigkeit zu Gewicht, ideal für gewichtskritische Anwendungen |
Zinklegierungen | Hohe Maßgenauigkeit, hervorragende Oberflächengüte, niedriger Schmelzpunkt |
Kupferlegierungen | Höhere Festigkeit und Temperaturbeständigkeit |
Oberflächenveredelungen
Wenn Sie Druckguss für Ihr Projekt in Betracht ziehen, ist es wichtig, die verschiedenen verfügbaren Oberflächenveredelungen zu kennen. Hier sind einige Oberflächenveredelungen, die Sie ausprobieren können –
Wie gegossen
Einfaches, raues Finish direkt aus der Form. Dies ist die wirtschaftlichste Option, ist aber möglicherweise nicht für Anwendungen geeignet, die genaue Abmessungen oder glatte Oberflächen erfordern.
Texturing
Fügt Muster oder Texturen durch Formmodifikationen hinzu. Dies kann den Griff verbessern, die Ästhetik aufwerten oder kleinere Unvollkommenheiten kaschieren.
Polieren
Erzeugt eine glatte, glänzende Oberfläche. Polieren wird häufig für dekorative Teile oder Anwendungen verwendet, die ein hohes Reflexionsvermögen erfordern.
Kugelstrahlen
Verbessert das Aussehen und die mechanischen Eigenschaften. Durch Kugelstrahlen können Oberflächenverunreinigungen entfernt, die Dauerfestigkeit verbessert und eine gleichmäßige Oberflächenstruktur erzeugt werden.
Vibrationsbearbeitung
Ideal für komplexe Formen und große Stückzahlen. Mit diesem Verfahren können Teile entgratet, scharfe Kanten entfernt und die Oberflächenbeschaffenheit verbessert werden.
Lackierung/Beschichtung
Verbessert die Korrosionsbeständigkeit, verleiht Farbe und verbessert die Ästhetik. Zu den üblichen Beschichtungen gehören Pulverbeschichtung, Nasslackierung, Eloxieren und Galvanisieren.
Was sind die Herausforderungen bei der Herstellung dünnwandiger Teile?
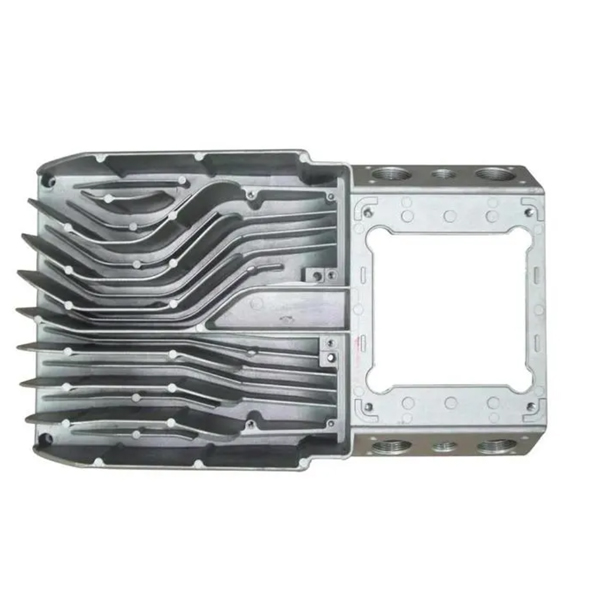
Wenn Sie vorhaben, dünnwandige Teile herzustellen, müssen Sie sich auf die folgenden Herausforderungen vorbereiten. Dies sind häufige Probleme, die bei der Herstellung dünnwandiger Teile auftreten
Probleme mit dem Materialfluss
Bei dünnen Abschnitten ist es eine große Herausforderung, eine vollständige und gleichmäßige Füllung mit geschmolzenem Material sicherzustellen. Das hohe Verhältnis von Oberfläche zu Volumen dünner Wände führt zu einem schnellen Wärmeverlust, wodurch die Viskosität des geschmolzenen Materials steigt und sein Fluss behindert wird. Dies kann zu einer unvollständigen Füllung der Formhöhle führen und im Endteil Hohlräume oder dünne Bereiche hinterlassen.
Ungleichmäßige Kühlung
Aufgrund ihrer geringen Dicke kühlen diese Teile viel schneller ab als dickere Abschnitte. Diese schnelle Abkühlung erzeugt ungleichmäßige Temperaturgradienten innerhalb des Teils, was zu unterschiedlicher Schrumpfung und der Möglichkeit von Verformungen, Verzerrungen und der Bildung von Einfallstellen führt. Die ungleichmäßige Abkühlung kann auch innere Spannungen im Teil verursachen, die seine Festigkeit und Haltbarkeit beeinträchtigen können.
Verzerrung und Verzerrung
Die erheblichen Temperaturgradienten während der Abkühlung können zu unterschiedlichen Schrumpfungen des Teils führen. Diese unterschiedlichen Schrumpfungen können zu Verformungen führen, bei denen sich das Teil verbiegt oder verdreht. Komplexe Geometrien und unterschiedliche Wandstärken verschärfen diese Probleme und machen es schwieriger, die endgültige Form des Teils vorherzusagen und zu kontrollieren.
Einfallstellen
Wenn dünne Abschnitte schnell abkühlen, schrumpfen sie schneller als die umgebenden dickeren Abschnitte. Diese unterschiedliche Schrumpfung kann dazu führen, dass sich die dickeren Abschnitte von den dünneren Abschnitten lösen, wodurch Vertiefungen oder „Einfallstellen“ auf der Oberfläche des Teils entstehen. Diese Einfallstellen können optisch unansehnlich sein und auch die Funktionalität des Teils beeinträchtigen.
Tor Design
Die richtige Angusskonstruktion ist entscheidend für die vollständige und gleichmäßige Füllung dünnwandiger Abschnitte. Position, Größe und Form des Angusses können den Materialfluss, die Druckverteilung und die Gesamtqualität des Teils erheblich beeinflussen. Die Optimierung der Angusskonstruktion erfordert eine sorgfältige Berücksichtigung von Faktoren wie Teilegeometrie, Materialeigenschaften und Verarbeitungsbedingungen.
Auswurfherausforderungen
Das Auswerfen dünnwandiger Teile aus der Form kann aufgrund ihrer empfindlichen Beschaffenheit eine Herausforderung darstellen. Die dünnen Wände können beim Auswerfen leicht verformt oder beschädigt werden, insbesondere wenn die Auswurfkräfte nicht sorgfältig kontrolliert werden. Um Teileschäden zu minimieren, können spezielle Auswurfsysteme wie Niederkraftauswerfer oder pneumatische Systeme erforderlich sein.
Ist Niederdruck-Kokillenguss für dünnwandige Teile geeignet?
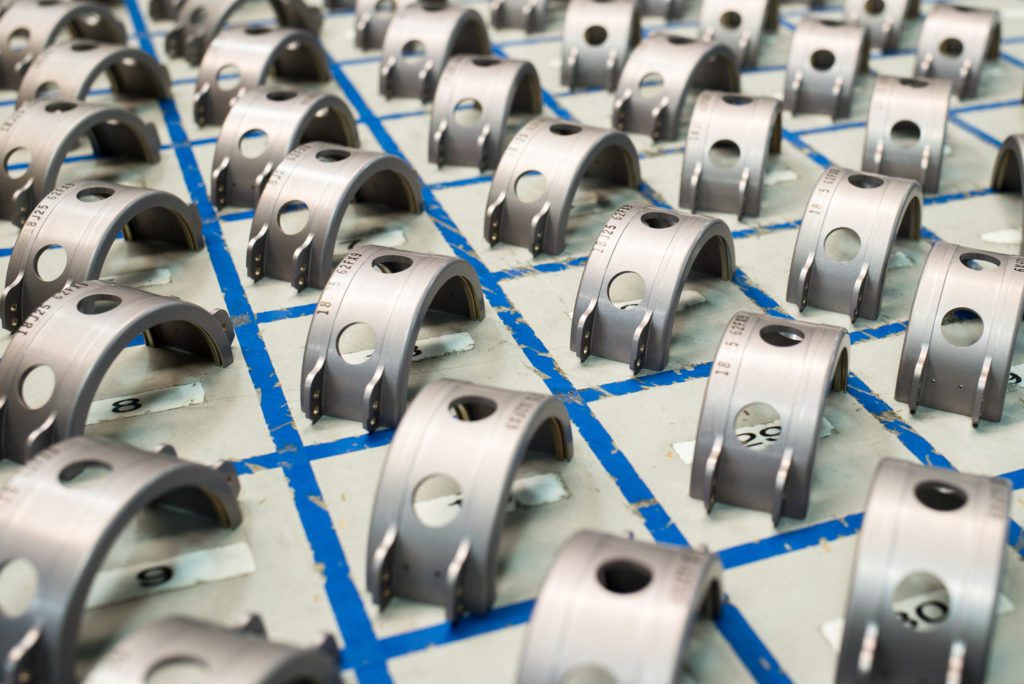
Kommen wir nun zur zentralen Frage dieses Artikels: Ist Niederdruckguss für dünnwandige Teile geeignet? Die kurze Antwort lautet: Nein, Niederdruckguss ist im Allgemeinen nicht gut für die Herstellung von Teilen mit sehr dünnen Wänden geeignet. Die Technik hat mehrere Einschränkungen.
Einschränkungen des Niederdruckgusses
Aufgrund der Einschränkungen beim Niederdruckguss treten im Prozess einige entscheidende Probleme auf. Dazu gehören:
Begrenzte Fähigkeit zum Füllen sehr dünner Abschnitte
Erstens reicht der relativ niedrige Druck beim LPDC möglicherweise nicht aus, um extrem dünne Abschnitte vollständig zu füllen, insbesondere solche im Bereich von 1–5 mm.
Sie werden Probleme mit dem Mangel an Kraft im geschmolzenen Metall haben. Es wird nicht in der Lage sein, die Oberflächenspannung zu überwinden und in die engsten Bereiche der Formhöhle zu fließen. Dies führt schließlich zu Problemen wie unvollständiger Füllung, Hohlräumen und potenziellen Defekten.
Potenzial für Verformungen und Verzerrungen
Wie wir oben besprochen haben, sind Verformungen und Verzerrungen bei der Herstellung dünnwandiger Teile sehr häufige Probleme. Obwohl LPDC Turbulenzen minimiert, kann der langsamere Füllprozess dennoch zu einem gewissen Grad ungleichmäßiger Abkühlung führen.
Diese Ungleichmäßigkeit trägt enorm zum Verziehen und Verformen bei, insbesondere bei Teilen mit komplexer Geometrie oder großen Unterschieden in der Wandstärke.
Darüber hinaus kann durch die langsamere Abkühlung das Risiko steigen, dass sich im Teil innere Spannungen bilden, die nach dem Auswerfen zu Verformungen führen können.
Langsamere Produktionsraten
Das Niederdruck-Einspritzverfahren führt naturgemäß zu längeren Füllzeiten im Vergleich zum Hochdruck-Druckguss. Dies führt zu längeren Zykluszeiten und niedrigeren Produktionsraten. Obwohl dies an sich kein großes Problem darstellt, kann es dennoch schwierig sein, Teile in großen Stückzahlen herzustellen.
Wie geht man mit den Einschränkungen des Niederdruckgusses um?
Wenn Sie nun darauf bestehen, Niederdruckguss zur Herstellung dünnwandiger Teile zu verwenden, können Sie einige Strategien ausprobieren. Diese können Ihnen helfen, die Probleme bis zu einem gewissen Grad zu umgehen und anständige Ergebnisse zu erzielen. Sie lauten wie folgt:
Optimierung des Formendesigns
Die Optimierung des Formendesigns Ihres Niederdruckgusses kann eine nützliche Strategie für den Niederdruckguss dünnwandiger Teile sein. Folgendes können Sie tun:
- Verwenden Sie mehrere kleinere Angussöffnungen, um das geschmolzene Metall gleichmäßig zu verteilen und Lufteinschlüsse zu minimieren. Wählen Sie die Angussöffnungen sorgfältig aus, um Bindenähte zu vermeiden und eine vollständige Füllung sicherzustellen.
- Entwerfen Sie Kühlkanäle präzise, um Wärme effizient abzuleiten, eine gleichmäßige Kühlung zu fördern und thermische Spannungen zu minimieren. Erwägen Sie die Verwendung von konturnahen Kühlkanälen für eine gleichmäßigere Wärmeableitung.
- Sorgen Sie für eine ausreichende Entlüftung, damit die Luft aus der Formhöhle entweichen kann. So wird ein Lufteinschluss verhindert und eine vollständige und gleichmäßige Füllung dünner Abschnitte sichergestellt.
Materialauswahl
Sie können die Erfolgsquote Ihres Projekts bereits vor dessen Beginn durch eine strategische Materialauswahl steigern. Dazu müssen Sie –
- Wählen Sie Legierungen mit niedriger Viskosität, die ihre Fließfähigkeit verbessern und es ihnen ermöglichen, dünne Abschnitte effektiver zu füllen.
- Wählen Sie Materialien mit geringer Erstarrungsschrumpfung, um das Risiko von Verzügen und Maßungenauigkeiten zu minimieren.
Prozessoptimierung
Während des Niederdruckgussverfahrens können Sie einige wichtige Optimierungsstrategien umsetzen. Sie können beispielsweise:
- Reduzieren Sie den Einspritzdruck leicht, um Turbulenzen zu minimieren und den Materialfluss in dünne Abschnitte zu verbessern, während Sie gleichzeitig ausreichend Druck für eine vollständige Füllung aufrechterhalten.
- Implementieren Sie kontrollierte Kühltechniken, wie beispielsweise den Einsatz von Kühlern oder Wärmedämmung, um die Abkühlrate zu regulieren und das Risiko einer ungleichmäßigen Abkühlung und von Verformungen zu verringern.
Spezialwerkzeuge
Und nicht zuletzt kann der Einsatz spezieller Werkzeugtaktiken Ihnen auch dabei helfen, die Auswirkungen von LPDC-Einschränkungen zu mildern. Sie können –
- Verwenden Sie spezielle Einsätze in der Form, um dünnen Abschnitten zusätzlichen Halt zu verleihen und so eine Verformung beim Auswerfen zu verhindern.
- Um das Risiko einer Beschädigung dünnwandiger Teile beim Auswerfen zu minimieren, verwenden Sie Niederdruck-Auswurfsysteme oder pneumatische Systeme.
Welche Vorteile bietet der Niederdruckguss für dünnwandige Teile?
Hier ist der Punkt: Niederdruckguss ist vielleicht nicht die beste Lösung für dünnwandige Teile, aber es bietet dennoch einige wichtige Vorteile. Diese Vorteile sind dieser Fertigungstechnik inhärent. Zu den Vorteilen, die Sie erhalten, gehören:
Reduzierte Porosität
Das langsame und kontrollierte Füllen der Form unter niedrigem Druck minimiert das Risiko von Turbulenzen und Lufteinschlüssen, was zu einer deutlich geringeren Porosität im Endprodukt führt. Dies ist bei dünnwandigen Teilen von entscheidender Bedeutung, da Porosität die Struktur schwächen und ihre Integrität beeinträchtigen kann.
Verbesserter Materialfluss
Der sanfte und gleichmäßige Fluss des geschmolzenen Metalls unter niedrigem Druck ermöglicht eine bessere Füllung komplexer und dünnwandiger Abschnitte. Dies verringert die Wahrscheinlichkeit unvollständiger Füllungen, Kaltverklebungen und Fehlläufe, gewährleistet eine gleichmäßige Wandstärke und minimiert Defekte.
Verbesserte Maßgenauigkeit
Der kontrollierte Erstarrungsprozess unter niedrigem Druck sorgt für eine gleichmäßigere Abkühlung und verringerte Schrumpfung, was zu einer verbesserten Maßgenauigkeit und engeren Toleranzen führt. Dies ist besonders wichtig für dünnwandige Teile, bei denen selbst kleine Maßabweichungen ihre Funktionalität beeinträchtigen können.
Verbesserte Oberflächengüte
Die langsamere Füllrate und die reduzierte Turbulenz beim LPDC tragen zu einer glatteren Oberfläche der Gussteile bei. Dadurch kann der Bedarf an umfangreichen Nachbearbeitungsvorgängen wie Zerspanen oder Schleifen minimiert werden, die bei dünnwandigen Bauteilen anspruchsvoll und kostspielig sein können.
Vielseitigkeit
LPDC kann zum Gießen einer großen Bandbreite von Metallen verwendet werden, darunter Aluminium-, Magnesium- und Kupferlegierungen, und ist daher für verschiedene Anwendungen und Materialanforderungen geeignet.
Schlussfolgerung
Zusammenfassend lässt sich sagen, dass Niederdruckguss zwar nicht die ideale Wahl ist, in manchen Fällen aber dennoch zum Erfolg führen kann. Mit den inhärenten Vorteilen dieser Technik können Sie mithilfe der besprochenen Strategien qualitativ hochwertige Dünnwandteile herstellen. Auf diese Weise müssen Sie nicht nach anderen Methoden zur Herstellung von Dünnwandteilen suchen.
Wenn Sie jedoch den größtmöglichen Nutzen aus Ihren dünnwandigen Teilen ziehen möchten, kann Druckguss eine hervorragende Lösung für Sie sein. In dieser ausführlichen Diskussion erfahren Sie, warum sich Druckguss für dünnwandige Teile gut eignet.
Großartig, zusammen